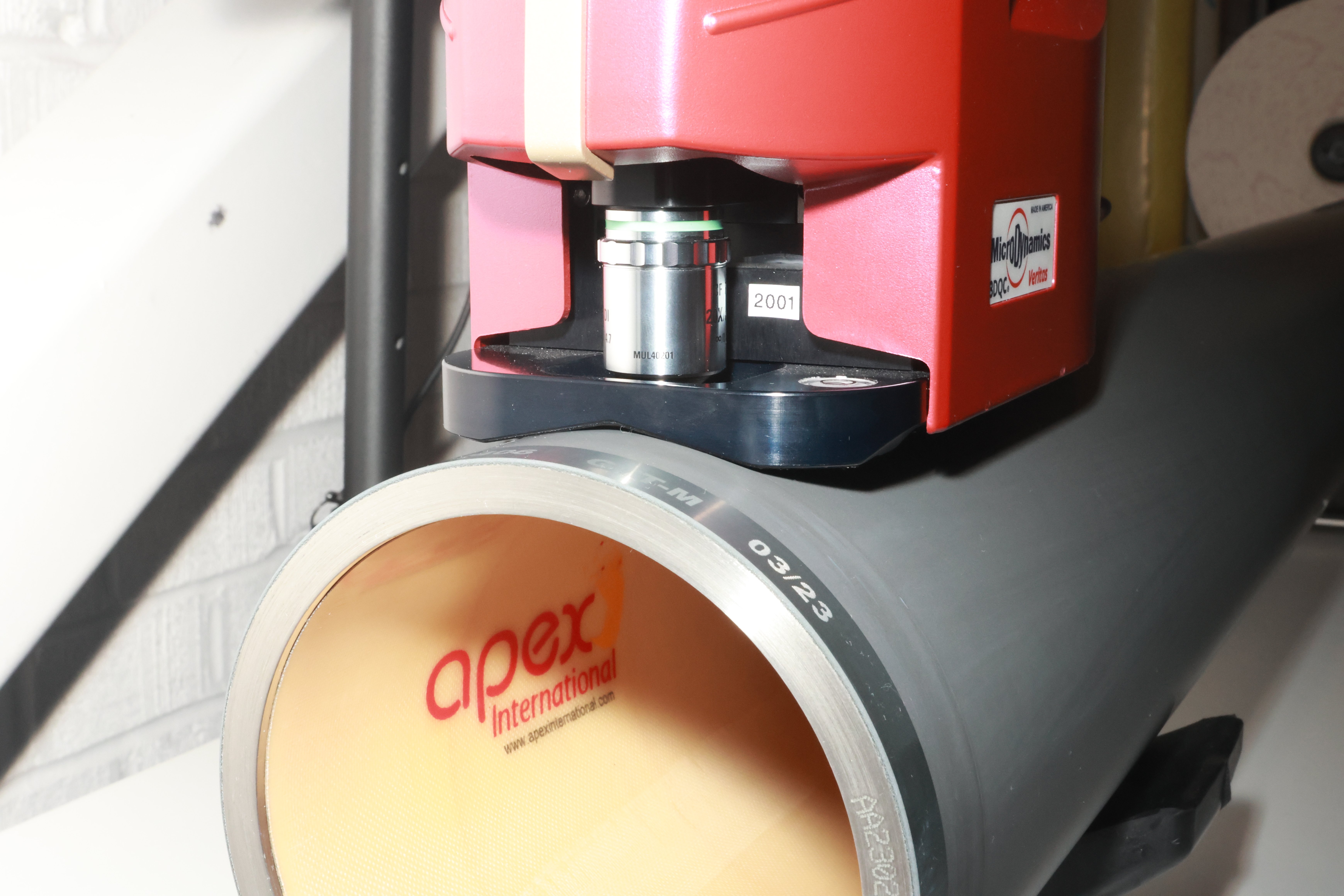
With the rise of digital printing technology, many long-standing flexo printers have begun to question – should I go digital, or should I stay with conventional flexo? The answer is not quite simple. There are advantages and disadvantages affecting both print applications and many questions to consider.
At Apex International, we manufacture the heart of the flexographic press – the anilox roll. Though digital printing has gathered momentum for some applications in recent years, Apex is confident that conventional flexo printers that strive for process standardization and optimize for press performance efficiency will have a competitive advantage over digital format in the long run. Here’s how…
Digital Printing
Digital printing is a newer method of printing that removes the heart of the flexo press and replaces it with digital inkjet technology. Inkjet technology controls the level of ink placed on the substrate according to the digital blueprint. Replacing the need for the anilox, ink and printing plate, digital inkjet performs color builds using specially formulated CMYK inks (and OGV for expanded gamut).
