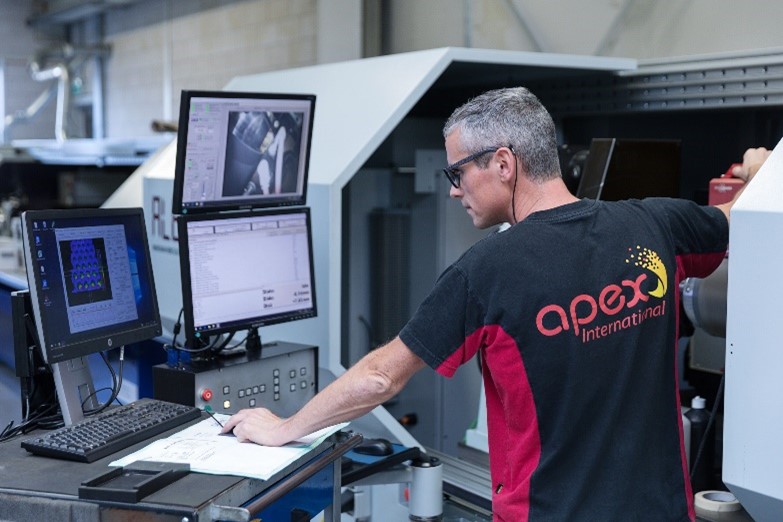
Though anilox engravings are a microscopic component of your print process, these components can have a huge impact on your print quality, positively or negatively. Uniformity, precision, and durability are key to manufacturing the millions of anilox cells or channels that make up the heart of the flexographic printing process. As a world-class manufacturer of anilox rolls and sleeves, Apex International has years of experience refining and innovating liquid transfer technology. In this next blog in our “Anilox 101” series, explore the characteristics of anilox cells/channels, the different types of anilox engravings and their applications, along with best practice, from your global anilox partner, Apex International.
We must emphasize that, in many cases, the wrong choice of anilox specification can lead to higher costs in cleaning the anilox. Some printers may even spend more time and money cleaning the anilox than the asset is even worth! Additionally, the wrong engraving and surface touch points can result in faster doctor blade wear, leading to higher costs in consumable and increased downtime for blade changes.
What are Anilox Engravings?
Small but mighty, anilox engravings are the microscopic indentations manufactured with precision and uniformity along the surface of an anilox roll or sleeve. Anilox engravings are a critical component in the flexographic and offset printing process, responsible for transferring a precise amount of ink or coating to the printing plate, which, in turn, transfers the ink or coating to the substrate (e.g., paper, cardboard, film).
These engravings come in a variety of shapes and sizes, and their pattern will determine the amount of ink or coating volume that will be transferred for print. Anilox cells or channels are engraved through either mechanical or laser engraving technology, depending on the desired shape and application. The geometry, depth and shape of the engraving must be closely controlled during the manufacturing process in order to be uniform, consistent, and durable. Using the latest multi-hit laser technology, Apex International manufactures anilox solutions to the tightest OEM tolerances and highest industry standards.
Anilox engravings are measured by Billion Cubic Microns (BCM) or Centimeters cubed by meters squared (Cm3/m2), which determine how much volume of liquid will be held within a specific area, and by Lines per Inch (LPI) or Lines per Centimeter (Lpcm), the amount of indentations engraved across the length of the roll. The shape, volume, and line screen will vary depending on the application it will be used for. Different printing applications, designs and substrates will require specific volumes and line screens to achieve optimal print quality, color density and coverage. From HD graphics to fine texts, solid areas to special effects, the proper selection and maintenance of the anilox roll is essential for achieving consistent, high quality print results. Contact your Apex representative for their expert anilox recommendation tailored to your print goals.
Anilox Engraving Types
Apex International manufactures a wide range of standard, specialty and custom anilox engravings for a variety of printing and coating applications. We manufacture hexagonal, GTT 2.0, trihelical, channel, quad, longcell, and more. With multi-hit laser technology and next generation materials, our anilox engravings are manufactured with the tightest tolerances for ultimate performance. Here’s your guide to understanding Apex anilox engravings and their characteristics, applications, and advantages/ disadvantages.
Hexagonal. The hexagon cell engraving has six uniform sides placed at 60° or 30° angle and resembles a honeycomb pattern. It is one of the most common cell engravings, available through every flexographic anilox manufacturer. This engraving type is best used in solvent-based flexible packaging applications, performing well with thinner, less viscous inks (up to 24 second on Din 4/ 30 seconds Zhan 2). The shape maximizes the cells per square inch with lpi ranges of 120 to 1500, providing good dot support and does not clash with the plate angle of CMYK applications. This anilox engraving is suitable for a wide range of applications and performs well with process work in narrow web and wide web printing.
