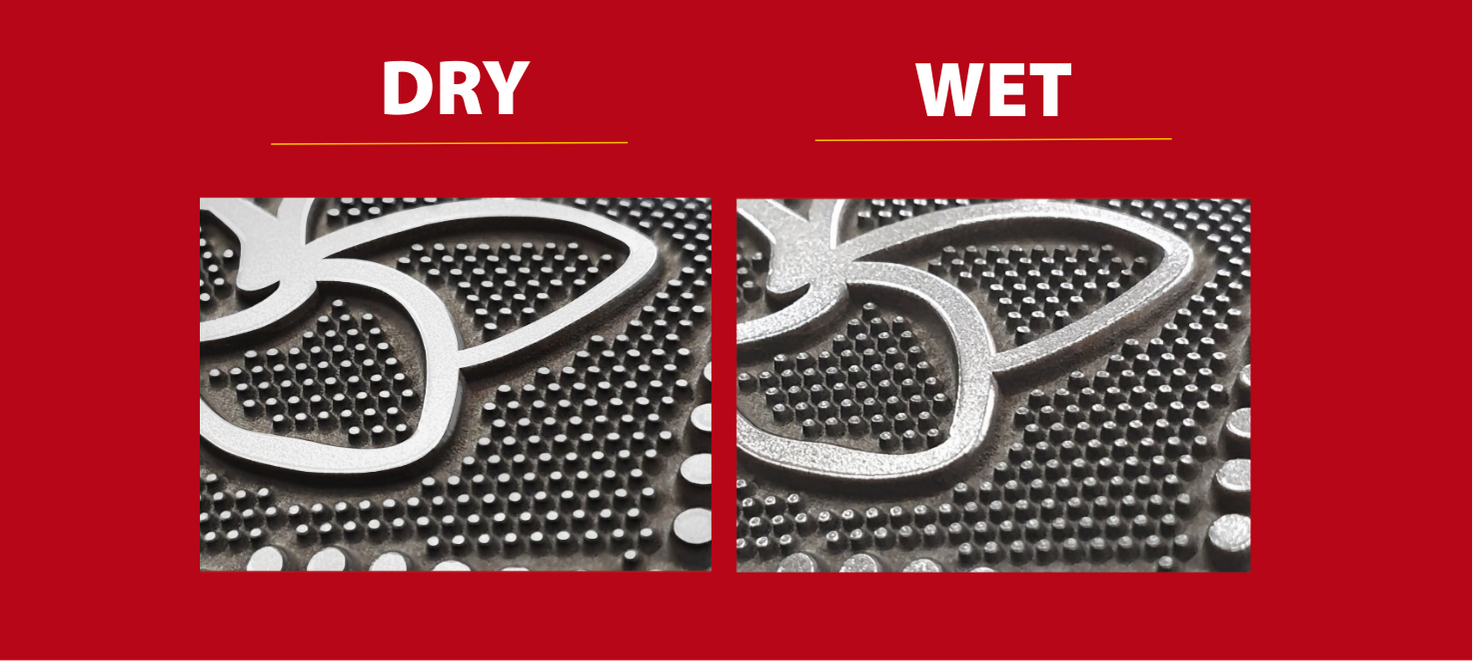
In the precision-driven field of metal embossing, advancements in laser engraving technology are crucial for achieving superior quality, efficiency, and sustainability. Two key technologies in this space are wet laser engraving and dry laser engraving.
While wet laser systems have been widely used for traditional engraving, dry laser technology sets a new benchmark with its environmentally sustainable approach and exceptional versatility. This makes it the preferred choice for businesses looking to modernize and embrace eco-friendly solutions.
Metal Embossing Technology Overview
Metal embossing requires precision and durability, making laser engraving the go-to method for high-quality results. Let's explore how wet laser engraving and dry laser engraving compare in key areas, including material versatility, environmental impact, and efficiency.
Wet Laser Engraving Technology
Wet laser engraving has been a trusted method, particularly in embossing laser engraved rolls. However, when applied to metal embossing, its limitations become evident:
Key Features of Wet Laser Engraving:
- Stylus-Based Engraving – Utilizes diamond styluses, providing reliable but limited precision.
