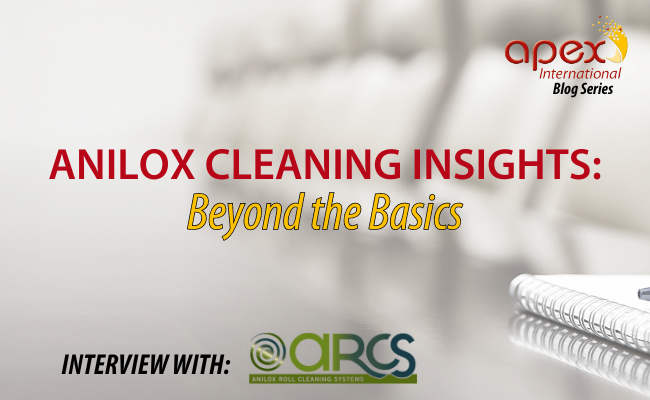
Welcome to the first installment of our blog series, where we go deep into the world of anilox cleaning techniques. Throughout this series, we will feature discussions with industry-leading experts and insights directly from the manufacturers. With a multitude of suppliers worldwide claiming to offer the ultimate solution for anilox roll cleaning, printers find themselves navigating a complex landscape, striving to identify the most efficient cleaning method that aligns with their operational needs and budget constraints.
At the forefront of this discussion is Apex International, recognized globally as the largest supplier of anilox rolls. A common question encountered on a daily basis revolves around identifying the optimal cleaning method for anilox rolls. Traditionally, the response to this inquiry has been vague, largely due to the diverse applications of anilox/metering rolls. With these rolls being used across a wide variety of liquids, including water-based inks, UV inks, solvent-based inks, adhesives, latex, and more, it's understandable why a one-size-fits-all solution proves challenging for Apex.
To shed light on this critical topic, Nick Harvey, Apex International's Technical Director, has collaborated with key suppliers of anilox cleaning equipment. Together, they aim to explore different cleaning methods and provide expert advice on each product. Join us as we embark on this enlightening journey into the complex world of anilox roll cleaning, sharing invaluable insights from industry leaders every step of the way.
Interview with Anilox Roll Cleaning Systems (ARCS):
Nick Harvey: It’s good to sit down with you. Glad to have you as part of our blog series on anilox care maintenance. I know you regularly contribute to discussions and forums in the industry on this.
Jeff Paduano: Hi Nick, it's a pleasure to join you. I'm grateful for the chance to be a part of your blog series on anilox care maintenance. Contributing to industry discussions is something I value highly, and I look forward to providing your readers with a thorough overview of the intricacies involved in anilox cleaning.
Nick Harvey: We’ll get straight into it then. What are the main methods of cleaning you’re seeing around the world today?
Jeff Paduano: For the most part, the methods in use today are the same methods companies have been using over the past decade or two, including Ultrasonics, Chemical Wash systems, and Baking Soda Blasting. The one method that does have a lot of buzz around it right now is Laser Cleaning. Although this too has been around for quite some time in Europe, it has started to become very popular here in the states over the last few years. What is different today vs. the past amongst all of these methods are the improvements – most of the systems I see today are easier to use, more reliable, and generally speaking do a good job at roll cleaning.
Nick Harvey: Do you have different recommendations for customers in the Corrugated, Label, Wide Web, and Coating sectors?
Jeff Paduano: Yes.
For Corrugated and even some Wide Web applications, many companies come to us for On-Press Cleaning options. We have some clients who use very large cylinders in their operation – some over 250” long! Cleaning these rolls and even smaller ones “On-Press” greatly reduces the risk of roll damage since less handling is involved. It’s also quicker – even very large cylinders can be deep cleaned On-Press in 1 – 2 hours, and once it’s done you are up and running again right away. Just the time to remove and then re-install a jumbo roll can take longer than this. Up till now, the only viable On Press method was Baking Soda Cleaning Systems. They have come a long way…. today’s systems are dust-free, highly portable, and very easy to use. However, we also now offer an On-Press Portable Laser Cleaner – it’s gaining popularity and is a testament to an overall industry trend to utilize sustainable technology wherever possible.
