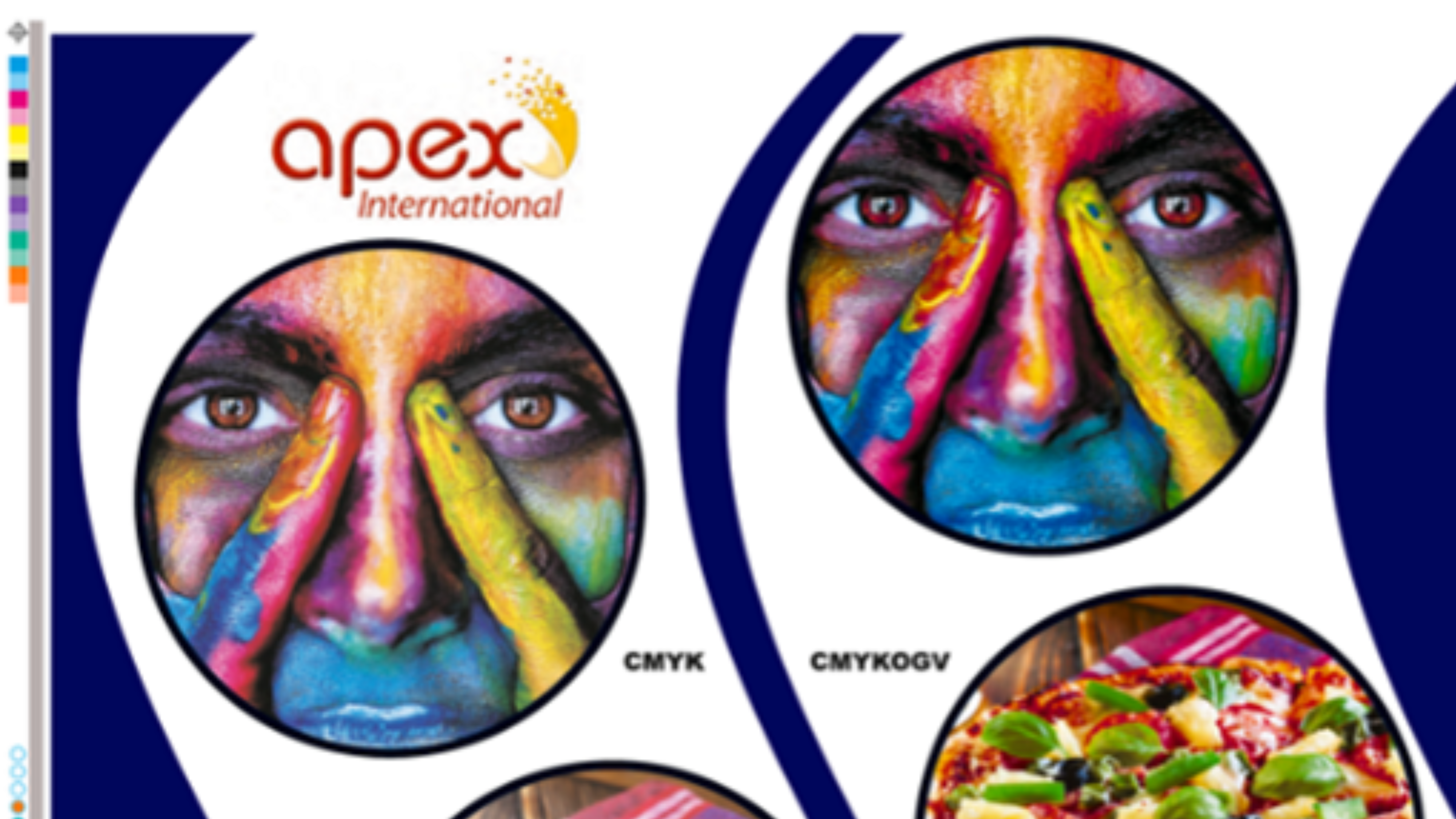
When it comes to achieving vibrant and color accurate prints, color density plays a critical role. Maintaining the proper levels of CMYK color laydown (+ OGV if expanded gamut) significantly influences the overall quality of printed materials.
At Apex International, we specialize in precision anilox solutions designed for accurate color management to achieve outstanding print results. In this blog, we’ll explore the importance of color density in printing, how it affects the final product's visual impact, and the essential role of the anilox in achieving desired color strength.
What is Color Density in Print?
Color density refers to the richness or intensity of ink applied to a substrate. Achieving the correct density ensures that printed colors are true to the original design and maintains consistency across different print runs. The level of color density is controlled by the management of each print station, consisting of the ink, ink pan or chamber, doctor blade, and anilox roll. By implementing effective quality control processes for these components, you can properly manage color laydown and density.
The Importance of Managing Color Density
The density of color applied will affect the accuracy and quality of the image across print runs, while also affecting your ink consumption on press. Let’s take a closer look…
Color Accuracy. Color density directly impacts accuracy in printed materials. If the density is too low, the printed image will display a lack of vibrancy and depth, appearing washed out. In color build applications, if the density is not correct on one or more of the print stations, the colors will appear different. Conversely, excessive density can result in oversaturation, causing colors to bleed and details to be lost. Controlling the right balance is crucial for achieving accurate colors that reflect the designer's vision.
