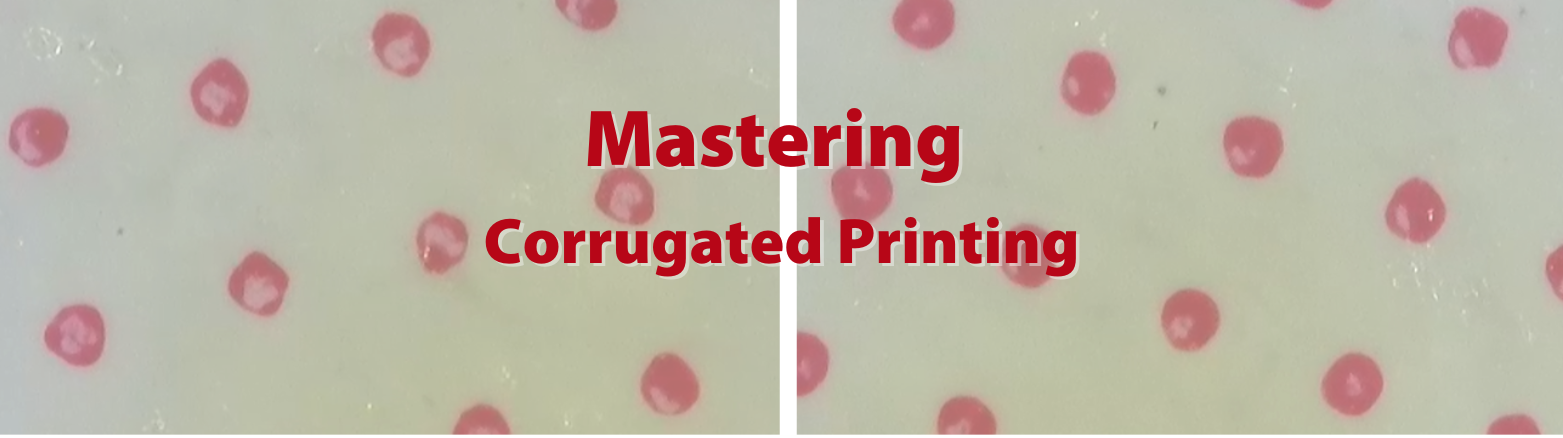
Corrugated printing often presents unique challenges, particularly in achieving consistent ink density and smooth laydown. Corrugated substrates - especially those that are uncoated or recycled - often have rough, uneven surfaces that make it difficult to apply ink uniformly. This can lead to patchy coverage, uneven color density, and even ink wastage.
With Apex International’s GTT 2.0 technology these common obstacles can be overcome. GTT 2.0 offers a revolutionary solution that ensures not only higher ink density but also better overall ink distribution. In this blog, we’ll dive into one of our recent trials, where we tested GTT 2.0’s ability to lay down ink more efficiently, resulting in deeper, richer colors and fewer defects, even on difficult corrugated substrates.
The Importance of Ink Density in Corrugated Printing
Ink density refers to the amount of ink deposited and how smooth is applied to the substrate, which directly affects how vivid and consistent the printed colors appear. When printing on corrugated materials, achieving consistent density is tricky due to the texture and absorbency of the substrates. Corrugated boards—such as kraftliner or recycled paper—can absorb ink unevenly, leading to variations in color coverage and vibrancy.
Traditional anilox technologies often struggle with controlling ink flow on these substrates, resulting in patchy prints or low-density areas. This inconsistency can cause colors to look faded or uneven, which reduces the overall quality of the print. For brands that rely on bright, eye-catching packaging, this can lead to dissatisfaction with the final product and, ultimately, reprints or redesigns—both costly and time-consuming.
GTT 2.0: A Solution for Higher Density and Better Ink Laydown
GTT 2.0 was purposefully engineered to meet the demands of achieving high-density ink coverage in corrugated printing. Its innovative open-channel structure optimizes ink flow and provides precise control, ensuring even distribution across the entire substrate. This technology excels on challenging surfaces such as kraftliner or recycled paper, delivering consistent ink density that results in brighter, more vibrant colors. A key advantage of GTT 2.0 engravings is their ability to provide a smoother, more uniform ink layer by completely eliminating air introduction during the ink transfer process.
The Problem with Conventional Anilox Cells
With conventional anilox technology, as ink is transferred to the print plate, the cells fill with air. During the re-filling process in the doctor-blade chamber, this air is repeatedly introduced into the ink, creating a pump-action interaction. The result? Microbubbles form in the ink, disrupting its consistency during production.
To counteract this issue, operators often rely on manual additions of antifoam and transfer additives. While these additives address foaming and ink instability during the press run, they introduce a separate challenge when the ink is returned to storage.
The Hidden Cost of Manual Additives
At the end of a production run, leftover ink—referred to as "ink returns"—is typically sent back to the ink store for future use or remixing into a new color. Unfortunately, these reused inks often lack accurate records of the additives introduced on the press.
This unbalanced chemistry can lead to a host of print defects when reused, including:
- Mottling: Uneven ink distribution causing a blotchy appearance.
