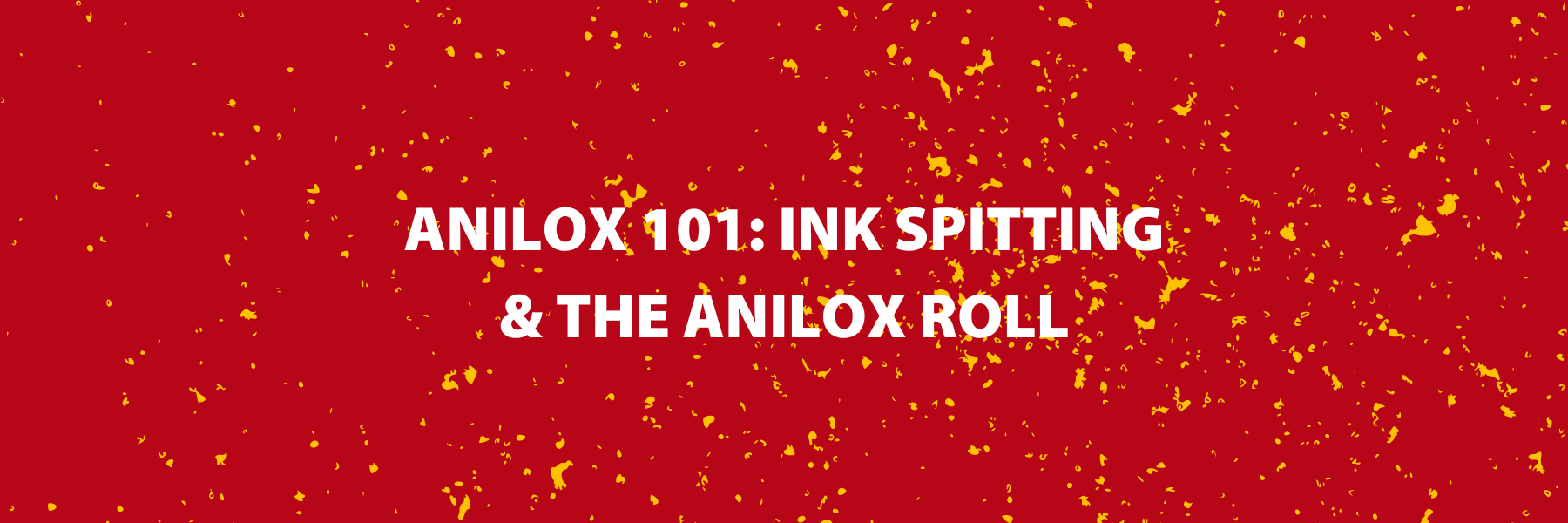
UV ink spitting is a flexo print defect that occurs when the ink builds up on the back of the doctor blade and randomly creates darker spots of ink within the print area, the phenomenon is predominantly seen when printing with UV ink however can be seen in water based and Solvent inks from time to time. This problem occurs when a higher viscosity of liquid ink is being used and the result is a splattered appearance in isolated sections or throughout the final print piece.
Through the extensive research and development of Apex anilox solutions, we’ve discovered the relationship between the anilox roll and the appearance or resolution of UV ink spitting. Your choice of anilox engraving, ink, and doctor blade can make all the difference in the success or failure of your flexo printing.
In this blog, we discuss the relationship between the anilox roll, the engraving factor, and the occurrence of ink spitting. We’ll also provide solutions to resolve this frustrating defect.
What Causes Ink Spitting?
UV Ink spitting in flexo printing can be caused by several factors, including press speed, anilox engraving, ink properties, blade or plate pressure, inadequate curing, and other press factors.
Excessive Pressure: If the pressure is too high between the anilox roll and doctor blade the surface contact point will be increased. This effect can allow the ink to build up on the back of the blade. When using cell-based engravings there will always be pressure build up in the cells, this pressure increases with press speed and as a result this can force the ink to lift from the cells after passing under the doctor blade. The basic science is that you can compress air, but you cannot compress a liquid. With an enclosed HEX 60 engraving, pressure and the centrifugal force during rotation of the anilox creates a lift out of the cell as the ink climbs up the cell walls, setting the stage for ink build up on the back of the doctor blade which can result in the spotted appearance of “ink spitting.”
Ink Viscosity and Tack: UV inks are thick viscous inks that can stick to the anilox cells and fail to properly release, leading to uneven transfer, increased ink consumption, and spitting. Comprehensive anilox cleaning schedules and choosing the right engraving for your job specifications is crucial for accurate ink metering.
