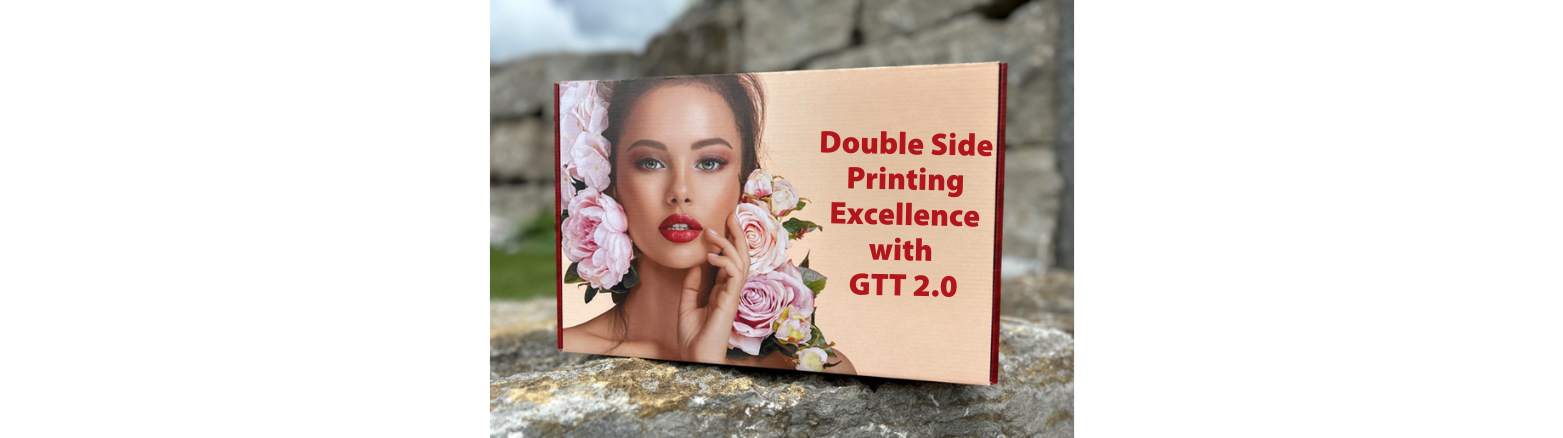
In today’s fast-paced printing industry, maximizing efficiency while maintaining high print quality is key. Corrugated printers are constantly looking for ways to streamline processes, reduce production time, and lower costs without sacrificing the final output. One of the most effective solutions to this challenge is double side printing, a process that allows both the inside and outside of packaging to be printed in a single pass.
Apex International’s GTT 2.0 technology takes the additional inside printing to the next level by providing superior ink control, enabling seamless transitions between print areas, and ensuring consistently high-quality results. In this blog, we’ll explore how GTT 2.0 enhances the efficiency and precision of double side printing, using a recent trial as an example of the technology’s powerful capabilities.
What Is Double Side Printing?
Double side printing refers to the ability to print on both the inside and outside of a package in one production run. This process is particularly useful in corrugated printing, where packaging often requires both an exterior design and interior branding, such as company logos, promotional messages, or product details. Traditional methods typically require multiple passes to complete both print areas, which increases production time and costs.
Inline duel side printing not only speeds up the printing process but also reduces the risk of misalignment between the two print areas. However, it presents a unique set of challenges, particularly when printing on corrugated substrates like kraftliner. Maintaining consistency in ink coverage and print quality across different surfaces in a single pass can be difficult, especially with traditional anilox systems.
The GTT 2.0 Advantage in Inline Printing
GTT 2.0 technology is designed to address the specific challenges of this printing process by offering precise ink control and distribution. Its open-channel structure ensures that ink flows smoothly and evenly, enabling printers to handle multiple print areas simultaneously without compromising quality. Whether you’re printing on the smooth exterior of a package or the rougher interior, GTT 2.0 adapts to the substrate and delivers consistent results across both surfaces.
