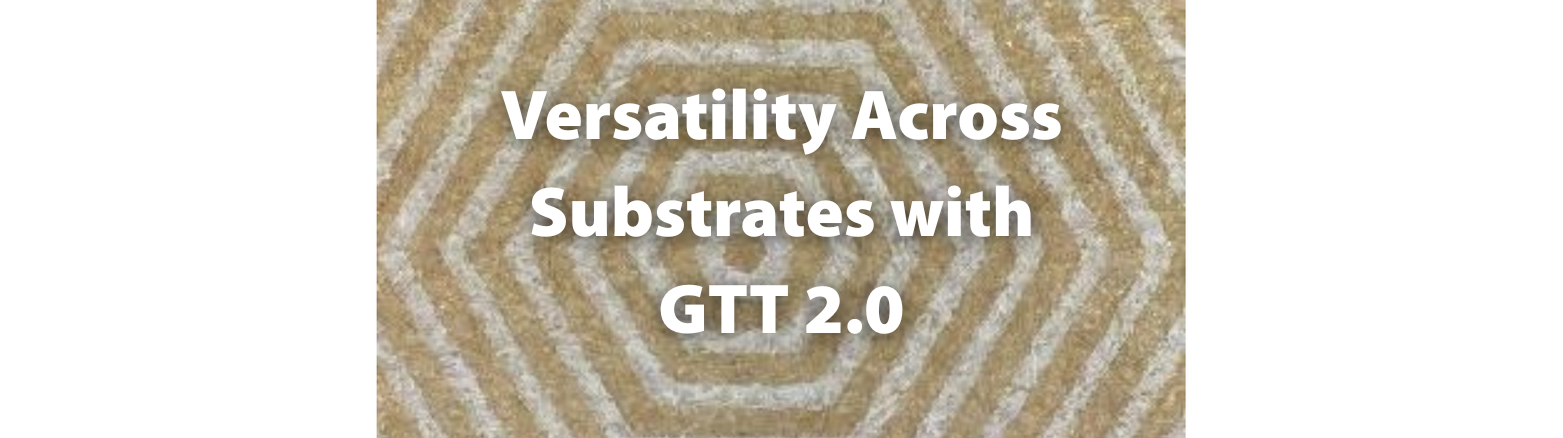
Corrugated printing demands versatility. Packaging comes in a wide variety of substrates, from lightweight recycled papers to rough kraftliners, and each substrate poses unique challenges in terms of ink absorption and surface texture, these factors ultimately affect print consistency. Achieving high-quality results across such a broad range of materials often requires ink adjustments or anilox changes and subsequent down time and lost revenue.
Apex International’s GTT 2.0 technology is changing the game in corrugated printing by delivering a consistent performance across a variety of substrates—all with a new anilox technology solution.
Whether you're running coated, uncoated, or recycled board, GTT 2.0 gives you a wider ink transfer range. That means fewer anilox changes, smoother ink laydown, and excellent print quality, without constant adjustments to ink or rollers. It’s a smarter, more efficient way to print.
In this blog, we’ll dive into the versatility of GTT 2.0, showcasing how it excels on a variety of corrugated substrates through a recent trial that highlights the technology’s superior adaptability and precision.
The Challenges of Printing on Diverse Corrugated Substrates
Each corrugated substrate presents its own set of printing challenges:
Coated paper tends to have a smoother surface that can lead to ink smudging or over-inking if not controlled properly.
- Uncoated kraftliner, with its fibrous and absorbent texture, makes it difficult to achieve consistent ink coverage without overusing ink.
- Recycled paper often has an uneven surface, which can result in patchy or streaky prints, especially when printing large areas of color.
Traditional anilox rolls often require ink adjustments on press or even an anilox change depending on the substrate, and even then, the results can be inconsistent, leading to waste and inefficiencies. Finding a solution that works consistently across these different substrates is crucial for corrugated printers looking to maintain print quality and efficiency, regardless of the material they’re working with.
GTT 2.0: One Technology, Multiple Substrates
GTT 2.0 is engineered to deliver precision and consistency across a wide range of substrates.
