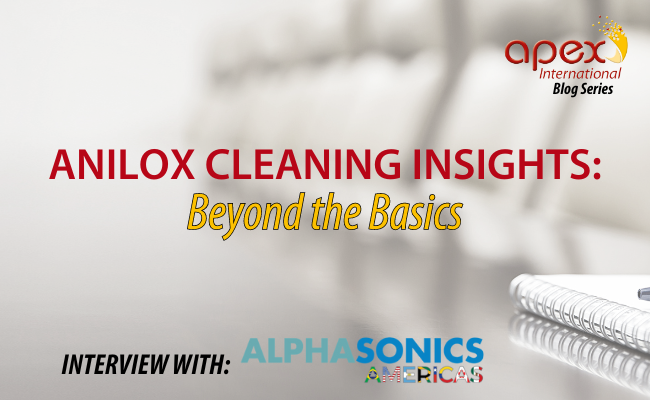
Welcome to the second installment of our blog series, where we continue our exploration into the world of anilox cleaning techniques. Throughout this ongoing series, we'll continue to feature discussions with industry-leading experts and provide direct insights from manufacturers.
In today's printing landscape, printers are still grappling with the challenge of identifying the most efficient cleaning method for their anilox rolls amidst a multitude of suppliers worldwide claiming to offer the ultimate solution. This complex landscape necessitates careful navigation to align cleaning methods with operational needs and budget constraints.
Once again, at the forefront of this ongoing discussion is Apex International, globally recognized as the largest supplier of anilox rolls. The question of identifying the optimal cleaning method for anilox rolls remains prevalent, with the response often proving elusive due to the diverse applications of anilox/metering rolls. With these rolls utilized across a wide spectrum of liquids, including water-based inks, UV inks, solvent-based inks, adhesives, latex, and more, the pursuit of a one-size-fits-all solution continues to challenge Apex and industry counterparts.
To provide further clarity on this critical topic, Nick Harvey, Apex International's Technical Director, has once again collaborated with key suppliers of anilox cleaning equipment. Together, they aim to delve deeper into different cleaning methods and offer expert advice on each product. Join us as we continue this enlightening journey into the complex world of anilox roll cleaning, sharing invaluable insights from industry leaders every step of the way.
Interview with Alphasonics Americas:
Nick Harvey: It's a pleasure to have this conversation with you. We're delighted to feature you in our blog series focusing on anilox care maintenance. Your active participation in industry discussions and forums is well-known.
Christopher Jones: Hi Nick. It’s a pleasure. Thanks for having me. It’s always great to provide thoughts and ideas on this topic and hopefully, it gives your customers a really clear picture of the anilox cleaning landscape.
Nick Harvey: As you know, the aim of this series is to give our customers first-hand Information on the main methods of anilox cleaning around the world today. What are your thoughts?
Christopher Jones: Well, there are a few methods that have come and gone over the years and some that have stood the test of time. Hand applied chemical cleaners have been ever present in print shops since the dawn of time but can only take people so far due to the limitations associated with a manual process.
Ultrasonics has been around for a while now as have jetwash units. We’re starting to see more laser cleaners enter the arena recently which claim to essentially are the perfect solution, but I’m sure we’ll get onto that…
Nick Harvey: Absolutely, this is the right platform to discuss and share your expert views openly. Do you think there's a significant distinction between everyday cleaning and deep cleaning processes, or is the essential outcome just about having a clean anilox?
Christopher Jones: There is no such thing as ‘deep cleaning’. You see and hear this phrase everywhere and it honestly drives me crazy! It’s either clean or it’s not clean. If a method can’t clean to 100%, it’s not good enough. There shouldn’t be any half measures and we really need to get away from that thinking as an industry and expect complete cleanliness from anilox cleaners.
Nick Harvey: That makes sense. We're interested in covering all angles to ensure our readers have a well-rounded understanding of the different cleaning strategies in use. Would you mind starting with your take on soda and media blasting as a cleaning method?
Christopher Jones: Well, these units are starting to die out now. The premise is the use of kinetic energy to essentially knock ink and contamination out of a cell. Decades ago, they did an OK job as anilox screen counts were generally lower across the board but as the industry has moved on, the method hasn’t been able to keep pace. The cells are too small these days to be effectively cleaned with media blasting and when you couple this with the fact this kinetic energy is absorbed by inks that are softer in nature, even when cells can be penetrated, it is unable to knock the contaminants out of a cell effectively.
It’s just a simple case that soda or media blasting is no longer “up to the job” these days. When you also consider that a lot of these systems are low capacity in terms of the number of rolls that can be cleaned simultaneously coupled with the mess these systems make with the dust created. This dust can actually get onto the press and cause print defects, rendering these systems not a viable option anymore. It’s unfortunately a case of the needs of the industry moving on and the soda blasting tech not being able keep up.
Nick Harvey: OK. So, a simple conclusion is that you believe the media blasting systems "old technology" are no longer fit for the purpose. Transitioning to another noteworthy approach, the Jetwash method has garnered attention from key players in the industry. Can you elaborate on the mechanics and importance of this method?
