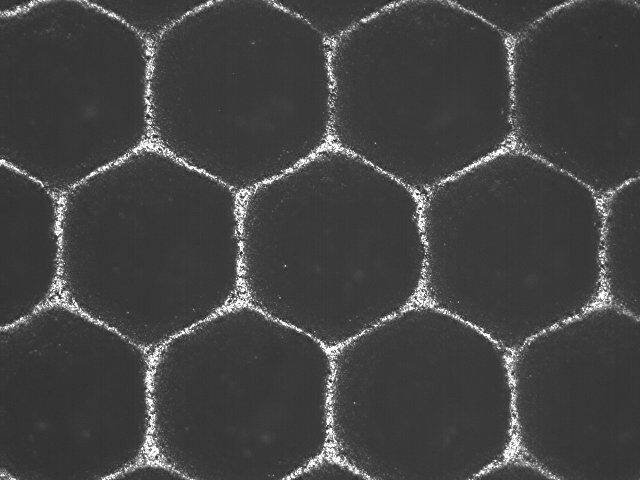
In flexographic printing, the 60° Hex anilox engraving has become an extremely popular cell shape for many reasons. The six-sided polygon is a proven geometry, in nature and printing, to hold liquid effectively. The purpose of the anilox is to pick up ink from the ink pan or chamber and release it to the plate in a uniform layer. A 60° Hex anilox completes this process diligently.
Apex International is the world’s largest manufacturer of quality anilox solutions. We offer a wide variety of anilox engravings including, our patented GTT 2.0 open channel, 60° Hex, 45°, Longcell, Channellox, Trihelical, 60° Bottoms Up, 45° Bottoms Up, along with many custom engraving options. In this blog, we’ll dive into the advantages of the hexagon geometry and understand the various nuances of this anilox engraving.
To view an educational infographic on the different anilox geometries, view the download here.
The Hexagon Anilox Cell
The hexagon geometry is a six-sided polygon with sides of equal lengths and internal angles of 120 degrees. The hexagon is an efficient and structurally sound configuration found in both man-made structures and nature: honeycombs, snowflakes and other microscopic structures. Hex patterns can fit together without any gaps creating perfect tessellation and increasing cell density on the roll for high ink delivery.
In flexo printing, the hex 60° engraving is known for increased cell density, uniform ink pickup and release, strong structural integrity, efficient volume control and ink adaptability. With more cells per square inch, precision cell volume control and more, the hexagon shape has been the gold standard for anilox cell engravings in a variety of print applications for many years.
What The Hex!
Though an efficient and effective geometry, the hexagon shape does have some shortcomings when it comes to print.
Complex manufacturing process. The precision required to engrave hexagonal cells at a 60-degree angle requires special equipment and diligent quality control. Not all anilox manufacturers can achieve the uniformity needed for an effective hex anilox engraving. If not formatted correctly, laser engraving technologies can engrave the cell too deep or pointy or make the walls too thick, reducing its effectiveness and increasing waste.
- Ink distribution and release. While hexagonal cells are excellent at picking up precise volumes of ink, their honeycomb design inherently traps both liquid and air. This can lead to inefficient ink release, as the cells act like air pumps, introducing countless micro air bubbles into the ink as it passes through the doctor blade chamber. Consequently, some printers need to increase cell volume and adjust other variables to enhance ink release. Additionally, the walled structure of hexagonal cells can contribute to problems such as ink foaming and spitting. Learn more in this Apex blog.
- Doctor Blade Wear. Though the 6-wall structure maintains the structural integrity of the anilox roll for longer life, printers may end up with increased downtime for blade changes. Depending on the level of polishing that is applied after laser engraving, the honeycomb grid of the anilox can grind the steel or polymer blade material down as it rotates on press, much quicker than other geometries. As the blade wears, the uniformity and precision of the ink
laydown regresses, and the press must be stopped for another change.
- Cleaning & Set Up Difficulties. As stated, the hexagon geometry is built for holding liquid within the cell. Therefore, it is tougher to clean the ink out of a hexagon geometry. Ink residues can become trapped more easily at the cell corners and bottom requiring more intensive cleaning. Set up of a hex 60° anilox requires more finesse as well. Misalignment or incorrect pressure can cause ink transfer issues and downtime.
Not all hex-cell aniloxes are the same! There is much more to an anilox than LPI and BCM values. Apex anilox solutions have gone through rigorous research and development to help minimize the known concerns of hex cell engravings. Seeing is believing when it comes to cell shape which is why we have invested in multiple 3DQC Veritas™ Digital Microscopes for use in the field.
UltraCell Hex Technology
Manufactured using advanced multi-phase laser engraving technology, the UltraCell anilox line from Apex takes conventional hex engravings to the next level! UltraCell aniloxes are engraved slower to create a melted / fused inner cell wall that requires no additional porosity-masking sealants. This controlled engraving process allows a pure ceramic cell with more efficient ink or coating transfer, easier roll cleaning, and ultra resistance to anilox corrosion and scoring.
UltraCell hex engravings are innovated with an increase in cell width and decrease in cell depth to improve ink release efficiency and maximize ink mileage and print performance. This wider and shallower cell shape modification makes these aniloxes easier to clean and maintain as well. With UltraCell, printers and converters can reduce waste and improve their bottom line by using less ink, increasing press speed, and decreasing downtime for maintenance, cleaning and troubleshooting. All Apex UltraCell aniloxes go through a rigorous quality control process as well to ensure the utmost precision, durability and uniformity of the cells.
Printers looking to eliminate the downfalls of a six-sided cell engraving altogether have opted for Apex’s patented GTT 2.0 open slalom channel engraving. By removing 66% of the cell walls and leaving an open “S”-like channel, this cell geometry offers the most effective ink release, press performance and anilox cleaning in the market today. Learn more in this blog.
What’s a Hex got to do with flexo printing? A LOT! If you feel your hex anilox engraving isn’t meeting the demands of your print environment, talk to your Apex Anilox Specialist to discuss if UltraCell or GTT 2.0 is a better solution for your needs.