Its patented open-channel design provides controlled, even ink distribution—ensuring the right amount of ink is applied every time. This flexibility gives printers a broader performance window across different materials, reducing the need for constant press adjustments and lowering the risk of print defects between jobs.
In a recent trial, we tested GTT 2.0 on three different substrates: coated kraftliner, uncoated kraftliner, and recycled paper. The goal was to assess how well GTT 2.0 could maintain print quality and consistency across these varied materials, compared to traditional anilox technology.
The Results: Consistency Across Every Substrate
The trial results confirmed that GTT 2.0 delivers outstanding performance across all three substrates. Here’s what we observed:
Coated Kraftliner: GTT 2.0 achieved excellent results on coated kraftliner, providing smooth, sharp prints without any smudging or over-inking. The ink laydown was consistent, and there was no need for additional adjustments to the printing press. Traditional anilox rolls, by comparison, often lead to ink pooling or smearing on coated surfaces, but GTT 2.0 prevented these issues entirely.
Uncoated Kraftliner: When printing on uncoated kraftliner, GTT 2.0 maintained strong color density and clean edges. The ink penetrated the fibrous surface of the kraftliner evenly, creating a solid print without the need for heavy ink applications. The open-channel design allowed for better ink flow, minimizing patchiness or uneven coverage, which is a common issue when using traditional anilox rolls on this substrate.
Recycled Paper: Recycled substrates often have an inconsistent surface, making it difficult to achieve high-quality prints. However, GTT 2.0 performed exceptionally well, delivering smooth, even coverage without any streaks or gaps. The ink transfer was consistent throughout the print job, and the adaptability of GTT 2.0’s ink flow system meant that fewer adjustments were needed between substrates.
Case Study: Multi-Substrate Printing with GTT 2.0 (GTT M)
In this trial, we used GTT M engraving to print the same design—a mix of solid colors, gradients, and fine details—on three substrates: coated kraftliner, uncoated kraftliner, and recycled paper. Each substrate posed unique challenges, yet GTT 2.0 delivered high-quality results across all of them without the need for significant adjustments.
Coated Kraftliner: The design printed on the coated kraftliner had bright, vivid colors with smooth transitions in the gradients. The fine details were sharp, and there was no smudging or over-saturation of ink.
Uncoated Kraftliner: On the uncoated kraftliner, GTT 2.0 maintained clean, solid color coverage without the heavy ink usage typically required on absorbent surfaces. The result was a well-defined print with no patchy areas.
Recycled Paper: The print on recycled paper was smooth and consistent, with the ink filling in the surface irregularities without causing streaks or defects. This was particularly impressive given the challenges of printing on recycled materials.
The ability of GTT 2.0 to deliver such consistent results on a variety of substrates highlights its versatility, making it a go-to solution for corrugated printers working with diverse materials.
The Benefits of Versatility in Corrugated Printing
For corrugated printers, versatility means fewer headaches and more streamlined production. Having a single technology that performs well on multiple substrates can reduce downtime, minimize waste, and improve overall efficiency. With GTT 2.0, printers can:
Reduce material waste by achieving high-quality results on the first pass, regardless of the substrate
- Lower ink consumption across all materials due to GTT 2.0’s precise ink control
- Simplify setup and adjustments since GTT 2.0 requires fewer changes between substrates, making it easier to maintain consistency throughout the print run
- Deliver consistent, high-quality results across a wide range of substrates, meeting the demands of diverse customer needs
Conclusion: GTT 2.0 Delivers Versatility and Quality
The ability to print high-quality designs on multiple substrates is a must in today’s competitive corrugated printing industry. GTT 2.0 technology excels in this area, providing consistent, reliable results across a variety of materials without the need for constant adjustments or reprints. Whether you're printing on smooth, coated surfaces or rough, absorbent kraftliners, GTT 2.0 adapts to the substrate and ensures the best possible outcome every time.
For corrugated printers looking to improve both their print quality and their operational efficiency, GTT 2.0 offers the versatility needed to meet the challenges of printing on multiple substrates. By streamlining production and reducing waste, GTT 2.0 enables printers to deliver exceptional results while saving time and resources. To learn more, contact us today.