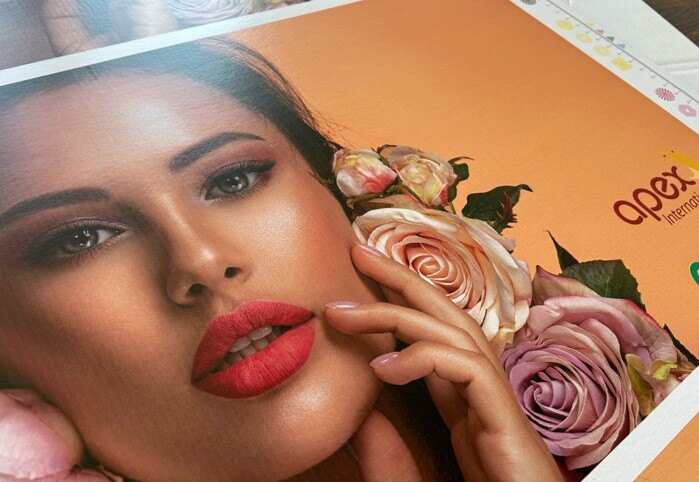
In the world of corrugated printing, achieving clean and natural skin tones to match offset quality is one of the most difficult challenges. This is due to several factors, including inconsistent ink laydown, dot gain, and the overall complexity of balancing colors to achieve perfect grey tones.
With Apex International’s GTT 2.0 technology, however, these challenges can be met head-on. GTT 2.0’s revolutionary design offers a level of precision and control that makes it ideal for producing the kind of high-quality skin tones that are critical for both packaging and high-end print products. In this blog, we’ll explore how GTT 2.0 successfully overcomes these challenges and delivers superior results.
The Complexity of Printing Skin Tones in Corrugated Packaging
Skin tones are notoriously tricky in printing, particularly when dealing with corrugated substrates. The reason lies in the delicate balance of colors required to reproduce skin naturally. Minor deviations in grey balance can cause unnatural hues that are immediately noticeable to the human eye. Moreover, corrugated substrates like recycled paper add to the complexity due to their uneven surfaces, making it harder for traditional anilox technologies to achieve consistent results.
This issue is compounded by the inherent limitations of traditional hexagonal and elongated anilox engravings, which often struggle to balance anilox volume (to achieve the required color density) and the LPI cell openings (to avoid dirty print and ink control). Poor ink distribution and inconsistencies due to deeper cell shapes lead to blemishes, graininess, and variations in tone, making the final product look far from the intended result.
GTT 2.0’s Solution
Apex’s GTT 2.0 technology was specifically designed to address these kinds of challenges. Its patented open-channel structure allows for more consistent ink flow and superior ink transfer, which leads to smoother, cleaner prints.
In one of our recent projects, we demonstrated GTT 2.0’s ability to produce clean, balanced skin tones. The project focused on printing a human face, a perfect test for this technology given the complexity. The substrate used was recycled paper, a notoriously difficult surface to print on with traditional methods due to its rough texture and absorbency.
The results were impressive. GTT 2.0 provided excellent grey balance and maintained the smooth transitions between colors, eliminating the blotchiness and uneven ink laydown. Skin tones appeared natural and smooth, with no visible defects.
The Role of GTT 2.0’s Ink Flow Management
The key to GTT 2.0’s success in printing smooth grey balances lies in its controlled ink flow. The open-channel design based on the true optimum opening to depth ratios and the elimination the back wall barrier ensures that ink is distributed evenly across the substrate, reducing the risk of oversaturation in certain areas and ink starvation in others. This balanced distribution is critical for maintaining the fine details and subtle color variations that are essential in reproducing skin tones accurately.
In addition to the improved ink flow, GTT 2.0 also offers superior control over dot gain, featuring new discovered benefits like DSC (dot-shape-control). Traditional anilox engravings often experience dot gain, where ink spreads beyond the intended print area, resulting in a blurred or less precise image. GTT 2.0 minimizes dot gain, allowing for sharper images and cleaner lines, which is particularly important in detailed areas like facial features. DSC avoids ink build up on the edges of screened areas that lead to higher plate cleaning times.
Enhancing Print Quality on Recycled Substrates
Downgrading substrates is having a high impact on sustainability and costs of packaging. An ongoing challenge in corrugated printing is achieving high-quality results on recycled substrates, which can have uneven surfaces that complicate ink transfer and can lead to uncontrolled dot shapes. GTT 2.0’s open-channel structure enables it to adapt to these rougher surfaces without sacrificing print quality. The ink flows smoothly into the substrate’s grooves and crevices, ensuring an even, high-quality finish.
During the trial, the recycled paper showed none of the typical issues associated with printing on such materials. There were no unsightly blotches, no uneven patches, and no degradation of the skin tones. Instead, the face printed with GTT 2.0 technology looked as smooth and natural as it would on more costly and higher weight paper qualities, demonstrating the technology’s remarkable adaptability.
The Benefits for Corrugated Printers
For corrugated printers, the implications of these findings are significant. Being able to produce high-quality skin tones on corrugated substrates opens new possibilities for packaging and printed media. Brands that rely on accurate and high-quality imagery, such as cosmetics, luxury goods, or even e-commerce companies that want to enhance their packaging designs, can greatly benefit from GTT 2.0.
By using GTT 2.0, corrugated printers can:
- Reduce waste due to fewer misprints and less plate cleaning.
- Improve print quality across a wide range of substrates.
- Save time and costs by achieving high-quality results in fewer passes and less ink usage.
- Meet the demands of high-end brands that require precise, detailed imagery.
- Higher flexibility in choosing flexography instead of offset or digital print, due to quality enhancement.
Conclusion
The ability to reproduce accurate skin tones on corrugated substrates is a game-changer for the industry. GTT 2.0 technology from Apex International not only meets this challenge but exceeds expectations by delivering smooth, natural tones that rival offset and digital printing.
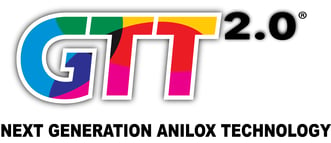
With its superior ink flow control, reduced dot gain with better dot-shape-control, and adaptability to difficult substrates like recycled paper, GTT 2.0 is setting new standards for corrugated printing. Whether you’re working with high-end packaging designs or mass-market corrugated materials, GTT 2.0 ensures that you can achieve the print quality you need without the complications of traditional anilox technologies.
Stay tuned as we explore more groundbreaking results from GTT 2.0 in our ongoing blog series, “Mastering Corrugated Printing with GTT 2.0: A Revolution in Precision.”