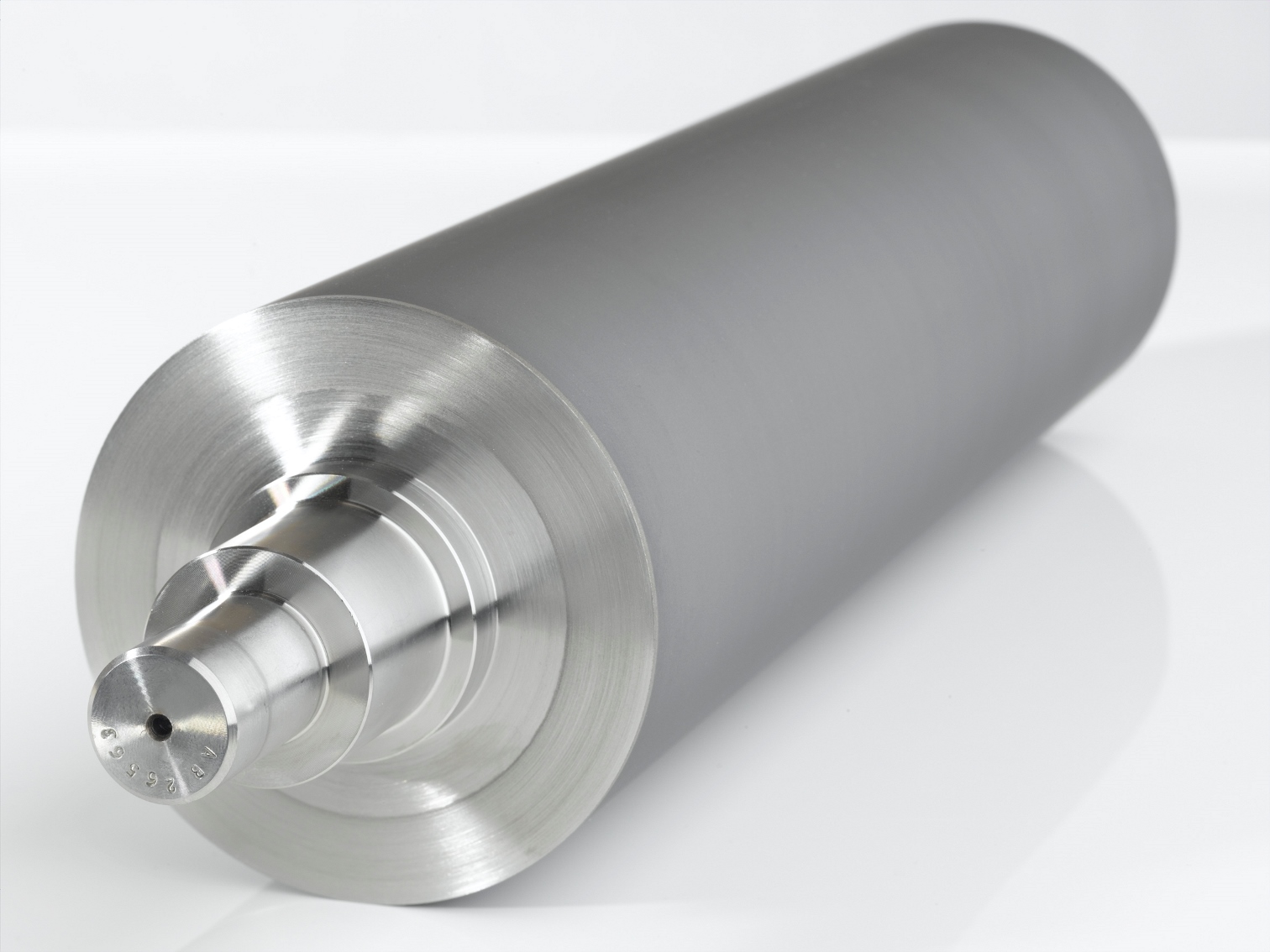
Day by day the flexible packaging, labels and corrugated market are constantly changing depending on the supply-demand that exists in the commercial environment.
The anilox roll plays a very important role in the markets, since as we all know, it is the heart of the printing press. The proper selection of the screen and the volume is a crucial factor in obtaining quality and consistency of the final printed product. However, this is only half of the story.
The selection of lpi and volume will also determine the life expectancy of the anilox roll. In addition, how regularly the anilox is cleaned, has a direct cost implication.
Advances in laser technology for ceramic anilox products allow more screening alternatives and volume combinations than ever before. Old standards have been surpassed with multi-impact technology, taller screens that provide higher volumes, new cell configurations, and S shaped cells. The presses of the last years, in the WW and NW market, now employ quick-change anilox systems using sleeve technology or rollers made from special materials such as aluminum or carbon fiber.
The laser engraved ceramic anilox roll has also played a key role as one of the consistent components that has been continuously improved. Multi-impact engraving technology produces highly consistent anilox rolls. These cells have much smoother walls, flatter bottoms, and a higher definition of the cell surface. This allows for better ink release, more complete consistency in cell volume, less dot gain, improved ink dispensing, and reduced doctor blade wear.
