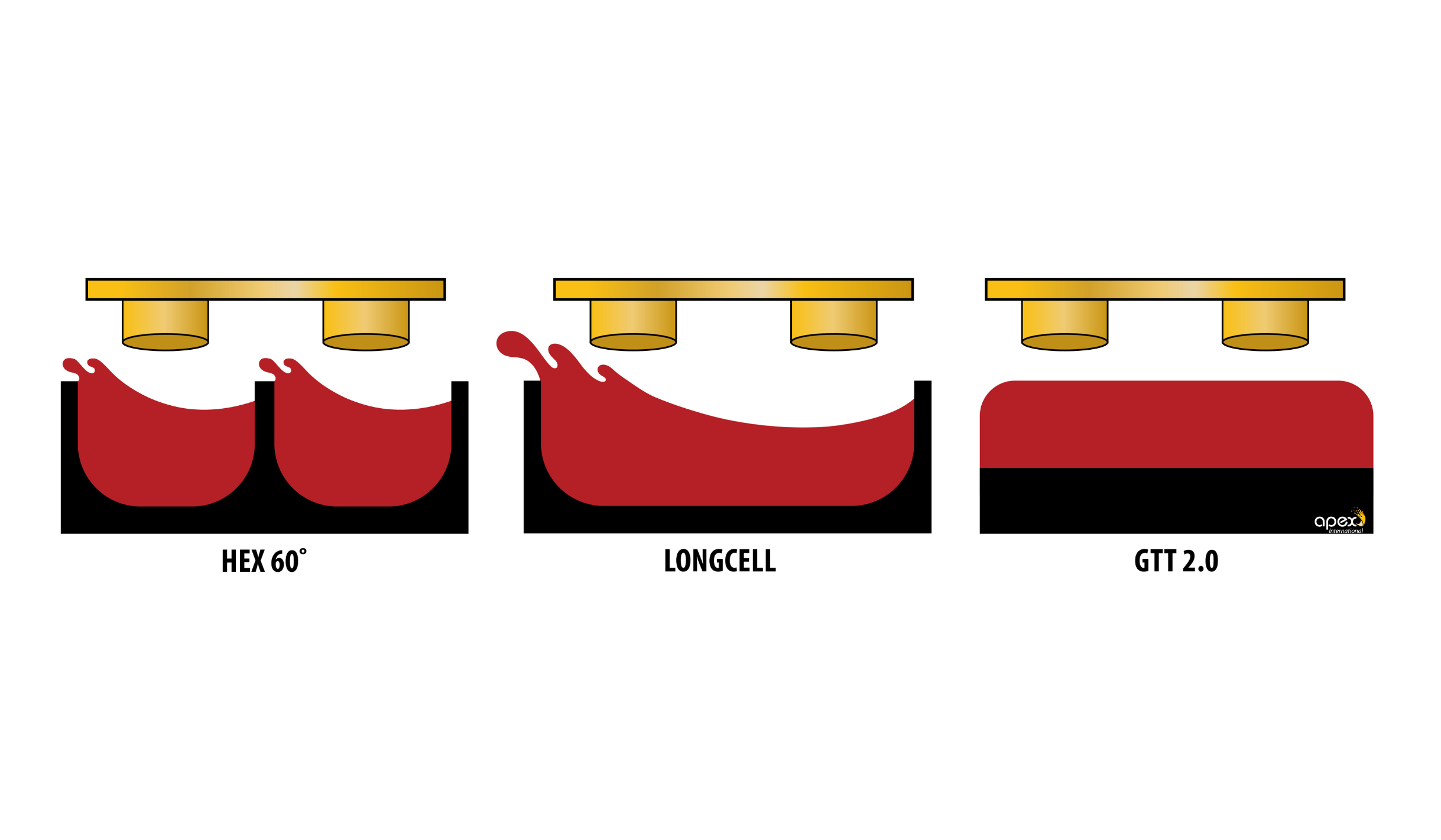
The anilox plays a critical role in determining the success or failure of your ECG printing endeavors. This particular method of fixed color flexo printing demands a higher degree of process control. Factors such as anilox volume, cell shape, and overall quality can significantly affect print quality and press performance.
For the 85% of printers who have attempted to transition to extended color gamut but ultimately reverted back to spot color printing, the missing piece of the puzzle might have been your choice of anilox partner. As a leading global innovator in anilox technology, Apex has developed the GTT 2.0 open slalom channel engraving as a proven solution for ECG printing challenges. Let's delve deeper into the forces influencing ink transfer to fully grasp the importance of this innovative anilox solution.
The Forces of ECG Printing
With the extended color gamut printing method, any inconsistencies related to the anilox ink transfer are magnified since spot colors now are created from a blend of YMCK + OGV. As a result, the techniques and procedures you have historically used in spot color printing may no longer be fit for ECG or any color-building printing. To understand what's missing, we must grasp the factors involved in ink transfer.