- Pin Holing: Small, unprinted spots due to air trapped under the ink.
- Furry Edges: Blurred or uneven print edges.
- Trapping Issues: Poor adhesion of subsequent ink layers.
These defects not only compromise print quality but also lead to increased downtime and wasted materials.
The GTT 2.0 Solution
Switching to GTT 2.0 Anilox Technology eliminates the need for manual additives like antifoam and transfer agents. This advanced engraving technology ensures:
- Air-Free Ink Transfer: Prevents the formation of microbubbles, delivering consistent and stable ink transfer.
- Maximum Ink Utilization: Reduces waste and allows for better reuse of leftover ink without compromising chemistry.
- Improved Print Quality: Minimizes the risk of defects such as mottling, pin holing, and trapping issues.
- Operational Efficiency: Reduces press downtime caused by ink imbalances and rework.
By adopting GTT 2.0, printers can achieve more efficient ink usage, better quality control, and enhanced production reliability—delivering superior results while reducing costs and environmental impact.
In one of our most recent trials, we tested GTT 2.0 on B-flute coated testliner and compared the results with a traditional anilox roll. The goal was to measure how well each technology handled ink density and laydown, particularly in high-coverage areas where achieving consistent color is key.
The Results: Higher Density and Smoother Laydown
The trial results were clear—GTT 2.0 outperformed the traditional anilox roll in both ink density and overall ink distribution. Here’s what we observed:
- Higher Ink Density: GTT 2.0 achieved deeper, more saturated colors across the entire print area. The difference was especially noticeable in areas with high ink coverage, where the colors appeared richer and more uniform than those produced by the traditional anilox roll. This higher density is crucial for brands that rely on bold, vibrant packaging to stand out on the shelf without using a higher amount of ink.
- Smoother Ink Laydown: One of the standout features of GTT 2.0 is its ability to lay down ink smoothly, even on uneven surfaces like corrugated boards. In this trial, GTT 2.0 provided consistent coverage with minimal patchiness or streaking, even in areas where the substrate was more textured. This smooth laydown reduces the need for multiple print passes, saving both time and materials.
- Fewer Print Defects: Traditional anilox rolls often result in print defects like dot gain and uneven coverage. In contrast, GTT 2.0’s controlled ink flow minimized these issues, producing cleaner, sharper images with fewer visible imperfections. This level of precision is essential for brands that require high-quality prints, even on complex or challenging substrates.
Case Study: High Coverage Printing on Coated Testliner
For this trial, we used B-flute coated testliner, a material commonly used in corrugated packaging. This type of substrate requires high ink density to ensure that colors appear vibrant and consistent, particularly in high-coverage areas like backgrounds or large logos.
We printed a design with heavy ink coverage using both GTT 2.0 and a traditional hexagonal anilox roll. The results were compared side by side, focusing on ink density, smoothness, and overall print quality.
- Ink Density: The design printed with GTT 2.0 had significantly higher ink density, especially in areas with large blocks of color. The traditional anilox roll, on the other hand, produced areas where the color appeared faded or less vibrant.
- Ink Laydown: GTT 2.0 achieved smoother ink laydown across the entire print, with no visible streaks or uneven patches. The traditional roll struggled with consistent coverage, leading to areas with patchiness and visible defects.
- Ink Efficiency: Because GTT 2.0 uses ink more efficiently, less ink was required to achieve the desired color density, resulting in lower ink consumption. This not only saves on material costs but also reduces waste, contributing to a more sustainable printing process.
Reducing the Need for Reprints
One of the major benefits of using GTT 2.0 is the reduction in reprints due to inconsistencies in ink density. In traditional printing setups, achieving the perfect balance of ink density often requires multiple passes, increasing the risk of misalignment or ink buildup. This trial demonstrated that GTT 2.0 can achieve consistent results in a single pass, eliminating the need for costly reprints and reducing production time.
The Benefits for Corrugated Printers
For corrugated printers, the ability to achieve higher ink density with smoother laydown means better overall print quality. Whether printing large areas of color or intricate designs, GTT 2.0 ensures that the final product will meet the expectations of even the most demanding clients.
Some key benefits for printers include:
- Higher print quality with fewer defects
- Reduced ink consumption thanks to more efficient ink usage
- Smoother ink laydown across various corrugated substrates
- Faster production times due to fewer print passes and reprints
Conclusion: Elevating Print Quality with GTT 2.0
In today's competitive packaging market, exceptional print quality is a non-negotiable for success. Whether it’s the vibrancy of the colors, the smoothness of the ink laydown, or the consistency of the print, every detail counts. GTT 2.0 technology has proven to be a powerful tool for printers looking to achieve high-density ink coverage with fewer defects and greater efficiency.
As we’ve seen in this trial, GTT 2.0 not only produces deeper, more vibrant colors but also does so with greater ink efficiency and fewer print imperfections. For brands that rely on high-quality packaging to make an impact, GTT 2.0 offers a solution that delivers superior results without the limitations of traditional anilox rolls.
Stay tuned as we continue our blog series where we’ll explore more ways this technology is transforming the corrugated printing landscape.