For Label and Narrow Web shops, we find they usually adopt Ultrasonic cleaning. The technology has improved, they allow for automated multi-roll cleaning, and typically are quick. Narrow Web companies have many rolls on hand, and obviously these are much easier to remove from the press vs. Corrugated Rolls and other large cylinder types. Ultrasonics offer convenience, small footprints, and although they do produce hazardous chemical waste, it’s usually a manageable amount. For really large label plants, I do also see Laser Cleaners starting to enter this market.
Wide Web and Coating operations are harder to categorize from a cleaning standpoint. They still use the aforementioned methods, but many times with limited results. However, more and more companies in this segment are exploring Laser Cleaning because other methods just don’t work. In the past, we met some clients in this segment who would give up on cleaning their plugged rolls and instead send them in for resurfacing. Lasers can remove unwanted contaminants better than any other method on the market today, including exotic coatings, metallic-based films, and many others.
Nick Harvey: How do you see the trends in the world today?
Jeff Paduano: Overall, I see a very positive economic trend for the packaging sector – most of our clients are at full capacity with healthy backlogs, we see new plants opening up, and demand is forecast to continue to rise for the foreseeable future.
Operationally, in order for Converters to meet their client’s ever-changing demands, it requires new ink or coating formulations. We see an enormous amount of innovation in this area. This trend has an unfortunate consequence – many of these new “recipes” generate stubborn residues. Being able to maintain the rolls used in operations like these is becoming more and more challenging. We continue to hear stories from people who spend hours cleaning their rolls.
We also know companies have to adapt to shorter runs and quicker turnarounds – this amplifies the need to maintain cell volumes and implement a strong Roll Maintenance Program – this “quickening” of the whole production process is here to stay and not every company will be able to adapt to the new pace.
Solution-wise, Laser Cleaning is gaining momentum, and I anticipate this trend to continue for many years to come. It’s for all the right reasons – precision cleaning, automated technology, and sustainable.
Lastly, more and more Converters are investing in advanced roll inspection / 3D cameras – another trend we see continuing. The newer ones available today supply all the data and images you need to properly manage one’s roll inventory. These new cameras work quickly and hold up in a plant environment.
Nick Harvey: This is the perfect setting to speak openly. What guidance can you provide regarding cleaning routines on a daily, weekly, and monthly basis?
Jeff Paduano: Maintaining your rolls in today’s hectic production environment is critical to success. We do recommend all press operators perform a press-side wash cycle after each shift or job. This feature is available on virtually all presses today, doesn’t take long, and has the added benefit of cleaning out pumps, chambers, etc. Another tip we share with operators is to never let the roll run dry – if your job doesn’t require the use of all downs, you should still run water over it. Doing this can prevent many headaches!
Weekly, we tell people to “know your roll.” This step is also quick but important. We recommend each production roll gets visually inspected using a hand-held scope, spot-cleaned where needed, and checked for volume. This step can reveal damage or wear and allow a company to better plan for the future. Do I need to replace this roll? When does it need to be deep cleaned again? Should I call my roll rep to help me understand what I am seeing?
Monthly meetings to stay on top of each roll’s condition is another best practice. Management involvement at this step goes a long way in showing the team how important roll maintenance is and can jump start conversations around how to improve the housekeeping routine, discuss new materials being run, and fosters a good culture of continuous improvement.
Nick Harvey: Do you believe there's a distinction between regular cleaning and deep cleaning, or is it simply a matter of an anilox being clean or dirty?
Jeff Paduano: Yes, I do – although deep cleaning is inevitable, in most cases, a good daily program (see above) will lengthen the time between deep cleanings. However, we are familiar with numerous operations who need a “like-new” roll for each job they run. For these plants more frequent deep cleaning is the only way to accomplish this. For other types of operations, we recommend scheduling a deep cleaning once cell volume is reduced by 25-30%.
Nick Harvey: What do you perceive as the primary factors influencing your customers' decisions, and could you rank them in order of importance? These factors might include environmental sustainability, energy efficiency, cleaning duration, adaptability to different roll sizes, operational costs, ease of use, purchase price, and any other considerations I might have overlooked.
Jeff Paduano: Great question! My rankings are based on our collective experience but certainly many plants may have other priorities to consider.
1. Automation
For Off Press Systems, Automation matters. All of us are feeling the effects of the labor shortage – being able to set up a roll for cleaning, press start, and then walk away until the cycle finishes is a very important feature for clients today.
