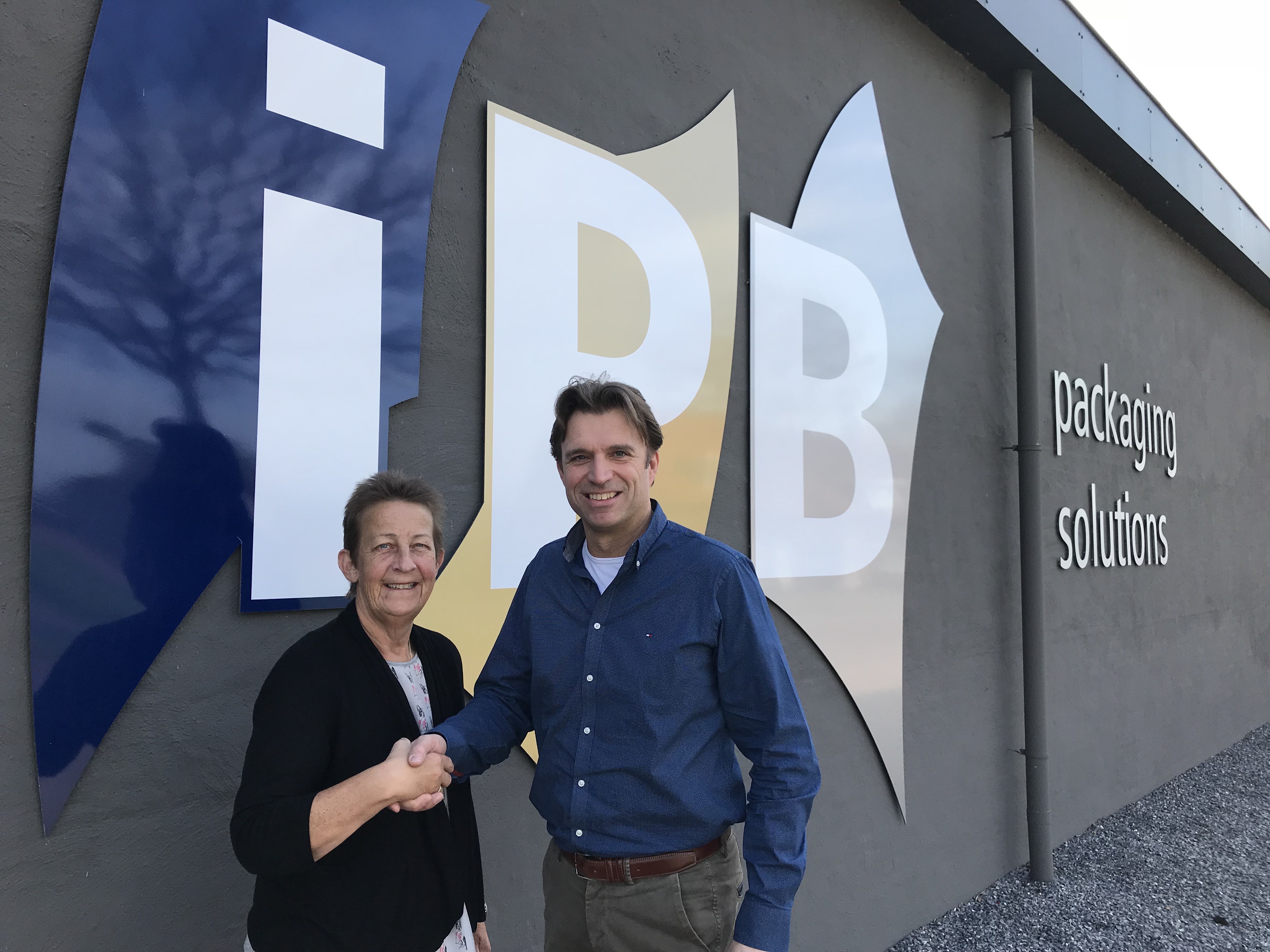
Ton Lavrijsen and his brother Bart are today’s third generation at the helm of the iPB family business. Having recently installed two brand new Bobst 10-colour flexo presses, they are ready to once again push the limits of innovation in packaging solutions. “Technology is really the tool that enables us to excel in what differentiates us from our competitors: product development. That is why it is also important for us to partner with specialists like Apex International: by combining skills and knowledge, we can both improve and innovate faster.”