In one of our recent trials, GTT 2.0 was used to print both the inside and outside of a corrugated package in a single pass. The substrate was B-flute uncoated kraftliner, which is known for its absorbent, fibrous surface that can make it challenging to achieve clean, sharp prints, particularly in a duel side printing process.
The Results: Efficiency and Precision in a Single Pass
The results of the trial clearly demonstrated the advantages of using GTT 2.0 for this process. Here’s what we observed:
- Consistent Ink Laydown Across Multiple Surfaces: One of the standout benefits of GTT 2.0 is its ability to maintain consistent ink coverage across different print areas. In this trial, we printed a detailed
design on the outside of the package, while the inside featured branding elements. Both print areas, despite their differing surface textures, exhibited smooth, even ink laydown with no visible defects.
- Seamless Transitions Between Print Areas: GTT 2.0’s controlled ink flow allowed for seamless transitions between the inside and outside print areas, with no loss of quality as the print process moved from one surface to the next. This is particularly important in double side printing, where misalignments or inconsistencies between print areas can detract from the overall appearance of the final product.
- Time and Cost Savings: By completing the entire print job in one pass, GTT 2.0 drastically reduced production time and material waste. Traditional methods would have required two separate runs to print the inside and outside of the package, increasing both time and costs. With GTT 2.0, the printer was able to achieve high-quality results more efficiently, lowering overall production costs.
Case Study: Double Sided Printing on Kraftliner
For this trial, we printed on B-flute uncoated kraftliner, a common substrate in the corrugated packaging industry. Kraftliner’s rough texture often makes it difficult to achieve smooth ink laydown, particularly when printing large areas of solid color or intricate designs.
Using GTT 2.0, we printed a two-part design featuring:
- A full-color graphic on the outside of the package
- Text and logos on the inside, printed on brown kraftliner
Here’s what we found:
- Outside Print Quality: The exterior print, which included large areas of color and detailed imagery, came out clean and sharp. GTT 2.0’s superior
- ink control allowed the ink to flow smoothly across the rough kraftliner surface, producing a vibrant and consistent print.
- Inside Print Quality: On the inside, the print quality was equally impressive. Despite the darker, more absorbent surface of the kraftliner, the logos and text printed with crisp edges and strong contrast, with no signs of ink spreading or blurring.
- Single-Pass Efficiency: Perhaps the most significant result was the ability to achieve all of this in a single pass. Both the exterior and interior prints were completed in one go, showcasing GTT 2.0’s ability to streamline the inline printing process while maintaining high-quality results.
Benefits for Corrugated Printers
For corrugated printers, the ability to efficiently print both the inside and outside of packaging in a single pass is a game-changer. By adopting GTT 2.0, printers can significantly increase their productivity without compromising on the quality of the final product.
Some key benefits include:
- Increased production speed: With GTT 2.0, printers can complete complex jobs more quickly by printing both sides of the packaging in one pass, reducing production time and increasing throughput.
- Reduced waste and costs: By eliminating the need for multiple runs, GTT 2.0 helps reduce material waste and lower production costs, making it a more sustainable and cost-effective solution.
- Consistent print quality: Whether printing on smooth or rough surfaces, GTT 2.0 ensures consistent ink coverage and sharp, clean prints across both the inside and outside of the package.
Conclusion: Double Sided Printing Excellence with GTT 2.0
This duel printing method is an essential process for corrugated printers who need to balance efficiency and quality in today’s competitive market. GTT 2.0 technology offers the perfect solution by enabling high-quality, consistent results on both the inside and outside of packaging in a single pass. With its superior ink control and distribution, GTT 2.0 not only enhances the quality of the print but also significantly reduces production time and costs.
As more printers move toward inline processes to meet customer demands for faster, more cost-effective production, GTT 2.0 provides the precision and reliability needed to excel in this area. Whether you’re printing intricate designs or solid color blocks, GTT 2.0 ensures that every print job is completed with the highest level of quality and efficiency.
Stay tuned for more insights from our blog series, “Mastering Corrugated Printing with GTT 2.0: A Revolution in Precision,” as we continue to explore how GTT 2.0 is transforming the corrugated printing landscape.