For On-Press applications, I am not aware of any true automated options due to the nature of the process. Our On-Press equipment is automated – once the operator mounts the equipment to the press frame, they can step back and just watch. But watching is important – it ensures no cords or hoses get tangled up by accident. There are other safety measures that get followed while cleaning On-Press, so leaving the print station while the equipment is operating is just not an option.
2. Cleaning Quality
As mentioned before, some companies are faced with removing very tough build ups. For plants who only run water-based inks, they have more options to choose from as all of these systems are pretty good with that type of residue. If instead you need to remove UV Inks, unique coatings or varnishes, then you will find not all cleaning systems are created equal.
3. Risk of Roll Damage
The Anilox Roll is a high value, mission critical component for any printing operation. Most people have heard the expression that it’s “the heart of the process.” Roll damage caused by the cleaning method itself still happens, even with the most advanced cleaning systems. Sometimes its operator error, but in many cases it’s the technology itself that can either malfunction or is inherently flawed. This concept is probably the hardest one to convey to potential buyers as a lot of noise exists around this topic.
4. Cost and ROI
Sticking to a budget still matters, and many companies need to strike the right balance between cleaning and capital investments. When we work with a client our goal is to make sure all costs are factored into their analysis. Besides the system cost, what consumables are required? What kind and how much waste gets generated? What is the cost of operation? Value of improved quality? Will I experience labor savings? What about the secondary benefits: less set up times; less rejects; better looking graphics; reduced ink costs, and so on….!
Nick Harvey: We want to explore every aspect, so our readers get your thoughts on the different cleaning methods out there. Let’s examine each approach, starting with soda and media blasting.
Jeff Paduano: Not too long ago there were two media blasting options to choose from: Soda or Plastic (Polymer) media. The latter method is not available anymore – turns out that process was really slow, and many times the plastic media would get stuck in the cells.
Soda Blasting does a very good job at removing many kinds of build-ups. This method is proven, and today shows up for most On-Press Cleaning applications. Today’s equipment is much simpler to operate and maintain, can fit into very tight spaces, and does not cost as much to run as people think.
Soda blasting does use compressed air to function, but it’s considered a very small amount compared to other pneumatic operated equipment found in most plants today. Soda consumption gets exaggerated at times – it’s become a really efficient process, and the generated waste is non-haz and land-fillable.
Another misconception about soda blasting is this method causes surface damage. Having the word “blast” in the name doesn’t help! However, the reality is soda is one of the softest medias available. Because it’s so soft, when a soda particle hits the roll surface (ceramic or chrome) it fractures upon impact. As it fractures, the original particle subdivides into even tinier crystals, allowing the soda to reach the bottom of even the smallest cells.
We have been involved with this method for over 3 decades because it does provide a way to do safe deep cleaning on so many different press types and avoids the use of harsh chemicals and disposal of hazardous waste.
Nick Harvey: Next, let's discuss the Jetwash method. It's a technique embraced by some major players in the industry. Could you share more about how this method works?
Jeff Paduano: The Jetwash method uses spray nozzles and a heated chemical solution to remove unwanted residues and build ups. Usually, these systems are effective on most ink residues, but coatings and film may take longer or require use of a harsher chemistry. Most of these systems have a wash, rinse and dry cycle, and can be left unattended while in cleaning mode. Although the equipment has become easier to use, it still requires a good amount of maintenance due to the hazardous nature of the chemical bath and the associated liquid waste Jetwash systems produce.
Nick Harvey: These units are found worldwide and achieve varying degrees of success. They've definitely gained popularity, but do you foresee a decline in their appeal anytime soon?
Jeff Paduano: We have already seen many companies pivot away from Jetwash systems and do believe this decline will continue. As stated, a Jetwash system may not be able to handle today’s unique coating formulations. On top of that, the cost of operating continues to climb. The chemicals needed for these units are very pricey, the cost to dispose the hazardous liquid waste adds up quickly, and the utility costs are steep – maintaining the solution tank at recommended temperatures takes more electricity than many people realize. Safety considerations also come into play when considering one of these systems – the chemicals used can burn someone’s skin or lungs if proper PPE is not utilized. Finally, this method does nothing to support any sustainability initiatives underway at most corporations.
Nick Harvey: Moving forward, let's shift our focus to ultrasonics. These systems have been around for quite some time, and I've encountered a wide range of opinions about them. Could you provide us with a comprehensive overview of ultrasonic anilox cleaning? Additionally, are all ultrasonic systems based on the same technology?