Centrifugal Force
As the anilox rotates, the ink contained within its cells is pushed outward, away from the center of rotation. This outward movement of liquid induced by the anilox's rotation is referred to as centrifugal force (Figure 1). To illustrate further, think back to the sensation of being pushed outward while riding on the rails of a merry-go-round or carousel during your childhood playground days. As the anilox continues to spin, the ink is compelled to move outward. In ECG printing, maintaining precise control and consistency in ink transfer is crucial for achieving desired results and ensuring color accuracy.
Closed Cell Engravings
To understand anilox ink transfer you must consider two critical aspects:
1. Applied Forces
In traditional cell-based engravings used in flexo printing, centrifugal force and G-force push the ink within the cells both upward and backward. This combined action, known as double force, causes the ink in the anilox cells to rise when it hits the back wall. With a 60° Hex engraving, the ink travels a shorter distance before lifting when it hits the back wall. Conversely, Longcell engravings allow the ink to travel further, building more momentum upon hitting the back wall, resulting in increased ink lift (Figure 2).
This lifting motion leads to various print defects. When the flexo plate contacts the anilox, dots may submerge into these raised ink bubbles on the anilox surface, leading to over-inking (Figure 3).
2. Ink Aeration
In all cell-based engravings, it is crucial to understand that tiny air bubbles, also known as micro bubbles, can be trapped inside the anilox cells during print production. This can lead to several issues such as ink foaming, ink lifting from the cells, pinholes, and uneven ink transfer. An important point to note is that anilox cells are never empty; they always contain either ink, solvent, or air inside them. After the ink is transferred to the printing plate, the cells become filled with air, which is then drawn into the doctor blade chamber due to the high speed of rotation of the anilox.
Some printers try to resolve these issues by either slowing down the press or adding special additives into the ink. However, these solutions often result in reduced press efficiency and reduced profitability. The buildup of micro bubbles within the ink chamber is increased at faster printing speeds.
Press Speed
ECG printing is more profitable at speed. The appeal of this printing method is based on reducing changeovers and increasing press speeds for maximum throughput. If optimized correctly, the anilox and CMYK + OGV inks can remain on press for every flexo print job, significantly improving uptime and profitability. However, if you are using a 60° Hex or Longcell engraving, you can often experience issues such as color variations from anilox to anilox. Also, ECG printing becomes more difficult when the anilox spins faster and faster as the press speed increases. Just like in the sport of Formula 1 Racing, the attention to detail required for the ECG printing process is both critical and essential if you want to be successful.
The Missing Link in ECG Printing
Understanding the recent developments and added complexity with ECG versus the lack of anilox innovation in the industry, it becomes clear why 85% of printers revert back to spot color printing. There is a missing piece, and Apex is committed to filling that gap.
For over a decade, Apex International has pioneered a proprietary open-channel engraving geometry to address the challenges faced by anilox and inking systems. Through extensive research and development, the patented GTT 2.0 anilox engraving was created as a solution for ECG printing and a versatile print solution overall. The concept behind this geometry is straightforward: by eliminating obstructive walls and designing perfectly angled curves for the anilox channels, a smooth pathway is established for liquid flow. This open anilox geometry reduces liquid turbulence and prevents ink from lifting due to centrifugal force during rotation. As a result, the ink flows calmly through the channels, avoiding contact with back walls that add to the ink lifting phenomenon (Figure 4). This free-flowing geometry enables the ink to move smoothly and consistently across the surface of the anilox, propelled by the G-force. The primary objective of the GTT 2.0 is to achieve a uniform layer of ink transfer, even at high speeds, thereby enabling expanded color gamut to meet the demands for quality and consistency.
When GTT was initially introduced to the market, it was ahead of its time and didn't see widespread adoption by printers. Back then, printers were worried about the possibility of plate dots entering the open channel engraving, although scientifically impossible. Moreover, there was no precedent for this type of engraving in flexo, so many understandably hesitated to embrace the unknown.
Today, GTT 2.0 has gained traction and is being successfully employed by printers worldwide for ECG printing and beyond. This second-generation engraving has been honed into a reliable anilox solution for various print tasks, from flood coats to intricate process work. With improvements including up to a 50% reduction in cell wall surface and a 25% decrease in engraving depth, GTT 2.0 facilitates smoother ink flow and easier cleaning. This leads to enhanced possibilities for finer plate screens, richer colors, fewer print defects, reduced ink consumption and waste, quicker dry times, and superior print quality and consistency across all speeds.
If past attempts at ECG printing fell short, we urge you to give it another shot to unlock your profitability. GTT 2.0 and Apex International are your dedicated anilox solutions partner committed to your printing success. Contact our team today to schedule a consultation with an Apex Print Specialist and embark on your journey with the world's largest and most innovative anilox manufacturer.