- Limited Material Versatility – Primarily optimized for gravure cylinders, restricting its adaptability to broader embossing applications.
- Dependency on Wet Processes – Requires water and solvents for cooling and cleaning, leading to increased chemical waste, higher operational costs, and greater environmental impact.
Dry Laser Engraving Technology (Apex Unique Specialized Engraving)
Unlike wet laser engraving, dry laser technology is specifically tailored for metal embossing, offering significant improvements in efficiency, sustainability, and flexibility.
Key Advantages of Dry Laser Engraving:
- Direct Laser Engraving – Eliminates intermediary steps, engraving intricate designs directly onto various metals.
- Broad Material Compatibility – Works with aluminum, stainless steel, copper, brass, and more, making it suitable for diverse industries.
- Eco-Friendly Dry Process – Does not require water or solvents, reducing waste and improving operational efficiency.
Why Dry Laser Engraving Outshines Traditional Wet Processes
1. Dry Process: A Game-Changer for Sustainability
Wet Laser Engraving:
- Requires significant water and solvent usage, generating chemical waste.
- Leads to higher operational costs and an increased carbon footprint.
Dry Laser Engraving:
- Completely eliminates the need for water and solvents, drastically reducing waste and environmental impact.
- Directly aligns with corporate sustainability goals and regulatory compliance.
2. Material Versatility & Expanded Applications
Wet Laser Engraving:
- Optimized for gravure cylinders, limiting its use to specific metals and applications.
Dry Laser Engraving (Apex Unique Specialized Engraving):
- Works with a wide range of metals, including aluminum, stainless steel, copper, and brass.
- Supports diverse applications, including decorative embossing, industrial labels, security features, and high-precision packaging.
3. Superior Precision & Design Flexibility
Wet Laser Engraving:
- Stylus-based engraving struggles with hard metals and complex designs.
- Limited depth control restricts precision for intricate patterns.
Dry Laser Engraving:
- Uses advanced diode-pumped solid-state lasers for high-speed, deep engraving.
- Allows for intricate textures, sharp details, and greater depth control, enabling more complex embossing designs.
4. Environmental & Economic Benefits of Dry Laser Engraving
Zero Waste & Lower Environmental Footprint
Wet Laser Engraving:
- Generates water and chemical waste, requiring specialized disposal systems and higher energy consumption.
Dry Laser Engraving:
- A completely dry process with no chemical runoff or water usage, reducing environmental impact while cutting costs.
5. Energy Efficiency & Reduced Downtime
Wet Laser Engraving:
- Consumes more energy due to cooling requirements and stylus-based mechanical wear.
- Requires frequent stylus replacements and solvent maintenance, increasing downtime and costs.
Dry Laser Engraving:
- More energy-efficient, using advanced laser technology without additional cooling needs.
- Minimal maintenance, resulting in higher productivity and long-term cost savings.
Why Dry Laser Engraving is the Future of Metal Embossing
Apex Unique Specialized Engraving offers the most advanced and sustainable metal embossing solution, delivering:
Industry-Leading Sustainability
The dry laser process completely eliminates water and chemical waste, reducing both operational costs and environmental impact.
Unmatched Material Flexibility
Capable of engraving a variety of metals, expanding applications into:
- Decorative embossing
- Industrial labeling
- Security features
- Premium packaging
Exceptional Precision & Detail
Advanced laser technology enables deep, intricate, and high-relief designs, offering superior quality in embossing projects.
Conclusion: A Clear Advantage with Dry Laser Engraving
While wet laser engraving has served traditional gravure and embossing applications, dry laser engraving represents the next generation of high-precision, sustainable manufacturing.
- Zero-waste process – No chemicals, no water, no unnecessary disposal costs.
- Expanded material applications – Supports diverse metals and industry-specific needs.
- Unrivaled precision and efficiency – Enables intricate embossing with maximum repeatability.
For companies prioritizing sustainability, operational efficiency, and advanced manufacturing capabilities, dry laser engraving is the superior choice. By adopting this innovative technology, businesses can reduce costs, meet environmental mandates, and position themselves as leaders in the evolving embossing industry.