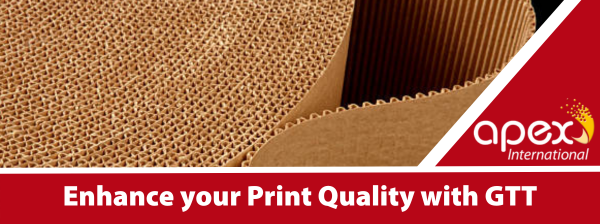
With the rising demand for elaborate box designs and luxury micro-flutes, now more than ever, corrugated print quality is being given a second look. Printing the traditional “this side up” block letter jobs will not be enough to thrive in the future of corrugated packaging. Box makers must learn to master the art of corrugated print to remain competitive and diversify their product portfolio for the sustainable success of the company. 
The anilox roll is one of the biggest factors in mastering quality print production. Choosing the right anilox will bring you one step closer to achieving elaborate, detailed, and vibrant corrugated print, allowing you successful entry into new and growing corrugated markets. Apex International is a global leader in anilox metering solutions and has refined their patented GTT 2.0 open slalom channel anilox engraving to help printers master quality and consistency for exceptionally profitable operations. In this article, we’ll discuss how the GTT 2.0 anilox engraving can help box makers master higher value product lines in box print designs while saving on money, downtime, and waste.
Mastering Corrugated Inks
If you’re like most corrugated printers, you use water-based inks in production. The laydown consistency of water-based inks can positively or negatively impact dry time, press speed, print quality and cleaning/maintenance downtime. Too much ink applied to the board and your print will suffer from smearing, blurry graphics and other print defects from the ink not drying properly at full speed. Too little ink applied, and your graphics may appear spotted and granular from low dot gain and absorption into the paper. The shallow open slalom channel geometry of the GTT 2.0 allows a uniform layer of ink onto the anilox roll and easy transfer to the printing plate. Other longcell or HEX cell geometries are generally engraved too deep, knowing that cell-based engravings always leave a small amount of ink in each cell, clogging the anilox and reducing the color strength on the corrugated sheet. This can result in graphics appearing dull and a subsequent increase in ink consumption to produce a vibrant graphic. The secret to the GTT 2.0 innovation is the 50% reduction in cell wall surface area across the anilox, as well as the decrease in the required channel depth by an average of 25%. Choosing the patented GTT 2.0 design will ensure optimal ink transfer and uniform laydown across the print plate.
Water-based inks can also struggle with foaming issues due to aeration from cell-based engraved anilox roll or aeration from the ink pump or ink system. When ink is pressurized between the cells and the doctor blade, air can be forced into the cells causing micro-foaming. This foaming can result in a splotchy look in your print and will render a portion of your ink unusable. Considering water-based inks is one of the more expensive ink types, it is important to utilize every dollar of ink to maximize your profit margin. The GTT 2.0 anilox cell geometry has been proven to reduce liquid turbulence within the anilox, significantly reducing foaming, without needing the combination of a de-foaming agent and transfer agent in your inks. In a recently published study, a 60-degree HEX engraved anilox and a GTT 2.0 open channel anilox were compared within a production environment. As shown in figure 1, the GTT 2.0 anilox roll showed significantly less foaming, if any, over the hex engraved roll. Time is money and with GTT 2.0 you can master consistent ink laydown, extend ink mileage, and decrease foaming for a profitable print operation.
Master Print Quality
With excellence in ink laydown uniformity and precision established, box makers can swiftly master the art of new box designs with GTT 2.0. The increasing demand for micro-flutes and luxury corrugated means box makers now need to achieve smaller print types, vibrant flood coat colors and soft blends and gradients. This is no easy feat for a box maker accustomed to standard block letter print. However, eCommerce box designs, DTC packaging and POP displays are becoming a more common ask from brand customers and there is no sign of slowing down. To take advantage of these full graphic design jobs, box makers must control their print processes, including the anilox roll and ink system.
The GTT 2.0 anilox roll has a reduced channel depth and open channel geometry to allow inks to easily flow through all channels in the anilox, then to the print plate. Manufactured with the highest T.I.R. and O.D. tolerances, GTT 2.0 is engineered to your exact OEM specifications and measured for quality control throughout the manufacturing process for ultimate print performance (Figure 2). With these innovations, your water-based inks can be consistently transferred to the print plate to achieve finer screens, sharp/crisp text type, bold solids, consistent highlights and undertones, and happy customers. With little or no need for de-foaming and transfer additives, you can decrease print defects such as trapping issues, mottling and pinholing in flood coats, blurred or faded type face and more. Furthermore, GTT 2.0 works exceptionally well in CMYK. These applications require next-level precision and process control, along with a long anilox life, and GTT 2.0 has what it takes to achieve the efficiency and profitability found in added value designs. If you’re looking to master print quality, GTT 2.0 anilox rolls are the heart of achieving this goal.
Master Productivity
Finally, to master corrugated print you must also master production efficiency and performance. If you are constantly stopping production for print defects, troubleshooting, and maintenance, the profitability of your operations will be doomed, and your competitive advantage will be lost quickly. With GTT 2.0 anilox rolls, you can steer clear of the downtime required to troubleshoot for the common corrugated print defects stated above and keep production running with stable, predictable, and repeatable print results. Considering the print quality is covered, let’s talk about anilox cleaning and maintenance.
The open slalom channel geometry of the GTT 2.0 has been enhanced over the last several years to improve its cleanability and extend roll life. Manufactured with a super-hard hybrid ceramic coating and engraved in a wave-like pattern, the GTT 2.0 is extremely durable in production, reducing bounce and downtime for anilox changes. The GTT is also known to maintain print quality consistently throughout the life of the roll. Anilox cleaning and maintenance is a large part of production downtime and GTT 2.0 has been engineered for easier cleaning and less required cleaning to ensure maximum uptime of the press. In a recent Apex study, the GTT C14 engraving was compared to a 130L/cm long cell volume 13.7 over an 8-month period. The results below demonstrate that the new GTT 2.0 required only one deep clean after about 8 months, whereas the long cell required a deep clean about every 3 months (Figure 3). These cleaning requirements not only result in downtime for roll cleaning, but also impact print quality as the roll gets further away from the manufactured volume. 
In conclusion, GTT 2.0 is your key to mastering productive, profitable and high-quality corrugated print. Run your press faster with less drying time, avoid print defects and ink waste, achieve elaborate print designs, and extend anilox usage with minimal cleaning downtime when you choose the patented GTT 2.0 anilox rolls from Apex International. Contact our team today to discuss your operations and we’ll work with you to find the best anilox solution to meet your corrugated print goals.