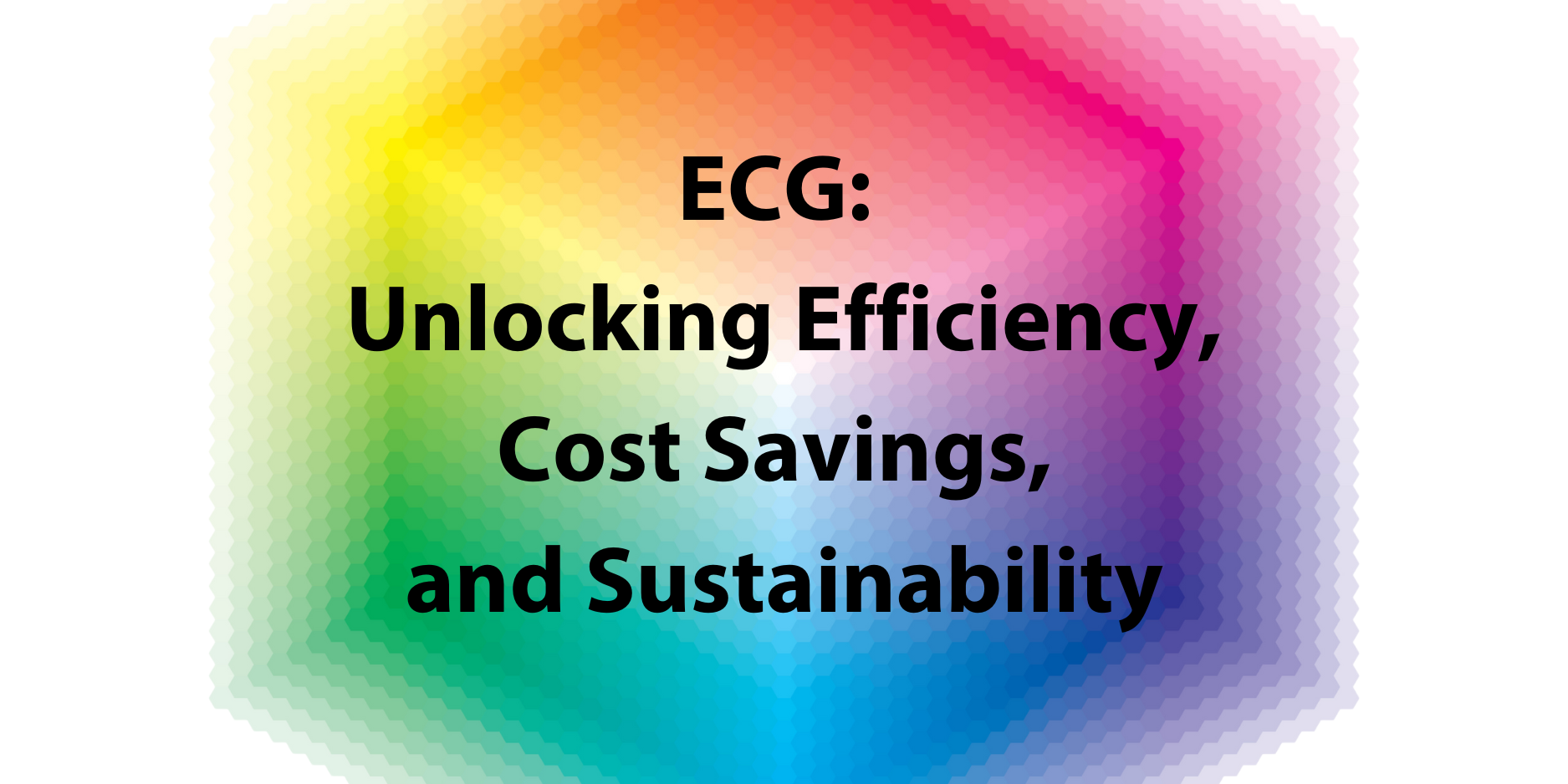
Understanding Expanded Gamut Printing (ECG)
Expanded Gamut Printing (ECG) has been a transformative concept in the printing industry for decades. The fundamental principle of ECG is the creation of printed colors by overlapping two or more core colors from the spectrum of Yellow (Y), Magenta (M), Cyan (C), Black (K), Orange (O), Green (G), and Violet (V) or Blue. Though often seen as a recent innovation, ECG's roots stretch back over 25 years, evolving alongside printing technology.
The concept of expanded gamut printing first gained attention in the 1990s when printers began overlaying Yellow with Magenta to create vibrant reds for promotional flashes in print designs. By 2007, the introduction of Hexachrome colors brought ECG into more printing discussions, highlighting its potential for cost savings, reduced wash-ups, and enhanced color options. Despite these advantages, ECG has yet to become the standard flexo printing process. Why?
