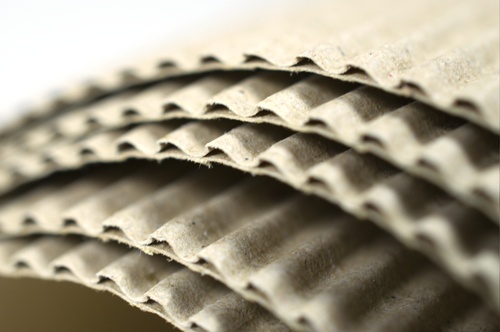
Consumers in the corrugated industry are demanding a decrease in starch consumption. And not just for the cost savings either. Instead, it is the thinner, weaker paper – with weights as low as 80 grams - that are used for gluing board. This type of paper requires the application of less starch, as little starch as possible in fact.
Add the fact that both water and heat are enemies of paper; applying too much water, has a negative effect on the smooth application of starch requiring more or longer drying, with all negative consequences for the quality of the paper. Another trend seen in the industry nowadays, is the fast-growing market for E-flutes and Micro-flutes. The flutes per linear meter for E-flute board are 295 (90 in inches), requiring a consistent application of a low dose of starch onto the board! Both Tappi and Fefco publish informative production information with regards to industry trends and developments.
The application of the level of starch is influenced by two factors:
- The gap between glue and doctor roll;
- The screen/profile on the glue roll
The gap between glue and doctor roll applies for approximately 60% of the glue application and this parameter can only be controlled by using the tightest tolerance in the manufacturing process of both the glue and the doctor roll. This is mainly determined by the materials that are used to manufacture the glue set, and its durability and reliability on the long term. Best results are reported when using a stainless steel glue roll in combination with a ceramic doctor roll. Of course, both have to be according to OEM specifications, even after one or two times reconditioning. In this case, special attention has to be given to the diameter build up of both rolls, preferably with durable materials such as steel or stainless steel.
2nd parameter determining almost 40% of the volume of starch/glue that in the end is transferred onto the Corrugated board, is the screen of the glue set.
Theory behind finer screen counts
Gluing of board can very well be compared to the printing of board. In theory, a finer line count or finer pattern, results in a more detailed print result. The exact same happens with the application of glue: a more even layer of glue is applied onto the board.
However, in all honesty, it is also necessary to mention that the finer the line count, in most cases, also the shorter the lifetime of the glue rolls is. In the recent past, very good results were achieved with screen counts of 50 l/cm (130 lpi). Beautiful even layers of glue were applied onto the board, but the minute the glue roll came into contact with the corrugator roll, very easily damage occurred to the fine walls of the cells, creating all sorts of issues like score lines.
Together with leading companies in the corrugated industry, glue set manufacturers discovered a compromise that is currently often used while producing board, in the situation of Single-facers as well as Double Backers. A standard engraving of 10 l/cm with volumes of 120 cm3/m2, with an angle of 45° (25 lpi, vol. 78 bcm) and the screen of 15 l/cm with a volume of 60 cm3/m2, also with an angle of 45° (40 lpi, vol. 39 bcm) both deliver very consistent and satisfying results in the application of glue.
![]() |
![]() |
![]() |
|
CONCLUSION:
Optimal starch consumption and reduced volumes are only possible with a reduced gap and the absolute tightest tolerances on the doctor roll and glue roll. Furthermore, the application of glue is determined by the screen count, as well as the screen pattern. It may be worth asking your glue- and metering roll manufacturer for the latest developments in this particular field of surface engravings, in order to realize significant cost savings thanks to improved board quality, reduction in paper waste, less starch consumption and less energy consumption (for drying).