Image Quality. The density of ink affects overall print quality and the ability to reproduce fine details. Proper color density ensures that gradients are smooth and details are crisp, making the final product visually appealing. An anilox that transfers too much or too little ink will directly affect the final image quality.
Consistency Across Runs. Consistency is key in the printing industry, especially for businesses that require uniformity across multiple print jobs. Monitoring and controlling color density helps ensure that colors remain consistent for each order. Precise color matching is critical for maintaining brand identity and meeting customer expectations. To maintain business from large consumer brands, production run consistency and repeatability is a must or else you will risk losing some of your biggest clients.
Ink Coverage and Consumption. Adequate color density ensures even coverage, which is essential for preventing issues like mottling or uneven color distribution. This is especially important for high solid areas. Printers that understand color density choose the right anilox solutions to optimize ink usage, reducing waste and costs while still achieving high-quality results.
Tips for Achieving Correct Color Strength
To ensure optimal color density and strength, consider the following tips from the experts at Apex International:
Perform Regular Maintenance: It’s important to regularly perform routine maintenance and cleaning practices for your anilox inventory. Taking the time to calibrate your press and auxiliary equipment will help maintain consistent color output. Contact your Apex representative for training and assistance with flexographic best practices.
Use the Right Inks: There are various ink formulations to achieve the color density desired. Work with your ink supplier to select the best ink formulation for your specific substrate and application. They can also help with understanding and controlling the optimal viscosity for each job.
Choose the Best Anilox Roll: Selecting anilox rolls with the correct engraving technology and volume is essential for managing proper ink transfer. Apex’s GTT 2.0 is a patented open-slalom channel engraving designed for achieving consistent and repeatable color laydown for a variety of print applications. Our UltraCell Hex 60 anilox rolls are also designed for excellence in color strength, with a defined, repeatable cell shape for enhanced ink transfer. With the right anilox partner, you can overcome color density issues efficiently and effectively.
Automated Inspection: There are automated tools and software that actively measure and monitor ink density and print quality during press runs. With on-press systems, you can catch color issues in its tracks, stopping production for adjustments before the full run is wasted.
Consider Fingerprinting Your Press: Not Just During FAT but Annually: Fingerprinting, also known as press characterization, is a calibration process that helps define the capabilities of a flexo printing press when using specific ink, density, pressure, speed, and operators. The results are then used to create a dot gain compensation curve.
Training and Education: Ensure your team is trained in color management practices and understands the importance of color density in the printing process. Apex is a proud member of the Flexographic Technical Association and recommends the FIRST approach to standardizing your flexo process. Learn more here.
The Role of the Anilox in Color Strength
While numerous variables play a role in ink transfer, the anilox roll is the key to controlling the amount of ink delivered to the substrate. When selecting the right anilox roll for each print run, several factors should be considered such as machine characteristics, plate and substrate types, ink formulation, and press speeds.
Key anilox features that affect color density are cell volume, cell count, geometry, surface treatment, and ink compatibility. Higher cell volumes or lower cell counts deliver more ink, which is ideal for large solid areas. Lower cell volumes and/or higher cell count provide more precise ink delivery for high-definition images and fine details and text. Cell geometry and surface treatment will also affect the rate and amount of ink transfer resulting in higher or lower color density. Inks like UV/LED, water-based, and solvent interact differently with cell structures, influencing density, drying times, and adhesion.
While our recent case study confirmed it’s not as simple as matching a BCM value to a specific print density, we did uncover some useful insights to help you make informed decisions about your anilox rolls. Read the summary or watch the recap video here and talk to your Apex Representative to determine the best anilox specifications for the job.
GTT 2.0 and UltraCell Hex 60 Anilox Engravings Can Help
Apex International has innovated advanced anilox solutions, like the GTT 2.0 open channel and UltraCell Hex 60 engravings, for accurate color management. These rolls are specifically engineered to optimize ink transfer and help achieve the desired color strength consistently and economically. GTT 2.0 stands out by improving dot printing stability and reducing ink aeration. With 21 specifications ranging from 1.3 BCM to 26 BCM, these engravings are created by maintaining the optimum channel shape ensuring that they are low maintenance when you consider the cleaning regimes. With their innovative design, Apex anilox rolls ensure that printers can maintain the required color density without sacrificing efficiency or quality.
Conclusion
Color density is a critical aspect of printing that significantly affects color accuracy, consistency, quality, and overall print success. Understanding and managing color density—especially with Apex's advanced anilox rolls—can help printers deliver consistent, high-quality results that meet client expectations. For more insights on color management and printing techniques, watch the video on cyan color strength and browse our print and anilox resources in the Apex Academy. Let us help you achieve unparalleled print quality. Contact our team today to explore how Apex solutions can elevate your printing process.