Challenges in Standardizing ECG for Flexo Printing
While ECG offers clear benefits, its adoption has been slow due to the technical challenges primarily related to consistency and predictability. Color builds in ECG rely on theoretical mathematical models that assume perfect printing conditions. However, real-world variability in plate resolution, ink viscosity, and anilox technology has made widespread implementation difficult.
Historical Technical Barriers to ECG Adoption
Plate Screen Resolution Limitations
In the 1990s, the maximum plate screen resolution was 100 LPI (lines per inch). This was insufficient for ECG, as the human eye could see the dots in the color builds, leading to dull and inconsistent colors. The ideal resolution for ECG printing is 175 LPI, a standard that is now widely used in both wide-web and label printing, making ECG more viable today.
Ink Viscosity and Flow Control
Consistent ink viscosity is crucial for maintaining predictable color reproduction in ECG. Early printing presses lacked the necessary controls for ink viscosity, temperature, and flow rates. Modern flexographic presses have significantly improved in these areas, ensuring better ink stability and reducing color variability.
Evolution of Anilox Engraving Technology
Anilox rollers and sleeves play a critical role in ink transfer consistency. Over the years, engraving technology has advanced from 800 LPI to finer engravings—up to 1400 LPI today. However, while finer engravings improve print resolution, challenges remain in controlling ink transfer due to changes in cell shape, wall thickness, and volume capacity.
For example, an 800 LPI anilox roller has a 25-micron cell opening with a 7-micron wall, whereas a 1400 LPI roller has an 11-micron opening with the same 7-micron wall. Such changes impact ink transfer efficiency and cleaning frequency of the anilox, influencing ECG reliability.
Apex International’s GTT 2.0: An ECG Enabler
Apex International has addressed many of the challenges associated with traditional anilox technology through its revolutionary GTT 2.0 engraving. This technology provides superior ink transfer consistency and volume control, making ECG printing more predictable and efficient.
Key Advantages of GTT 2.0 for ECG
-
Optimized Ink Transfer
- Traditional anilox engravings struggle with maintaining a balanced ink transfer ratio. GTT 2.0 uses an optimized opening-to-depth ratio, ensuring efficient ink flow and reducing inconsistencies.
-
Reduced Cleaning Requirements
- Unlike conventional engravings, GTT 2.0’s controlled surface ensures minimal ink build-up, reducing cleaning frequency and improving productivity.
-
Enhanced Color Density and Repeatability
- The laser-controlled engraving process eliminates inconsistencies common in pulse engraving methods, ensuring uniformity across multiple anilox rolls.
Why ECG is Essential for the Future of Flexo Printing
With advancements in technology, ECG is now more practical and cost-effective than ever. The benefits include:
✅ Cost Savings: Reduces ink consumption and minimizes the need for expensive spot colors. Studies show ECG can cut ink costs by up to 30% and wash-up solvent costs by 90%.
✅ Increased Press Efficiency: Eliminates frequent ink changes, enabling up to 80% press efficiency compared to traditional 40-45% efficiency levels.
✅ Superior Print Quality: Produces high-resolution (175 LPI) prints with improved color consistency using advanced screening technology.
✅ Sustainability: Lowers ink and solvent waste, making it an eco-friendly printing solution.
Overcoming Myths About ECG
Despite its benefits, misconceptions still exist about ECG:
❌ Myth: Brands and End Customers Won’t Accept ECG
✅ Reality: All Digital printing is printed using ECG. If the brands and customers accept Digital print, they will accept Flexo ECG.
❌ Myth: ECG Requires Printing with All 7 Colors on Every Job
✅ Reality: ECG selectively uses only the necessary colors, optimizing ink usage. Using only four colors will still yield huge cost savings.
❌ Myth: ECG Can’t Match Spot Colors
✅ Reality: Modern ECG technology reproduces up to 85% of Pantone colors with a Delta E of 2.5 or lower.
❌ Myth: ECG is Too Complex to Implement
✅ Reality: With Apex GTT anilox rollers, ECG becomes easier to implement with consistent and repeatable results.
Start Your ECG Journey with Apex International
If you’ve tried ECG before and faced challenges, now is the time to revisit it with the latest technological advancements. Apex International’s GTT 2.0 technology provides the missing link, making ECG more efficient, cost-effective, and easier to adopt than ever before.
Are you ready to unlock the full potential of ECG printing? Contact Apex International today to discover how we can help you maximize efficiency and profitability.