Although an industry standard for many years, the Hex 60° engraving does have a few weaknesses. Hexagonal anilox engravings have a restricted print range and may have inconsistent transfer when you switch from roll to roll (with the same LPI and volume), due to the engraving shape, wall thickness due to polishing or depth of the cell achieved. These three factors mean many printers must host a large inventory of anilox rolls for their different print applications. The cell geometry is also known to have weak walls when extreme specs are requested, and can contribute to ink spitting, foaming, misting or the ghosting effect due to a variety of factors. Hex anilox engravings may also require more cleaning than other anilox cell types. The Ultracell Hex 60° is an Apex anilox innovation that takes the traditional hexagonal structure to the next level! With a smoother inner cell that maximizes liquid transfer, UltraCell battles these common Hex 60° defects with greater ink release and faster clean ups.
GTT 2.0 Open Slalom Channel. Perfected through years of continuous improvement, the GTT 2.0 anilox engraving is patented and manufactured by Apex International to be the “Swiss army knife” of anilox rolls. This engraving has a smooth, consistent open slalom channel geometry and resembles the waves of an “S.” Available in 21 volume variations, GTT 2.0 was innovated with a 50% reduction in cell wall surface area and a 25% reduction in average channel depth in order to minimize liquid turbulence. This innovation allows for smoother ink transfer, better solids, easier cleaning, maximum ink mileage and a significant reduction in print defects and troubleshooting. Additionally, this reduction in liquid turbulence eliminates ink spitting and ink foaming, making it one of the most repeatable anilox technologies on the market today. This anilox roll provides high quality performance universally across all markets, however this technology is an ideal solution for ECG printing, Solvent inks, UV inks, water-based inks and value lacquers. Additionally, GTT 2.0 can “future proof” your press for the inevitable plate, ink, and screen developments to come.
Though it has many advantages, GTT 2.0 is a revolutionary, new anilox engraving innovation rapidly finding its place as the premier anilox technology in the industry. Therefore, making the switch from the historic Hex 60° to the innovative GTT engraving is a real consideration for printers today. To begin, GTT 2.0 does have a higher cost than the other engraving options and is a patented technology only available through Apex International. However, rest assured, Apex is a global anilox manufacturer with worldwide service and manufacturing facilities for incredibly fast lead times. Making the switch to GTT 2.0 requires a clear understanding of your needs and the areas you wish to improve upon. With any new technology there is always a small learning curve, but beyond this there is much value in consolidating and standardizing your anilox inventory with GTT 2.0. Apex Anilox Specialists can help guide you through the switch to ensure a seamless transition.
Quad. The quad engraving is a four-wall engraving at a 90° uniform angle and resembles a diamond or square. This engraving is often called a 45° engraving, typically engraved lower than 150 lpcm/60 LPI into chrome plated rolls used for basic corrugated or coating applications. As one of the original anilox engravings, this robust geometry has larger cell walls for structural support and is available through all anilox suppliers for tough printing and coating environments.
Like the Hex 60°, 45° cell engravings have a restricted print range and may have inconsistent transfer when you switch from roll to roll (with the same LPI and volume) due to the same factors. The angle is known to clash with CMYK standard plate angles and can contribute to ink spitting, ghosting, and foaming in the print and ink chamber. This engraving geometry will have 15% less cells compared to Hex 60° or 30° and is not suited for detailed process work.
Longcell. The longcell anilox engraving is an elongated version of the traditional hexagonal engraving with 6-walls of which two are longer than the others. This engraving type is best suited for basic, solvent-based print applications with large solid lettering and print areas like those found in corrugated. The engraving was introduced to the industry in the early 2000s, as an attempt to improve the Hex 60° transfer rate, though was unsuccessful in achieving the crisp details found in process work. The engraving geometry did, however, increase the cell volume available and ink transfer for solid block areas which made it ideal for basic water-based print applications. This technology lay dormant since 2001 until the increased popularity of the GTT open-channel engraving technology from Apex International. This sparked the revisit to innovating longcell engravings as an attempt to complete with the success of the GTT 2.0 patented anilox engraving.
As with the other walled geometries, longcell engravings also have inconsistent transfer from the “same” LPI and volume and are limited in print applications. The two elongated walls may become weak when extreme specifications are required. The angle of the cell walls clashes with plate screen angles and can create ghosting, ink foaming, ink spitting, misting, requiring regular cleaning and maintenance. Finally, there is no clear industry fixed angle – meaning 1 degree of difference can increase cell length by over 15+ microns. Due to its limitations, the longcell engraving should be used in course, corrugated block-style print applications and coatings for best results.
Channel. Known at Apex International as our “Channellox” engraving, channeled anilox engravings provide a break in the cell walls running top to bottom, allowing liquid to flow more freely throughout the roll. One step closer to the GTT 2.0 engraving, the channellox engraving is best suited for UV and thick, viscous inks and coatings for narrow web and wide web printing. With the reduction in cell wall surface area, ink and coating can move more freely from cell to cell, reducing ink spitting and foaming.
