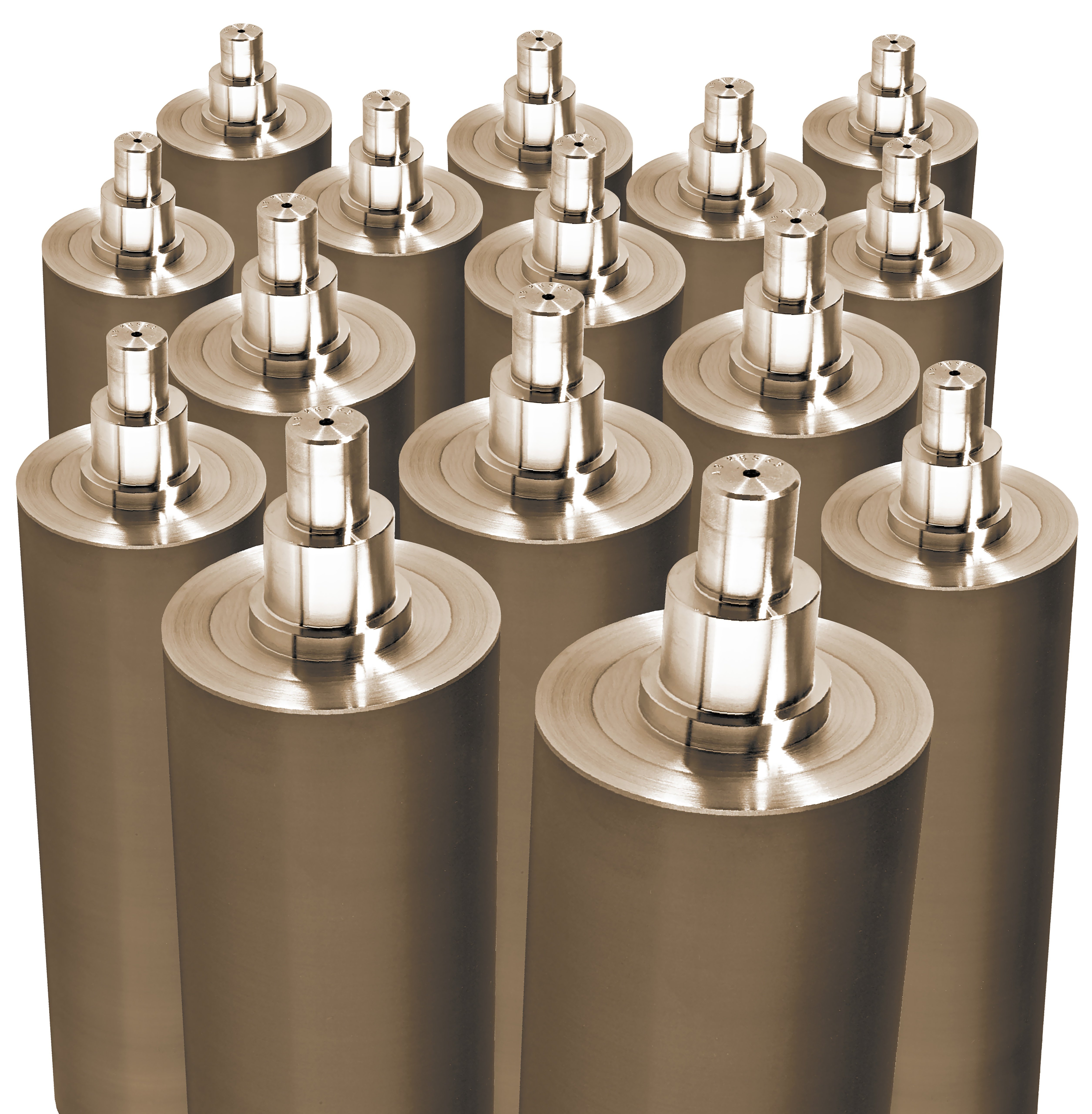
What does innovation have to do with the anilox roller in flexo printing? To answer that question, let’s look at the definition of innovation. “Innovation is the creation, development and implementation of a new product, process or service, with the aim of improving efficiency, effectiveness or competitive advantage”.
Throughout the years, the flexographic industry has grown from being considered “Rubber Stamp” printing to now rivaling Offset and Gravure. This growth can be attributed to one word: innovation.
Years ago, rubber plates were still a widely used means for transferring the desired images. Using polymer plates was a crude process and there were limited plate types and thicknesses available. Dangerous and hazardous chemicals were used to process the plates, and the equipment used was even cruder. Printing presses were clunky, slow, and you were lucky if registration was within half a registration mark away from each other.