Some of the advantages of digital printing are:
-
-
Without the need for anilox, inks or plates, there is minimal downtime for changeovers and cleaning.
-
With a faster start up to print production, digital has less ink and substrate waste.
-
Digital printing is capable of variable data and versioning.
-
All these advantages contribute to increased press uptime and profitability for digital printers.
-
Alternatively, some of the disadvantages of this print method are:
-
-
The flexo process is often still required for coating and laminating the print for digital ink laydown.
-
Digital printers tend to have a single source for consumables, which can get expensive.
-
Digital printers are much more expensive than a flexo press, creating a large barrier to entry.
-
Digital printing cannot compete with flexo on color vibrancy and saturation and tends to appear more faded than flexo or offset printed products.
-
With a single source for consumables and industry standardization, there is little room for a competitive advantage in digital printing.
-
Popular for its short run and variable data printing capabilities, digital has often been used as a supplemental printing method for researching and testing various versions of future packaging runs. With digital printing sales growing in the market, many flexographic printers have considered this alternative print method.
Flexographic Printing
Flexography has been a tried-and-true method for printing since inception. At the heart of the flexo print process, the anilox roll, ink and printing plate come together to form the final printed image. For every print job, these three components will need to be cleaned and/or changed for the next print run, unless you are deploying ECG printing methods. Flexo is known for being more economical than offset printing while maintaining the vibrancy and quality of print.
Some of the advantages of flexography are:
-
- This printing method can achieve much higher speeds than digital, while maintaining quality, making it economical for longer print runs.
- Flexo is known for its high ink coverage, resulting in bold, vibrant colors and excellent color saturation.
- Flexo printers have a wider range of substrates and in-line embellishment capabilities they can utilize allowing for higher quality and more specialized prints.
- There is a wide variety of suppliers in the flexo space, allowing for more competitive advantages between printers.
- This printing method can achieve much higher speeds than digital, while maintaining quality, making it economical for longer print runs.
Printers utilizing CMYK or CMYK+OGV color-build methods do not need to change their anilox and inks for every print run. This creates the advantage of increased efficiency and profitability that can be comparable to digital.
On the other hand, some disadvantages of flexography are:
While digital printing offers advantages in terms of customization, short runs, and variable data printing, flexographic printing remains the preferred choice for mid to high-volume printed packaging, especially when cost-effectiveness, speed, and substrate versatility are paramount. By evolving and adopting new techniques and leveraging the strengths of flexographic printing, manufacturers can efficiently produce high-quality packaging materials that meet the demands of diverse markets.
- Press downtime is needed for cleaning and changing anilox rolls, inks and printing plates after every run (except for the color build print method).
- Flexo is traditionally uneconomical for short runs due to increased changeover downtime and first time set of printing plates.
- Due to defects, downtime and press set up, flexo may produce more waste than digital.
Gaining a Competitive Edge Over Digital
Prior to digital print technology, flexography did not have much competition. With the rise of this new print method, some flexo printers feel they cannot compete with digital. Apex is here to tell you – you can!
Before digital, many brands would not accept the color build methods employed by flexo printers. Considering digital only does color builds, flexo printers can now compete with the efficiency of digital by employing CMYK print applications. This reduces changeover times and keeps the press running at maximum productivity. These color-build methods also allow quicker changeovers, which means flexo printers can compete with short run jobs. To compete with digital printing, anilox quality control is needed to master the art of color builds and reduce ink and substrate waste. Apex’s proprietary open slalom channel anilox engraving, GTT 2.0, is an ECG enabler that has empowered printers to achieve profitable ECG and CMYK printing. Learn more in this blog, here.
To remain competitive over digital, flexo printers need to work with their suppliers to create a standard method for print runs that is repeatable, but also allows deviations to remain competitive. Digital printers have this advantage, though flexo printers can standardize too!
Before diving into digital printing, work with your Apex anilox representative, ink supplier and plate manufacturer to determine the best product mix for enabling color-build printing and profitable SOPs. If you can achieve CMYK color-builds, you can compete with digital, and win. Evenmore, if you can build on CMYK and extend your color gamut into OGV inks, you will be in the top 15% of flexo printers flourishing in efficiency, profitability, and quality.
If you’re struggling with digital rivals, talk to your Apex representative and we’ll help you gain an edge in the competition with innovative anilox solutions and quality control methods built for you.