The company has never been shy of change and has always been eager to explore new business opportunities, says Lavrijsen: “Innovation is really part of our DNA.” Founded in 1938 as a dairy business, the company evolved into an import-export business in the cakes and confectionery sector in the 1970s. As the business continued to expand, they moved in 1988 to new premises – that still houses iPB today. It is also the place where it set up its own packaging and printing business in the 1990s: “Initially, we ordered preprinted labels that we imprinted ourselves with ingredient-details before shipping the goods to retailers all over of Europe. Eventually, we started to take care of the complete label printing process for our suppliers.”
Around 2000, the dairy and confectionery industry underwent dramatic changes, with suppliers forming large conglomerates to be able to deal directly with international retail organizations. Ton and Bart Lavrijsen needed to change course and shift gear. They decided to focus entirely on developing what was up until then still a sideline of their core business: “That is, devising and producing flexible, innovative packaging solutions for a wide range of customers with specific wishes.
Image: Ton and Bart Lavrijsen, owners of iPB Printing in front of the state-of-the art Bobst Flexo press
Product development is key
Their print business took off fast after its start in 2003, only to hit a rocky road as the financial crisis took a heavy toll on the printing industry as a whole. “We managed to survive the shake out, partly because next to adhesive labels, we also produce flexible packaging and in mould labeling. But more importantly: we consider ‘product development’ to be our true field of expertise, not ‘printing’. Of course, printing needs to be perfect – and we set a very high standard indeed – but our knowledge surrounding the printing process is what differentiates us from others. Combining these three different segments of packaging under one roof enables us to exchange technical innovations from one to another. For example, we now use die-cutting technology from our adhesive labels segment for our in mould business, and we leverage our knowledge on pretreatment of materials across segments.”
Ton Lavrijsen explains how even the best printing presses will be unable to meet expectations without having the right plates, inks and materials: “You need to be able to control the process from start to finish. It is all about getting the combination exactly right, all ways and every time: not just once in a test run for a 1,000 meters, but also for 100,000 meters in 85 different varieties. It needs to be fast, good and predictable. Operating according to the ‘Digital Flexo’ principles allows us to offer customers our superb ‘iPB ColourAssist’-colour system.” It is for exactly that reason that the two newly installed Bobst presses have been modified to the exact wishes of iPB Printing. “And it is also why we have involved Apex International to supply us with their anilox rollers.”
Consistent ink transfer
Anilox rollers are a crucial part of the printing process, says Lavrijsen, as they need to provide a consistent and precise ink transfer: “And that is all the more difficult, as we do not use standard inks or primers at iPB Printing. Printing with UV inks brings its own set of additional challenges, as does printing white on clear materials.” Apex’ laser-engraved GTT rollers with its patented Open Slalom Ink Channel anilox surface geometry are set to offer iPB Printing new solutions to these challenges. Additionally, GTT will enable new ways to further explore the opportunities of Fixed Palette printing in seven colours: “We really look forward to be printing much of our products in this way in future. So far, print results may be perfect for adhesive labels, but we still see room for improvement on various materials that we use in flexible packaging and in mould labeling. So we need to enhance this concept and tailor it to our specific products and materials, and to the quality our customers expect from us.”
Image: Marian Waterschoot (CEO Apex International) and Ton Lavrijsen (iPB Printing) see the value of cooperation in R&D to bring the flexo process to a higher level
Partners in R&D
Besides continuing to invest in its own research and development program, iPB is also looking to work together with ink and plate suppliers, press manufacturers and other specialists: “As we try to find ways to push the limits of technology so we can develop new products, we need suppliers to help us accomplish that. Apex is a perfect example of such a company we now partner with – by change even located only some kilometers from our facility. Their experts and our technicians will be able to put their skills and knowledge together and make giant leaps forward.”
The fast changing packaging market offers many opportunities to iPB, says Lavrijsen: “Diversification in packaging, shorter runs in more varieties, fast turn around and just in time deliveries – these are challenging trends for both us and our customers. To keep up with changing demand from consumers, brand owners are constantly developing new products. New products need new solutions. And that is where we come in.” At iPB Printing, ‘innovation’ is not merely a buzzword, concludes Ton Lavrijsen.”
More info: