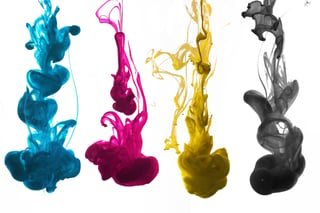
Global Environmental awareness is driving the printing industry to consider other ink systems in order to print more ecological packaging. Water-based inks are often praised as the green solution for a more sustainable product. They are a comparatively eco-friendly product, but when it comes to printing inks on to films and plastics, water creates problems…
- Unless we print on high absorbency substrates, water inks require significant heat to dry and to leave a cured ink film on the substrate. In other words, they require energy that negates any positive ecological benefits from the use of water-based inks.
- Water has a high surface tension, which can print beautiful perfect dots however creates mottled/pinholed solids, which means that in order to 'wet out' on most plastic surfaces, the surface tension has to be reduced considerably in order to achieve good print quality and smooth laydown of ink. That is done by adding a surfactant or a solvent, which contaminates the water immediately. Depending on the substrate, the type of press, the printing speed, the amount of solvent can range between 2 – 20% of the press-ready ink.
- Waterbased ink is also susceptible to foaming creating micro bumbles which thickens the ink and creates a reduced ink transfer. In order to solve this, the ink can be adjusted with anti-foam agents which in turn create drying issues and trapping problems.
- Water has to be combined with solvents in order to dissolve the kinds of resins that provide good adhesion on packaging films. Read: more chemicals!
- Switching from a solvent based ink to a water based ink cannot be done overnight, because of the different transferring capabilities. It often means modification to the anilox rolls because a shallower, more open cell structure is required to print water based inks.
- Contamination between solvent inks and waterbased inks creates an adversus chemical reaction that can result in the ink setting solid and then a major cleaning of anilox, pumps, pipes is required. Therefore, a press is required to be dedicated to waterbased inks to ensure press efficiency is maintained and waterbased ink print is viable.
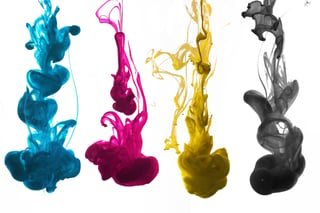
Having touched on the characteristics of water based inks here above, it cannot be left unmentioned, that critics have doubts on the printability of water based inks as well. They appear to result in:
- Poor scratch and rub resistance (especially shortly after printing)
- More difficult to re-wet
- More difficult to clean
- Comparatively lower gloss and poorer color strength
- Ink sets onto the plates creating ink build up and an inconsistent print
- Slow drying and therefore more heat/energy required
- Highest risk of clogging inside the anilox cells (especially with low-volume anilox rolls)
- Very difficult to control and guarantee a consistent and repeatable ink transfer (because of the pH and viscosity)
Water based inks – the future of printing!
Still, ink suppliers and also machine manufacturers dare to announce that water based inks are the future of printing. And a major part of the success of printing water based inks, lies in the actual transfer of the ink. Many of the above print issues can easily be solved when the right configurated anilox roll is used.
Apex International have performed several successful trials together with different ink brands in combination with leading machine manufacturers. The results reported by the ink manufacturers was:
- The shallow surface structure of the open-slalom laser engraving technology developed by Apex, results in no clogging. The most effective ink transfer allowing for the maximum ink replenishment within the Anilox surface compared to the restricted limits of any conventional engraving is realized. A very thin layer of ink can be transferred and less drying time is needed (energy savings!).
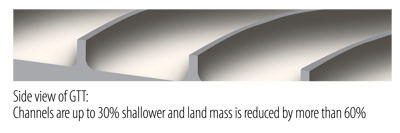
- Major advantages with no air inside the print process. In a closed-cell structure (image left), air gets trapped inside the cells and especially with waterbased inks, that is a disastrous combination. With the open-slalom structure (image right), the ink flows freely and the air will not get stuck inside the cell, it simply flows away. Less air simply means a better lay down of ink and better results on gloss and color strength. A side effect of having no air inside the print process, is the fact that a defoamer is no longer needed, which makes water-based printing an even more 'green' way of printing packages.
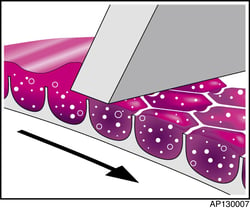
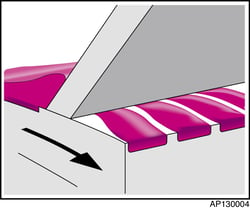
- With an open structure, the phenomen Dot Dipping does not occur. The explanation is simple: pressure causes counter-pressure, ink escapes through the opening and the result is over-inking. The water-based ink does not set onto the plates and will not cause ink build up and therefore inconsistent print is no longer an issue. The below image shows this:
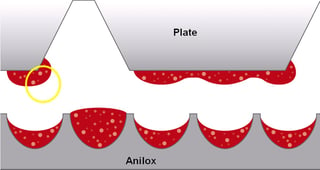
- The key to the success of waterbased inks is to control the viscosity and the pH and the key benefit of the open-slalom surface structure is a consistent ink transfer and the ability to print repeatable results with no air inside.
Conclusion: the last 5 print issues (out of the 8 mentioned) caused by waterbased inks, can be improved by using Apex GTT Anilox technology, which is a very good step in the right direction of a greener Flexo future.
Samples of waterbased prints performed by different ink brands on 3 different machine types are available.
See physical proof of state-of-the art ink-transfer technologies
that obviously supercharge your water based inks!