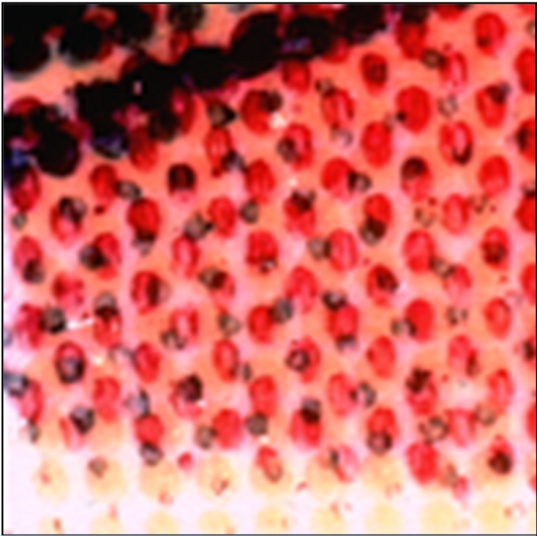
Dot gain in flexographic printing has a variety of causes and shows up in enlarged halftone dots to derformed dots, which can print out fuzzy sometimes. There are several causes of dot gain that are related to anilox rolls, however, there are also solutions to overcome dot gain or decrease it.
In general, all components in the printing unit can be involved in the dot gain. Printing ink (1), anilox roll (2), printing plate (3), adhesive tape (4), printing cylinder (5), impression cylinder (6) and the substrate (7). The anilox roll (2) transfers a determined amount of ink to the printing plate (3).
(Source images: pack.consult)
Here are 5 causes of Dot gain that are related to the anilox roll and also ways to solve Dot gain:
1) Avoid finest dots „dipping“ into the anilox cells.
In order to avoid/decrease dot gain, the screen resolution of the anilox roll must be matched to the screen count of the printing plate. The ratio of the plate screen count to the anilox roll screen ruling is chosen to be approximately 1:6.5 For example, printing a 54 L/cm (140 lpi) screen will set the screen count of the anilox to 340 L/cm (860 lpi) with the smallest dot to print 2% dot on the printing plate, which is a ratio of 1:6.3 in this example.
This prevents the smallest dot from dipping into the ink bubble on top of a cell, picking up more ink than intended, and printing with increased dot gain.
2) Choose the correct volume of the anilox roll
The rougher the substrate surface, the higher the required amount of ink to achieve a smooth ink film thickness. However, if dot bridging or dirty print occurs, a cause could be that the volume of the anilox roll chosen too high.
An anilox roll with a lower volume helps. If you need support, your anilox manufacturer has extensive experience in the correlation of the anilox volume with the specific substrate and can help to do so. You can even determine the volume and line specifications yourself.
3) Avoid high plate pressure
Flexographic printing is a pressure-sensitive process. An increase of the pressure to print solid areas smoothly almost always leads to a higher dot gain in the screens. Choose an engraving solution of the anilox with an optimal ink release. Thinner films of wet ink are easier to control, reduce dot gain, and increase graphic capability. A good ink release of the anilox roll allows homogeneous printing of solid areas with low pressure of the cliché.
Apex offers as solution an open slalom channel engraving pattern of the anilox roll called GTT profile. Its open profile in combination with a shallow channel, lower tolerances and a very consistent ratio between wall and opening makes the difference. This engraving shape has the advantage that a very consistent ink transfer of a defined amount of ink is transferred onto the printing plate. This enables the printing of high-resolution screens together with homogeneous solid areas.
4) Control your process
Flexographic printing is allowing printers to do things in a variety of ways. Having the wrong anilox in your press isn’t always immediately obviously the reason for your printing problem.
With a process control calibration roll you can check print plates and anilox rolls when printing problems occur and you achieve a closed-loop production control. The calibration roll consists of one half GTT XS and the other half GTT S. See how it works in this movie: https://www.youtube.com/watch?v=jCuYtU3b308
Don't forget that Dot gain isn't a simple flexo printing problem... Its causes could be numerous, including issues related to the press mechanics, ink management, cleaning and maintenance and dirty or worn anilox. A brief overview of other influencing factors beyond anilox rolls:
- The printing plate and the adhesive tape must have the correct total height, adjusted to the undercut of the printing press.
- The adhesive tape must have the correct hardness and must be mounted bubble-free.
- The ink must not swell the printing plate from its solvent composition and must be correctly adjusted in its viscosity (in case solvent or water based inks) and the pH value (in case waterbased inks).
- Check all mechanical factors of the machine such as damaged gears or dirty cylinders. The settings of the machine that affect dot gain are for instance anilox to plate; plate to impression cylinder.
- And of course, there are certain types of screens that help reduce dot gain.
In order to determine the right combination on the surface of your anilox, request your anilox calculator (GTT Profiles ánd Hexagonal anilox cells!) here.