Jeff Paduano: Ultrasonic Systems have come a long way. In the past, they had a reputation for damaging cells and breaking down frequently. Today’s manufacturers have ironed out those quality issues, and for many narrow web shops this is a good method to employ. Smaller systems can fit onto a workbench – these units are automated and can typically clean multiple rolls at a time.
The tradeoff is the waste stream – it’s almost always classified as hazardous.
If a company is running sleeves, another issue to contend with is the importance of using end seals that are liquid tight. Failure to do so will result in roll damage, as the ultrasonic solution will migrate underneath the ceramic coating and cause delamination to occur.
I have also noticed some larger Ultrasonics in use at Wide Web plants and other coating operations. The bigger systems will obviously produce more waste and are not necessarily as effective as their smaller narrow-web cousins. Larger rolls require more time to clean so will expose a sleeve to potential damage should an end seal fail.
You also asked if Ultrasonics all use the same technology? Conceptually, yes – Ultrasonic cleaners use transducers to produce sound waves. It’s these sound waves that create the cleaning action, but the ultrasonic bath needs more than water to work – a chemical is added to the tank to boost cleaning effectiveness.
In the old days, the sound waves could easily become too strong and ruin a roll. As stated above, the industry has come a long way, and the amount of cleaning energy (aka cavitation) is much more precise and controllable.
Nick Harvey: Right. This topic is likely of significant interest to our readers - Laser Cleaners. This new technology is gaining traction among many users. What's your take on it?
Jeff Paduano: Yes, we do spend a lot of time these days fielding inquiries from all over the world regarding laser cleaning. It’s become a very popular subject with a lot of noise around it.
I started my journey with lasers about 10 years ago. Part of my research led me to Europe, where laser cleaning has existed for many more years vs. here in the States. It was during this time that I learned all about different scanners, power settings, laser source quality, laser classifications, and most importantly safety concerns.
Although we don’t have enough time to discuss it all today, I can offer some highlights so if someone is in the market for a Laser System they can approach their decision in an informed way:
-Scanners Matter!
Most industrial lasers use a linear laser. For roll cleaning, this kind of scanner can lead to damage because it leaves behind hot spots. Some companies are better than others in minimizing the thermal effects of their linear lasers, but it’s a real thing. When a linear laser malfunctions, it causes “micro-melting” of the cells. ARCS developed a system with a laser company that uses a rotary scanner – it never stops so it can’t leave behind any heat.
-Made in America Matters!
The lower cost laser systems on the market today utilize laser sources from China. Unfortunately, they don’t hold up over time. We rely on an American-made laser source that’s rated to maintain its intensity for up to 50k – 100k hours!
-Laser Watts + Pulse Frequency
This gets complicated, but through our extensive research we were able to confirm a 50-Watt system was necessary in order to target a wide variety of residues and clean at an acceptable rate. A larger laser source enables more cleaning options when combined with various pulse frequency settings. This is where I will stop, as explaining this key concept takes a while. But I do have a dedicated presentation around this topic and am happy to go through it with anyone who has an interest.
-Conclusion
Lasers are here to stay, but not all are created equal. To understand the technical differences involves a good amount of due diligence, site visits, and demos. We encourage people to visit us since they can see their roll being cleaned right before their eyes. It also allows for in-depth discussions on the technology and industry landscape.
Nick Harvey: Well thanks for running everything down. It’s been an education, even for me! As a final point, could you summarize for our readers the crucial importance of anilox cleaning and what they should consider when selecting a cleaner?
Jeff Paduano: Sure Nick…. I think we have made a compelling case for companies to pay more attention to the condition of their cylinders. Life is so much better when a good housekeeping program is put in place and reinforced from the top down. Today part of that program should include regular deep cleanings – no matter how good your operators are or how many times you run a wash cycle, eventually your cells will become plugged.
When considering a cleaning system for your plant, a few items to check right away is total cost of operation, including waste disposal. What method makes sense for my operation? On-Press or Off-Press OR Both? Do I need the precise cleaning Laser Systems offer or do one of the other methods meet my needs? What kind of support can I expect – is the equipment made overseas or domestically? Will it work for my future needs – can it remove even tougher substances than it does now?
One last thought – not all companies want to acquire another piece of capital equipment. Or they want to leave the deep cleaning to “The Professionals.” If exploring this route, make sure the service provider meets industry safety standards (Tappi-certified? ISNET Grade?). Check their references; speak to your roll reps for recommendations; start small; do they offer On-Site laser cleaning?
