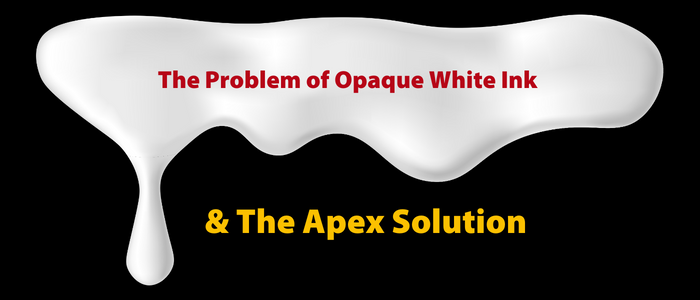
Opaque white ink is a double edge sword; both a solution and a problem for flexographic operators striving to produce consistent print quality. At its best, white opaque ink can bring vibrancy, clarity, and consistency to your print design; and at its worst, it can cause print defects, slow down the press and reduce profits. Whether we like it or not, opaque white ink is a fundamental element of the flexographic printing process that printers must control. With consistent compact opaque white ink laydowns, printers can increase the opacity and vibrancy of printed colors, add highlights, contrasts, and special effects to designs, increase brand color consistency and print readability, and overall, enhance the visual appeal of the printed material.
Below is an example of the vibrancy that can be achieved when the white ink laydown is smooth and compact with GTT.
At Apex International, we have innovated anilox roll solutions to optimize the performance of your opaque white inks, and minimize print defects, ink usage and costs. In this blog, we’ll discuss the reasons opaque white inks cause trouble in the pressroom, and the GTT 2.0 anilox solution designed to combat this ink dilemma.
What’s the Deal with Opaque White Ink?
Opaque white ink laydowns have haunted flexo operators for years. Often, the problems stem from the harder particles of pigment found in white ink and the way these particles behave on press. Due to the abrasive particles, operators must ensure the pigment gets proper dispersion to prevent clogging, uneven printing, and opacity issues. These robust pigments tend to settle more rapidly than other ink colors, leading to variations in opacity consistency. When operators encounter these opacity issues, they tend to increase the anilox cell size and volume to mask the defects and simply attempt to apply more ink to improve coverage. This, however, increases ink costs tremendously and reduces productivity and profits. White ink is most likely one of your cheapest inks by quantity, however it will be the ink you spend the most money on (typically accounting for about 30% of a printer’s ink budget). Why let one of your most costly consumables go to waste! Watch “The White Ink Dilemma” Apex video for more details.
Achieving the right viscosity for white ink is also imperative for successful print. Sometimes, the ink can experience a shear effect, isolating the pigments resulting in a reduced transfer and decreasing the ink viscosity due to the shear forces in the printing process. If the ink is too thin, the opacity will be compromised resulting in a less opaque and more transparent white layer. Alternatively, if the viscosity is too high, it can lead to a streaky appearance in the print and increase the dry time/reduce press speed. Ink spitting, mottling, pinholing, and uneven laydown are all print defects caused by the relationship of the ink, its viscosity, and how it interacts with the engraving pattern on your anilox roll.
Dry time is also a factor with opaque white inks. These inks are known to take longer to dry due to their higher pigment content from the use of higher volume anilox cells, and if your operator is increasing ink usage in response to a print defect then your drying process and reduced press speed is going to start hurting your profits. If your ink doesn’t dry properly before the next pass it can lead to smudging, offsetting and other print defects. To adjust, the operator either needs to increase the dryer settings and air flow speed, reduce the press speed, or reduce the amount of ink laydown.
Does any of this sound familiar? Are you struggling with opacity issues? Maybe you experience ink spitting, mottling, pinholing or another print defect in your opaque white inks? Or perhaps you have beaten these obstacles at the cost of your press productivity/profitability. Apex International has worked for over a decade to diligently innovate a solution to your problem of opaque white ink laydown: the GTT 2.0 open slalom channel anilox engraving.
The GTT Anilox Solution
With the anilox at the heart of the flexographic printing process, it should be no surprise that your anilox roll has the power to minimize, or even eliminate, the common problems associated with opaque white inks. As a global leader in anilox innovation and production, Apex International is proud to offer an anilox engraving that has been proven to reduce print defects, ink usage and dry times, while increasing the opacity, consistency, and profitability of white ink applications. In testing and development for over a decade, the GTT 2.0 open slalom channel engraving is the solution you’ve been looking for.
The open channel “S” pattern of the GTT 2.0 anilox is a proprietary Apex innovation that removes the liquid turbulence and ink aeration caused by obstructive anilox cell walls. The open geometry delivers two key benefits:
-
-
- GTT allows the harder and abrasive particles found within opaque white ink to flow freely throughout the anilox roll. This free flow of ink allows for a more consistent white ink laydown that optimizes ink usage for ultimate profitability.
- GTT eliminates the micro bubbles created by ALL cell engravings.
To understand this statement, you must first accept that an anilox cell is never empty. The cells will always contain either ink or air which is why when you increase the engraving cell size and volume you never get a linear increase on ink transfer. The basic science behind this is that the bigger the cell size the more air can enter the doctor blade chamber. As the air is trapped and dragged into the chamber (with traditional 6-walled anilox cells) air can build up within the chamber causing micro-foaming and ink spitting which will detrimentally impact your print results. The open cell geometry of GTT eliminates aeration within the anilox and allows for a more even ink flow throughout the full anilox roll or sleeve. It has been proven; with GTT you can save up to 14% in opaque white ink costs while still achieving the same desired level of opacity. Print white opaque inks faster, better, and stronger with the GTT engraving innovation from Apex International.
-
In a recent controlled case study, Austrian flexo printer, Coveris, tested four different anilox engravings (longcell, staggered long cell, GTT-L pattern and GTT-C12 pattern) and their impact on white ink opacity and consumption. In the study conducted on their W&H Novoflex CM10 flexo press, Coveris found the GTT-L engraving used the lowest anilox volume measurement (11 cm3/m2 | 7 bcm), while achieving the required opacity level while consuming the lowest ink usage (25.5kg). The walls of the longcell geometry contributed to higher amounts of ink aeration and ink consumption while the GTT engraving opacity and homogeneity were on target with no print defects recorded. Read the full Coveris Opaque White Ink Case Study to learn more.
Opacity is more than just a number. How compact the ink laydown is will deliver a clear advantage to printers by creating a smooth surface for the additional inks to be printed on and reduce the ink consumption that will increase your profit.
With GTT 2.0 anilox engravings, printers can combat the many problems of opaque white ink laydowns and reduce, if not eliminate, their most pressing white ink dilemmas consistently. The open channel geometry reduces aeration (pin holes) and liquid turbulence, allowing the ink pigments to flow freely to the plate. Printers can achieve their desired opacity while reducing ink consumption and dry times. Press speeds can increase without fear of drying or viscosity problems arising. In addition, the cleaning of the anilox is easier than ever with the 30% shallower anilox geometry of GTT. With the innovation found in GTT 2.0, printers now have a proven solution to their most pressing opaque white ink problems. Contact Apex International to discuss which GTT engraving size can help solve your white ink dilemma and discover your most profitable pressroom yet!