All of this has led to a surprising variety of alternatives for the machine operator, who no longer must limit himself to a screen and volume arrangement but can instead, order a specific anilox with a screen and volume combination tailored to the needs of the machine’s particular application.
Today's aniloxes can be more consistent than ever before; easier to clean, longer lifespan, with greater resistance to wear. However, they can also be high-maintenance rollers since ceramic anilox rolls require more cleaning. In addition, they have a shorter life if the engraving technology is pushed to the limits with high volumes or high screen counts that create weaker, thin cell walls and deeper engravings.
The correct selection of the anilox engraving will depend on several factors such as the type and LPI of the plate that will be printed, the ink strength and the substrate to name a few. Click here to access our online Anilox Calculator.
Wide web
Technological advancements have dramatically improved all aspects of the broadband flexographic printing process. Sleeve presses with tighter registration controls, digital printing plates, high fastness inks that can regain moisture, and improved substrates have all contributed to superb quality and faster speeds. Recent advancements in anilox manufacturing have also given broadband printers engraving options that were not available just a few years ago.
There are three processes for anilox that have improved the technology the most: the application of ceramic coating, cell measurement and laser engraving method and technology. Today the technology allows a ceramic coating hardness of 1,400 Vickers with porosity levels of less than 1 percent as the standard. However, a differentiator is not the porosity but the compactness of the coating. For example, 1% can be one hole or 1% can be accumulated for 1000 microscopic holes. The improvement in the ceramic spraying technique greatly increases the quality and consistency of the cell geometry as well as the life of the roll.
Narrow Web
The narrow web industry has experienced an enormous amount of innovation with respect to online press technology, including all the other key converting components. Flexographic inline printing presses now run much faster, have more print stations, and print on wider webs and thinner substrates.
These servo-driven presses, with automatic registration and change, and equipped with tension control, speed up the start of work, reduce the level of waste and increase production. Their design makes them incredibly flexible and gives them the ability to handle both long and short runs from roll to roll with reverse printing, surface printing, laminating and foil stamping alike.
Corrugated
The corrugated industry has undergone some dramatic changes in recent years. The field of application that printers/converters are being asked to supply has shifted from simple cardboard boxes with a single two-color identification to multi-color point-of-sale displays.
The era of three- and four-color presses, doctor blade chamber systems and ink systems have evolved alongside anilox rollers.
When we consider current demands, we see that requirements have changed greatly in the high-quality graphics and display materials business areas. It is now common to see presses with six and seven print stations, equipped with quick anilox change mechanisms that allow a converter to have an inventory of anilox rolls that can be interchanged depending on the job.
Anilox Roll Cleaner Techniques
To follow the demands made by the industry suppliers of plate and ink and print higher image resolutions, anilox roll manufacturers have created smaller and more concentrated cells. Unfortunately, these small, deep cells have a greater tendency to accumulate dry ink inside adding extra costs.
This sedimentation of the ink/varnish ends up influencing the quality of the printing, since it reduces the volume of contribution. That’s why it is necessary to follow the anilox roll cleaner recommendations. You should clean your anilox rollers frequently with the most suitable products. The goal is to remove all the remains from the bottom of each cell but without damaging the surface. Here’s an interesting fact: a printer can spend more money on cleaning an anilox over its life span than what they paid for the anilox in the first place. It makes sense to discuss the anilox specs with your anilox provider to understand the effect extreme specs will have on the product’s lifespan, frequency of cleaning and potential risks of score lines.
Anilox Cleaning Solutions
The original way to clean the anilox cells consists of applying anilox roller cleaning chemicals which can remove the dried ink from the bottom of the anilox cells regardless of the type of ink used—water-based, solvent, alcohol, or UV. The cleaner is applied once a metal brush (stainless steel or brass depending on the type of anilox) has removed the fresh ink. The bristles of the brush push the cleaner to penetrate to the bottom of the cell where the f dried ink has accumulated. Cleaning the anilox cells with sponges, rags, or plastic brushes are less effective and wear out quickly.
Automatic Cleaning
In the automatic cleaning process, concentrated water-based cleaners are used, and the action of the brush is replaced by the pressure of water and the cleaning product on the anilox. You can program the cycles of minutes for the dosage of the cleaner, time to rest, rinse with water under pressure and drying with air.
Older systems used to clean the anilox would project particles that carry the remains of ink such as bicarbonate or plastic spheres. These systems are no longer in use and have been surpassed by other more efficient and safer anilox roll cleaning systems with a lower cost.
Laser equipment is another physical cleaning technology, set at a different frequency than the one used for recording. With this cleaning process, the projected beams remove ink remnants. They are high-cost equipment that requires precise handling by the operator since improper handling does damage the engraving.
We developed a Use & Care Guide with detailed advice. Do you want one for free? Download the guide here below!