We service hundreds of clients in this fashion – some send their rolls to one of our locations for cleaning, and many times we will show up at their plant to do the work with either our portable laser system or soda system.
Nick Harvey: Finally, for readers considering an investment in an anilox cleaner, what advice would you offer? What key aspects should they evaluate in a system to ensure it is suitable for their needs and effective?
Jeff Paduano: Besides the above recommendations, my best advice is to assign someone who has a thorough understanding of production’s requirements and can make sure the plant’s priorities are kept at the forefront when evaluating the different options available today. Purchasing still must play a role in the decision-making process, but having a technical lead will ensure the right questions are asked and answered. If possible, go visit the equipment maker’s facility. See one of your rolls cleaned on their system. Can’t make the trip? Send them a roll and have them perform a 3D scan showing before and after images. Doing these steps can go a long way towards ensuring the right decision gets made.
Nick Harvey: Thank you very much for your time and the detailed insights. This has been a fascinating discussion that I'm confident will spark comments from our readers.
Jeff Paduano: Your welcome Nick! Thanks for having me – I always enjoy having the chance to share our industry insights and observations with as many people as we can, and your forum allows us to do just that!
In wrapping up our insightful exploration into the intricate world of anilox roll cleaning, it's evident that the journey toward selecting the ideal cleaning method is as complex as it is critical. This series has ventured beyond the basics, shedding light on the multifaceted considerations that printers must navigate to maintain operational efficiency and print quality. From the diverse methods discussed, including Ultrasonics, Chemical Wash systems, Baking Soda Blasting, and the increasingly popular Laser Cleaning, to the nuanced advice on daily, weekly, and monthly cleaning routines, it's clear there's no one-size-fits-all solution. Each method comes with its own set of benefits and challenges, tailored to different sector needs, from Corrugated to Label, Wide Web, and Coating operations.
Jeff Paduano's comprehensive insights underscore the evolving landscape of anilox roll cleaning, highlighting not just the technological advancements but also the pressing need for sustainability and efficiency in today's fast-paced market. As we've learned, the decision-making process for selecting an anilox cleaner involves a delicate balance of factors, including automation, cleaning quality, risk of roll damage, and the overall cost and return on investment.
In conclusion, the future of anilox roll cleaning lies in embracing innovation while recognizing the importance of a meticulous, informed approach to roll maintenance. Whether it's the precision of Laser Cleaners, the efficiency of Ultrasonic systems, or the adaptability of On-Press solutions, the goal remains the same: ensuring the longevity and performance of anilox rolls. As this blog has shown, staying informed and open to new technologies is key to navigating the complex terrain of anilox cleaning, making it possible to meet and exceed the demands of modern printing operations. The journey doesn't end here; it evolves with each technological stride and every piece of shared expertise, driving the industry toward a future where clarity, efficiency, and sustainability lead the way in anilox roll maintenance.
About Anilox Roll Cleaning Systems:
ARCS, a pioneer in anilox roll cleaning for over 35 years, has played a pivotal role in advancing the design and technology of modern roll cleaning systems. To date, our service division has successfully cleaned and restored well over 50,000 rolls.
Our dedicated service technicians bring a wealth of experience, with a collective 75+ years of expertise in cleaning printing rolls. We can come to your plant or ship your roll to one of our three locations for quick service.
For companies who want to own their own roll cleaning equipment, our proprietary Laser Cleaner stands as the gold standard, restoring cell volumes to ‘like-new’ condition without causing any surface damage. ARCS also offers a state-of-the-art Deep Cleaning Soda Blast System. Witnessing the remarkable cleaning power of both our Laser and Baking Soda systems often elicits a loud ‘WOW’ from first-time observers.
About Jeff Paduano:
Jeff Paduano is President and Owner of Anilox Roll Cleaning Systems, Inc., a 35-year-old Hatfield, PA based company with branch offices in Grand Rapids, MI and Greensboro, NC. ARCS is a turn-key supplier and manufacturer of advanced roll cleaning equipment and also offers roll cleaning services.
Since taking over in 2007, Jeff has led ARCS through a period of rapid growth over the years and today is the largest service provider in the States. Jeff earned a Bachelor of Science from SUNY Geneseo, and today belongs to both FTA and TAPPI.