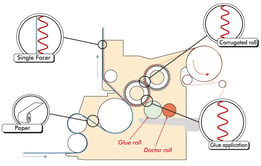
Board quality is the foundation for corrugated excellence and therefore the board used directly affects print results. New materials and improved technologies make it possible to manufacture corrugated board to a much higher standard and realize cost savings on glue consumption and required drying capacity.
![]() |
![]() |
The position of the glue sets in the Corrugator machine for a Singlefacer and a Double-backer
Modern materials
The use of modern materials for manufacturing glue and doctor rolls has many advantages. The ultimate combination is a glue roll with a 3 mm thick hardened stainless steel layer coupled with a doctor roll manufactured with a ceramic layer. This combination guarantees a longer lasting set and eliminates the possibility of oxidation.
Because of the hardness of the material the chance on score lines has decreased, which guarantees a better distribution glue. The direct effect of score lines would be the appearance of ‘warping’ (a slanting dislocation of the cardboard layers). This is due to the fact that locally too much glue is being transferred to the corrugated board (see image).
The effect of score lines on the glue transfer
Improved Technologies
By using new materials and technologies the opening between glue and doctor roll can be reduced from 0,15 mm to 0,10 mm and sometimes even smaller (0,08). The reason for this reduction is the lowered TIR (Total Indicated Runout; which is the deviation in the rotational characteristics of the roll).
In the past it is assumed that the volume of glue transferred onto the corrugated board, has been completely derived from the opening between glue and doctor roll. However, the transfer of glue is also derived from the engraved cells of the glue roll and also here several improvements have been made in the recent past. More on this, in our next blog "How to produce better quality board with less starch".