Though removing some of the cell wall increases ink transfer, the lack of the top and bottom retaining walls can cause some print defects. With the constant rise and fall of cell walls, in comparison to the consistent wave-like channels of GTT, print dots are less supported with channellox engravings. This can lead to dirty print around areas of fine text and edges. Additionally, the transfer performance may be inconsistent due to the loss of ink density as press speeds increase and its sensitivity to the pressure settings for color strength. Channellox is best used for thick, viscous inks and coatings in label applications.
Trihelical. The trihelical engraving geometry is a straight channel across the anilox rolls and simply resembles a line. This engraving was engineered for transferring thick, vicious inks and coatings for applications with high volume requirements. This course engraving is made of deep, uniform channels that create incredible volume possibilities with a strong wall surface for course coatings and large particle ink, varnishes, adhesives and more. For flood coats and protective varnishes and lacquers, the trihelical anilox engraving delivers the maximum transfer volume onto the print plate or direct to substrate. With great durability against the doctor blade, this engraving is traditionally provided at a maximum of 80 lpcm/30 LPI and works best in tough printing conditions.
With such a large volume of liquid transferred, the trihelical engraving is not suited for any image or design printing in flexo, label or corrugated. The geometry tends to lose the coating volume as press speeds increase and may be sensitive to the pressure settings defining the coat weight. Transfer performance consistency can also vary, and coating aeration is a common defect to troubleshoot with this engraving type. If thick coating quality is your goal, choose the trihelical anilox engraving from Apex International.
Positive. The positive engraving is different than all forementioned engraving, in the sense that the engraving is raised, and volume is created in the valleys between the raised cells. The engraving will resemble either a hexagonal 60° or a quad 45° engraving, inside out with the shape raised above. This engraving can pick up extremely viscous liquids and was created for glue, starch, and silicone metering for direct coating applications. The 45° positive also works well in silicone and cold seal applications with doctor blade chamber systems. The advantages of this engraving type are it allows a very open engraving structure delivering a high volume across the surface of the roll and reducing the risk of clogging and foaming and requiring less cleaning.
Positive engravings do have some negative attributes. The geometry can result in the coating weight/liquid transfer reducing at high press speeds and is sensitive to high pressure settings on press. With its high-volume transfer, positive anilox rolls do not perform well in image and process work and roll to roll repeatability and volume consistency has a higher tolerance. The positive cells provide minimum surface contact points that result in weaker structure and can wear fast if used with a doctor blade chamber or with aggressive coatings and lacquers. Additionally, the engraving is meant for thick, course coatings, and the liquid could leak if they are low in viscosity.
Anilox engravings play a vital role in the quality and performance of print and coating applications. Be sure to discuss your unique applications with your Apex representative for expert recommendations on the proper anilox cell geometry, volume, and depth to meet your goals.
Anilox Engraving Maintenance & Best Practice
Aniloxes are semi-consumables that will require cleaning, maintenance, repair, and re-engraving over the life of the roll or sleeve. With everyday use, inks and coatings can get trapped inside the microscopic engravings of the anilox resulting in poor print results, waste and downtime for cleaning and troubleshooting. Proper cleaning and maintenance of your anilox roll will prevent buildup, preserve integrity, and help maintain consistent ink transfer to improve your print quality and press performance. Keep in mind, the cost and time associated with cleaning will depend on the engraving type. Some engravings are prone to clog easier and can be higher maintenance requiring regular costly cleaning, while others are more durable or streamlined requiring less maintenance, cleaning, and downtime. Engravings that are manufactured with extreme volumes or with reduced touch points on the surface can be more susceptible to scoreline and shorter roll life as well.
For best performance, incorporate a regular cleaning schedule allotting time for manual cleaning, mechanical or laser cleaning and the re-engraving processes. Utilizing a cleaning brush or pad, the anilox should be cleaned when taken off press to prevent ink buildup. Choose a cleaning solution that effectively washes off the ink and coating used, without being too harsh or abrasive on the anilox roll or cells. Over time, your anilox may require a deeper clean using mechanical, laser or other cleaning technology. Using anilox inspection technologies, you can optimize your best performing anilox rolls for press, while sending poor performing rolls to be cleaned in-house or through outsourced cleaning services. Download our Anilox Use & Care Guide for a comprehensive look at proper anilox cleaning and handling.
It is important to handle your anilox rolls carefully to protect the engraving and avoid damage such as cracks, score lines and warping. Store anilox rolls in a clean and controlled environment, avoiding exposure to dust, dirt, and extreme temperatures. Monitor the wear and condition of anilox rolls regularly and replace rolls that are worn out or damaged beyond repair. For some anilox rolls, re-engraving services may be available to restore their performance.
Apex International has decades of experience in manufacturing anilox engravings to the tightest OEM tolerances and highest industry standards. Our anilox specialists are available throughout the globe to assist you in choosing the right anilox engraving for your unique print or coating application. With our patented GTT 2.0 and innovative UltraCell Hex 60°, we are committed to continuous improvement in anilox technology to ensure the highest performance and quality in your print and packaging endeavors. Contact our team to discuss which engraving is best for your process and get matched with the best performing anilox solutions on the market, with Apex International.