Anilox Engraving options: The construction, engraving choice, and condition of your anilox roll is fundamental to achieving quality print. Printers now have a variety of innovations to choose from such as closed cell versus open channel anilox engravings, or plate materials and tape combinations. Your choice of suppliers and your cleaning/maintenance habits are crucial for the success of your print. Read our Anilox Cleaning blog series, featuring insight from top cleaner OEMs and suppliers.
Curing Process: Uneven ink release can lead to inadequate curing of the UV ink, which can also lead to ink spitting. If the curing process is not optimized—either due to insufficient UV light exposure, incorrect wavelength or intensity, or uneven exposure—then the ink may remain too fluid and can be prone to spitting. Enhancing the uniformity and effectiveness of the curing process can mitigate this issue.
Speed of the Press: As press speeds pick up, the centrifugal force caused by the rotation of the anilox roll increases, resulting in the ink lifting higher from the cells (if using the wrong anilox engraving). For enclosed anilox cells, as the ink sloshes to the back of the cell it lifts as it hits the back wall. Ink build-up on the back of the doctor blade will occur. One resolution is to slow down the press, but why cripple your greatest asset? As long as your UV curing system is optimized for fast speeds, your anilox roll should not slow your operations down for the sake of quality.
UV Ink Spitting Resolutions
Addressing UV ink spitting typically involves adjusting the press settings, proper anilox/doctor blade/ink combination and cleaning and maintenance.
Adjusting Pressure Settings. Carefully calibrate the pressure between the anilox roll and the printing plate. The goal is to apply just enough pressure, known as a “kiss impression,” to transfer ink adequately, without excess that could lead to spitting. This might require frequent adjustments depending on the job and conditions. Many press OEMs are now automating these settings to reduce the occurrence of ink spitting and take the guess work out of job orders. The most future-forward printers are using Apex’s GTT 2.0 open slalom channel engraving to reduce liquid turbulence.
Optimizing Ink Viscosity and Tack. Ensure your press room temperature is correct for the ink you use. Attempting to use an ink that is too cold or too hot will drastically affect ink release and cleaning. Tacky UV inks can get caught in the corners and depths of hex engravings and be difficult to clean thoroughly. The GTT 2.0 open channel engraving offers continuous flow through the channel which results in greater ink release and easier cleaning. Clean rolls lead to less spit!
Quality Control of Anilox Rolls & Plates. Along with choosing the best anilox engraving, volume, depth and other specifications, it’s important to regularly inspect and maintain your anilox rolls to eliminate ink spitting. Printers can utilize the Veritas Anilox Inspection system to thoroughly inspect, record, and track their anilox performance. Knowing when to send your anilox to the press or to the cleaner can save you a press load of time and money in troubleshooting.
Maintaining Press Speed. The goal is productivity and quality. The goal is to maintain the optimal press speed to balance ink transfer, adhesion, and curing times while eliminating ink spitting and other print defects. This might involve testing multiple variables, switching out different anilox/doctor blade/ink combinations to find the best mix to maintain productivity with little interruption.
Improving the Curing Process. Enhance the UV curing process by ensuring the UV lamps are operating at the correct intensity and well-maintained. It may be necessary to adjust the wavelength and intensity of the UV light or the duration of exposure. The source of the problem may be your anilox roll transferring a too thick layer of UV ink. Ensuring your doctor blades are installed at the right angle and pressure settings can help reduce over-inking and minimize ink spitting. Periodic testing and calibration of the UV system and optimizing your anilox and print sections can ensure consistent performance.
Testing and Prototyping. Before running a full production, conduct tests with the chosen ink and substrate combination. This helps identify potential issues and allows for adjustments in a controlled setting. Maintain stable environmental conditions and take note of humidity and temperature effects on ink, plates and other factors that can cause spitting.
The solution to UV ink spitting has been elusive for many flexo printers. Apex has worked with printers and supplier partners to collaborate on the best solutions, processes, and formulations for success.
GTT 2.0 The Missing Link
To reduce print defects like ink spitting and improve the free flow of ink throughout the anilox, Apex innovated the GTT 2.0 anilox engraving. The open slalom channel engraving facilitates a continuous flow, reducing ink lifting which can lead to ink spitting. With GTT 2.0, printers can be confident that anilox-to-plate pressure, doctor blade pressure, press speed, ink viscosity and other variables won’t impact the aniloxes’ ability to precisely pick up and lay down ink. GTT 2.0 is versatile, proprietary, tested in a variety of applications, from flood coating to process work. It was created to combat known and unresolved print defects in flexo so printers can remain competitive, productive and profitable in their UV ink applications.
There are multiple causes and solutions to ink spitting. It is one of UV printers’ greatest battles. With Apex anilox solutions, printers have begun to not only reduce but eliminate ink spitting in their operations. Contact an Apex representative if you’re struggling with ink spitting and other print quality concerns. We’ll work with you to find the best flexo combinations and processes for your unique operations.