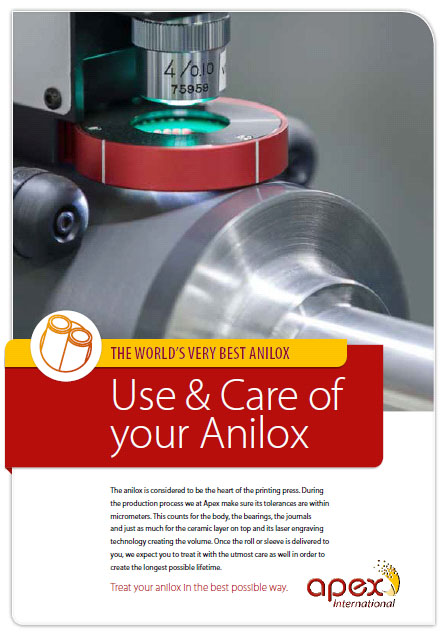
Probably the easiest and fastest way to solve any ink drying problems during print production is to add some drying solvent to the ink. However: it is usually not your ink that is actually causing the problem. It may be worth it to take a different approach and prevent the problem from (re-)occurring.
Flexo printing on corrugated board usually involves water-based inks. Drying these inks involves evaporation into the air and absorption into the board of the water component, leaving the solid components on the surface of the board. Under normal circumstances, these very liquid inks dry very fast; most flexo presses for corrugated do not have a special drying unit.
For the best results in color and print quality, it is important to ensure a smooth ink layer of constant and equal thickness. An ink layer that is too thick or uneven will not only cause quality issues, but also drying problems. If the ink does not dry fast enough on the board, it may smear the backside of the next piece of board, or cause delays in the finishing department.
Now, most quality inks will have been tested and analysed thoroughly by its manufacturers, including for its drying characteristics, to have an optimal performance on press. So if a drying problem occurs despite using inks from a reliable and trusted supplier, it is very likely not the ink but probably your production environment that is causing it.
Getting ink to its final destination in a consistent and stable manner takes quite an effort, involving aniloxes, blades, plates and substrates. Just consider that printing a full color image maybe takes some 2 cm3 of ink. In order to achieve this, the ink flow has to start out with a considerably larger volume of maybe some 10 cm3, as only some 50 per cent of the initial volume passes the first nip – from anilox to plate – and again only another 50 per cent passes the second nip – from plate to board. Control of all factors involved is crucial to get the right amount of ink on the substrate, which in turn ensures both the right print quality and proper drying.
In case of drying problems, adding a drying solvent may very well solve your problem – for now. But please do consider this short checklist to maybe get to a more durable solution:
1) Ink
Make sure it is the right ink for this job, from a trusted supplier and from the right batch.
2) Production environment
The temperature of the pressroom or the press has an impact on the viscosity of the ink that could influence ink behavior.
3) Press
Check the nip between the anilox and the plate, and the nip between plate and substrate. If too much ink is transferred to the surface of the corrugated board, this will cause drying problems.
Make sure you are using the right anilox and ink volume for the job: different substrates may need specific aniloxes. Also check the surface of the anilox: clogged or worn cells disturb the flow of ink and may not transfer the right volume of ink.
4) Substrate
If drying and/or quality problems still persist, there may be a problem with the substrate or the surface of the board that is being printed on.
Find out more about the challenges of printing on corrugated substrates. Understanding the process helps you in getting it right much faster: saving you time and costs and earning you better quality. Experts from Apex are ready to advice and support you on the right type of anilox and how to keep it in the best condition for as long as possible. Contact your technical anilox expert!
We developed a Use & Care Guide with detailed advice on the above mentioned topics. You want one for free? Download the guide here below!