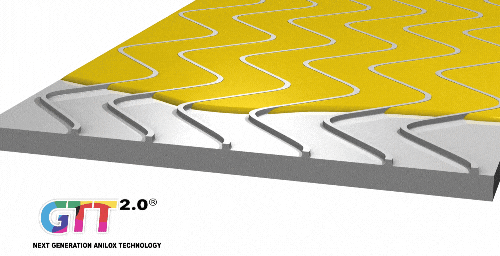
Flexographic printing has long been a staple in packaging production, offering high-speed, cost-effective solutions for a variety of substrates. However, with the ever-growing demand for higher quality prints on reduced paper qualities, more sustainable processes, and increased efficiency, the need for innovation is more pressing than ever. This is where Apex International’s GTT 2.0 technology steps in as a game-changer, delivering groundbreaking advancements in the way water based ink is transferred and corrugated printing is executed.
In this blog, we’ll dive into the key features of GTT 2.0 and explore how it outperforms traditional anilox roll technologies. We’ll introduce the project we undertook to test GTT 2.0 across multiple printing challenges, and we’ll highlight the results from several specific print samples, each showcasing GTT 2.0's exceptional performance.
Why GTT 2.0?
GTT 2.0 technology was developed to enhance the original award-winning GTT engraving, fine-tuning its performance through years of experience across all markets. If you tried GTT in the past, now is the perfect time to re-evaluate. Apex has continued to address some of the most persistent challenges in printing: achieving consistent ink laydown, reducing waste, improving print quality on various substrates, and enhancing sustainability efforts. Unlike traditional anilox engravings, which often struggle with issues like dot gain, inconsistent ink transfer, and ink spitting, GTT 2.0 uses a patented open-channel structure that ensures smooth, controlled ink flow. This results in cleaner, sharper prints with less waste.
The Project Overview
To demonstrate the power of GTT 2.0, we conducted a series of print trials across multiple regions, comparing the performance of GTT 2.0 to traditional hexagonal and elongated anilox engravings under the same technical conditions. These tests were carried out on various substrates, including coated and uncoated kraft liner, recycled paper, and super lightweight paper. Each trial measured the ability of GTT 2.0 to maintain high print quality while optimizing ink usage, reducing defects, and improving environmental sustainability.
The trials were designed to reflect real-world challenges in printing, such as:
- Achieving smooth gradients on light and recycled substrates.
- Printing strong opaque whites on uncoated test and kraft liner without crushed edges.
- Less mottling of ink, resulting in smoother solid prints.
- Reducing dot gain and maintaining sharpness in high-resolution images.
- Better dot-shape-control, resulting in more clean printed images.
- Lowering CO2 emissions and ink consumption to promote sustainability.
Each trial demonstrated the superior control and flexibility of GTT 2.0, resulting in better overall print quality, less ink usage, and more efficient production.
Key Findings
Improved Ink Laydown and Density
One of the standout benefits of GTT 2.0 is its ability to deliver higher ink density and better overall laydown. This was evident across all substrates, particularly in trials involving high-coverage areas like opaque whites on brown paper. Traditional anilox engravings often left inconsistent patches, but GTT 2.0 achieved a smoother and more uniform result.
Cleaner and Sharper Print Details
Achieving crisp, sharp details can be a challenge, especially with fine text or intricate designs. However, GTT 2.0 excelled at producing clean edges, reducing dot bridging, and maintaining high-resolution clarity even in demanding applications. This made it easier to achieve high-quality results without multiple print passes.
Reduction in Ink Consumption and Waste
Sustainability is a growing concern in the printing industry, and GTT 2.0 responded to that need by offering significant reductions in ink consumption. In several trials, ink usage dropped an average of 18% resulting in lower costs and less drying energy needed. This also contributed to a notable decrease in CO2 emissions, further supporting eco-friendly printing practices.
Superior Performance on Varied Substrates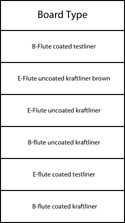
The trials highlighted GTT 2.0’s versatility across multiple substrate types. Whether printing on coated test liner, uncoated kraft liner, or recycled paper, GTT 2.0 consistently delivered superior results. The ability to switch between different materials without compromising on quality is a major advantage for printers working with diverse packaging needs.
Enhanced Sustainability
The environmental impact of printing is under increasing scrutiny, with regulations and consumer demand pushing companies to adopt more sustainable practices. GTT 2.0 not only reduced ink waste but also contributed to a reduction in CO2 emissions. In some cases, switching to GTT 2.0 resulted in a 15-25% decrease in emissions, making it a more environmentally friendly choice for printers looking to lower their carbon footprint.
Less Plate Cleaning
GTT 2.0 offers significant advantages in reducing plate cleaning, thanks to improved dot shape control and minimized dot bridging. With less ink buildup on the edges of flexo plates, printers experience fewer press stops, leading to higher productivity and enhanced overall equipment effectiveness (OEE). This improvement streamlines operations and allows for smoother, more efficient print runs.
Looking Forward
The results from our project highlight the potential of GTT 2.0 to revolutionize corrugated printing, setting a new standard for print quality, efficiency, and sustainability. By adopting GTT 2.0 technology, printers can not only enhance their output but also reduce operational costs and environmental impact.
In this Blog Series, we will explore the results from the several specific print trials, each focusing on a particular printing challenge. From skin tones to opaque whites, and from sustainability to efficiency, you’ll see firsthand how GTT 2.0 outperforms traditional technologies in real-world applications.
Stay tuned as we dive deeper into the future of printing with GTT 2.0.