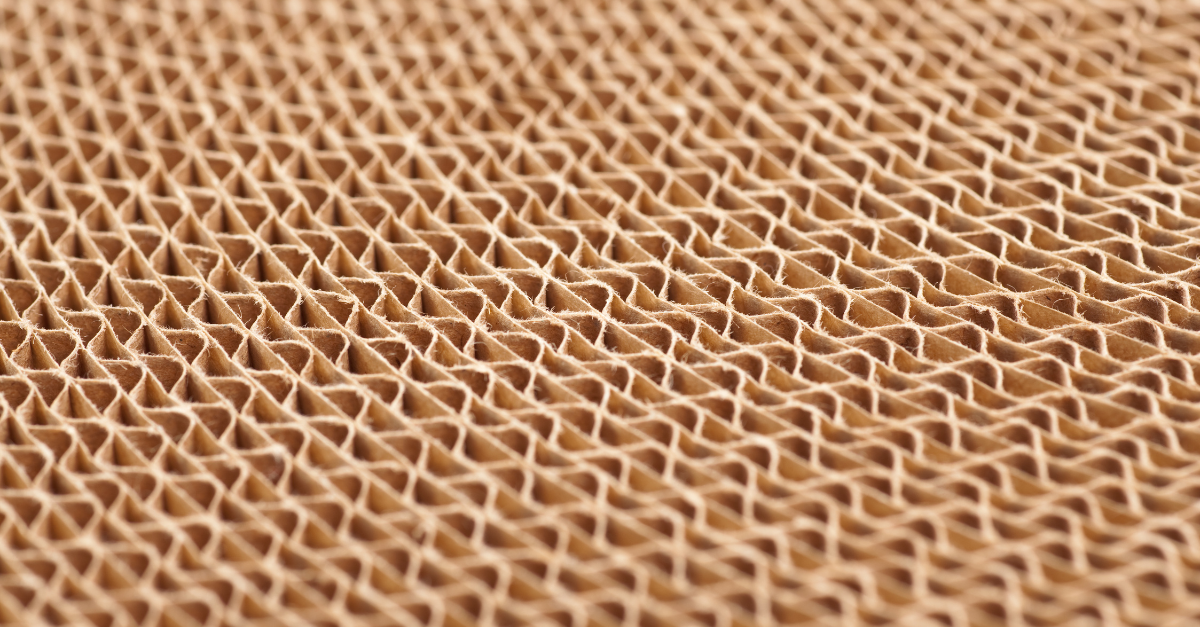
Since 2020, the corrugated manufacturing industry has endured numerous crisis-level events that have resulted in shortages, delays and price increases for raw materials, energy and transportation. The pandemic, along with droughts and storms in the Western hemisphere, have abruptly impacted corn starch supply in the Americas; The war in Ukraine is impacting European industrial starch production; And rising tensions in China and Korea have caused further interruptions in the corrugated supply
chain. According to a recent global starch forecast report, the availability and costs of critical starch materials have become extremely volatile and is expected to remain this way for the foreseeable future. Add in the increase in corrugated packaging demand due to eCommerce, sustainable packaging trends and consumer demand, and we are collectively facing the biggest supply chain giant of our generation.
During the AICC/TAPPI Corrugated Week 2022 Supply Chain panel, executives from SMC Packaging Group and Akers Packaging Service Group echoed the concerns of many manufacturers – namely shortages and delays of raw materials including sheets, starch, pallets, glue and more. Though for every challenge, there is an opportunity to rise above. At Apex International, we are proud to have developed the Accora™ corrugated glue set solution to reduce starch and glue consumption and mitigate some of the supply chain challenges of today’s corrugators.
Reducing Starch & Glue Consumption
The two main factors in reducing unnecessary consumption of glue and starch during corrugated manufacturing are (1) a controlled, precise gap between glue and doctor roll, and (2) the screen, profile, and volume of the glue roll. The gap between the glue and doctor roll is responsible for approximately 70% of the glue application, while the screen, profile, and starch/glue transfer volume account for the remaining 30%. To manufacture glue sets that allow the operators to achieve maximum raw material savings, Apex International developed the best combination of roll materials to ensure the tightest TIR tolerances are achieved and maintained during the roll manufacturing process, resulting in better than OEM specifications.
According to industry best practices, consistent results occur when using a stainless steel glue roll in combination with a ceramic doctor roll. Additionally, the standard engraving of 10 l/cm with volumes of 120 cm3/m2, with an angle of 45° (25 LPI, vol. 78 bcm) and the screen of 15 l/cm with a volume of 60 cm3/m2, also with an angle of 45° (40 LPI, vol. 39 bcm) both deliver consistent, precise results in the application of glue.
Minimal starch consumption and reduced glue volume are the results of strategic engineering, precise, controlled manufacturing and knowledgeable placement of your glue set. Apex International proudly manufactures Accora™ glue sets with precision, durability and excellence to help you save on precious raw materials, without losing board quality.
Built for the Challenges of Corrugated Manufacturing
Accora™ glue and doctor rolls are strategically manufactured by Apex International to be easy on starch, light on glue and high on quality. Through an AST fusion manufacturing process, Apex crafts its applicator rolls with a thick, double-class layer of precision engravable stainless steel, tailored to your machine’s exact OEM blueprints. United with the proprietary hydrophobic, low-porosity ceramic layer on the doctor rolls, Accora™ glue sets are capable of achieving industry-leading Outside Diameter (OD) and Total Indicated Runout (TIR) tolerances – maximum of 0.0005” TIR. With Accora™, Corrugators can confidently specify any gap - down to 0.007”- safe in the knowledge that Apex glue sets will achieve the most controlled, uniform and straight gap across its width. This consistently minimal glue-to-doctor roll gap results in less starch required to achieve ultimate bond strength.
The benefits of Accora™ glue and doctor rolls ripple far beyond raw material savings. The reduction in starch equates to a reduction in moisture applied to the paper, allowing corrugators to turn down the steam boiler. This generates savings in heat and energy costs, easing the rising fuel and energy concerns in corrugated manufacturing, as well. Fewer customer rejections, less finished goods waste, higher machine speeds and maximum roll life are other notable benefits thanks to the precise gap control, reduced starch consumption and quality roll materials with Accora™.
With no clear path to supply chain normalcy, it’s important to invest in solutions designed to minimize the challenges of today and outlast the woes of tomorrow.
For over 25 years, Apex International has been committed to serving the corrugated manufacturing industry with precision, innovation and excellence. Let us help you navigate the complexities that come with a volatile market – contact our team today!