But over time, innovative thinkers helped create, develop, and implement new ways of laying ink down on substrates. Platemaking became a more controlled process. There was the development of digital plates, high-speed imagers and thermal plate making technology. These efforts transferred ink better with new plate surface tension technologies, cell patterning and flat top dots. Presses developed from slow geared presses with different pitches to high-speed servo driven race cars, with faster changeovers and setups, easier cleaning and make readies, lighter rolls and sleeves, better doctor blade options, super tight registration, and extremely fast press speeds.
The Function of The Anilox Roller in Flexographic Printing
One of the biggest innovations that directly impacted the "heart" of the printing process is the function of the anilox roller in flexographic printing.
Originally, anilox rolls were steel bases, made using a process of mechanical engraving, utilizing hardened steel tools of various cell counts and cell shapes. Unfortunately, they offered limited engraving specifications. As time went on, the innovators in the industry developed a method for laser engraving, greatly expanding the line screen and volume options. But one innovator wanted to go even further.
.jpg?width=224&height=228&name=Anilox%20rolls%20(HR).jpg)
Apex International decided to help develop anilox technology that would help reinvent how inks and coatings were applied. They started one step at a time. First, Apex took the manufacturing of their bases internally. While other anilox suppliers were being supplied their bases from essentially the same base manufacturer, Apex took a different approach. They wanted to help eliminate the additional cost that was passed on to the end-user. So, they eliminated the middleman and created a lightweight base that was made 100% to OEM specifications.
Then as sleeve options came into play, Apex created their own sleeve. This sleeve features an extra smooth, easily cleaned interior wall that is resistant to swelling. In addition, the corrosion-proof stainless end caps are built into the sleeve itself and this sleeve has the tightest TIR tolerance in the industry (< 0.0005”).
Apex’s sleeves now allow printers the ability to run at high speeds of 2000 fpm. Even at those high speeds, you don't have to worry about bounce. It is the longest-lasting sleeve on the market today, remaining an asset longer and allowing more reworks to be performed before having to be replaced. All these features make it one of the most popular sleeves with OEM’s today. Apex also looked at ceramic hardness, the porosity of the ceramic, and the polishing of the ceramic. From that, Apex innovators developed proprietary methods for all those aspects of the anilox. The result is an anilox that can last longer and provide repeatable results time after time.
Additional Apex Innovations
Next, Apex decided to look at how to improve the ways to transfer ink from the anilox to the plate. This resulted in the invention of the Ultracell. As you know, there is a certain amount of ink that is left in the cell upon rotation of the anilox. Since the Ultracell is a wider and shallower cell, it allows more ink to effectively transfer from the anilox to the plate. The Ultracell releases more ink, improves densities, prints cleaner, and cleans up more efficiently.
But Apex didn’t stop there. They looked at the corrugated segment of flexo and asked, how can we improve print quality?
Wanting to improve again on the way ink flows through the process, Apex invented and patented its GTT engraving technology. This channeled, engraving pattern was designed to provide maximum ink transfer. It achieves this goal by reducing the amount of ceramic wall space by 50% and allowing the ink to flow uniformly and calmly onto the plate. The constant beam of the laser engraving process provides smooth and consistent channel walls.
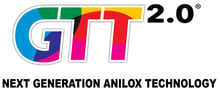
GTT allowed printers to print stronger solids with less mottling and pin holing; sharper and finer type; tighter reverses; finer, cleaner plate screens; with less dot gain, and printing combo work with clean screens and dense solids. GTT also allowed predictable and repeatable print results and helped eliminate ink foaming.
After time went by, Apex saw that GTT could also be effective in flexible packaging and label applications. It's especially useful for those using UV inks, where GTT eliminates UV ink spitting altogether. GTT brought the way ink is transferred to a plate to a whole new level.
Then, Apex investigated how GTT could help in coating applications. They found that the smooth flowing channels of the GTT anilox could evenly and cleanly transfer coatings with various particle sizes much more efficiently than a traditional Hex patterned anilox.
Innovation is the foundation of the Apex philosophy. Apex continuously provides innovative solutions to all their customers and looks at new ways to improve every day. Printers looking for quality, value, consistency, repeatability, and increased profitability, choose Apex. That’s why they are the leading supplier of anilox solutions in the world. There are innovators and there are imitators; who do you want to trust with your anilox? Contact our team today!