Christopher Jones: You know, there are a handful of well-established companies here in the U.S. I won't drop names, but you've probably come across them. Despite Europe witnessing a surge in businesses, ranging from small to multinational, transitioning towards tech-driven solutions for anilox cleaning, the Jetwash units still hold their ground in the States. These units use heated chemical cleaners and high-pressure water, delivered via pumps and spray nozzles. Plus, most of them come with rinse and dry features, adding to their appeal. Jetwash is losing its edge. Why? Well, it's simple. There's no real mechanical action involved in the cleaning process, and the chemicals tend to degrade faster than you'd expect. And let's not even get started on the costs. With most systems requiring 50% dilutions, they go through expensive cleaning fluids like there's no tomorrow, the expenses mount up very quickly. In my eyes this directly impacts a print shop’s margins and in turn, profit. There’s also the unfortunate fact that these units are a maintenance nightmare. Messy, temperamental, and a headache to fix without a service engineer on speed dial. I’m regularly meeting with operators that are frustrated, to say the least. And don't even get me started on the damage these systems inflict on gears and bearings. Despite all the promises, the reality is far from rosy.
Let's address the elephant in the room: "green" credentials. Sure, the chemicals may boast eco-friendly labels, but what about contaminated waste? Ink disposal is a real headache, and many end up in hot water with local authorities for improper disposal practices because they are led to believe that waste can go to drain when 99% of the time it cannot and should not. Whilst I may appear harsh here, let's not sugarcoat it—calling these units "technology" is a stretch. A pump and a spray nozzle hardly scream innovation. But hey, credit where it's due, some companies have built strong businesses around these units, especially here in the U.S. and that has to be admired. I would suggest that the historical growth and dominance of these systems is more due to the lack of competition than any form of ground-breaking technology.
Nick Harvey: That’s a strong opinion for sure. With their prevalence across the globe and differing levels of effectiveness, these units have unquestionably become more popular. Yet, do you envision a waning interest in them in the near future?
Christopher Jones: Indeed, they have. But it’s important to note that at Alphasonics we’ve never been beaten in any cleaning trial at a customer, anilox producer or press manufacturer that has carried out controlled assessments where Alphasonics and jetwash units have been put head-to-head.
As I said earlier, people are slowly but surely starting to move away from the units now. There is still some life in them yet, don’t get me wrong and in some instances, they do have their merits. Only a fool would say otherwise. That being said, in terms of where the method can go in terms of industry development, I’m not sure how this technology can develop any further in terms of what customers need and how aniloxes develop.
Nick Harvey: Thank you for your open thoughts, it’s always interesting to hear opinions from the leading companies in any field. Shifting our focus to an intriguing subject that our readers are sure to find compelling: laser cleaners. With this innovative technology gaining momentum among users, what are your thoughts on its implications and significance?
Christopher Jones: Certainly, this topic is of significant interest to many. The concept revolves around utilizing a focused laser beam to effectively remove or 'ablate' ink from cells with precision. While theoretically promising, current market solutions have not fully aligned with industry needs despite being marketed as the ultimate remedy for all anilox cleaning challenges.
Let's first address the claim of these units being 'green' and waste-free. The substantial power demands of laser units contradict such assertions. It's essential to consider the broader environmental impact beyond fluid-based alternatives. Laser units exhibit high energy consumption, leading to environmental and cost implications. Moreover, despite claims, there is indeed a waste product generated—ink and coating dust resulting from the laser's burning action.
Concerns extend to the physical setup of these units. Despite their sizable footprint, many systems have limited capacity, especially for operations with extensive anilox inventories. These systems require operational precision trained staff, introducing bottlenecks if qualified personnel are unavailable. Having one person constantly stood at a cleaning machine serves no print shop any good at all and creates time and cost implications. Furthermore, incorrect settings can lead to damage to both the internal cell structure and cell walls of the anilox, highlighting the meticulous control required in utilizing this technology.
They are not easy to use and pose risks to rolls. Reports indicate prolonged cleaning times as a consequence of operational challenges, such as power reduction settings to minimize the risk after extensive anilox damage has occurred. For instance, in Brazil, early adopters have faced significant frustration due to extensive cleaning durations, causing operational inefficiencies. The issue of damage has been a prevalent concern. Notably, one South American roll producer has chosen to void warranties if laser cleaners are used onsite, underlining the apprehensions of industry experts. The reluctance of anilox roll producers and laser engraving machine manufacturers to endorse these systems underscores the recognized risks and limitations associated with laser cleaning technology.
One would think they would jump on this train themselves if the technology was the perfect technology that marketing campaigns claim. Instead, true experts in lasers are wise to the true picture of the matter. It's crucial to grasp the inherent risks associated with ablation—the same process used in anilox engraving—presenting potential hazards in ink and ceramic vaporization. Of utmost concern are the carcinogenic nanoparticles produced during ink burning, posing potentially serious health risks to operators and surrounding personnel. Despite claims of sophisticated filtration systems, effectively removing these particles remains dubious, with the subsequent dust disposal raising further safety concerns.
Even if we play devil’s advocate here and assume these filtration systems are faultless, what happens to the filter itself when it needs to be changed? Do we put our operators at risk with the changing of the filter? Further to this, do we ignore the risks to workers at landfill sites? Simply because it’s left our facility, we should not just wash our hands of responsibility. This dust exists and has to go somewhere. That somewhere is not lungs,
The industry should not turn a blind eye to risks extending beyond production facilities, particularly with heightened scrutiny on packaging materials and waste management. We as an industry cannot engage in ‘NIMBY-ism’. The health risks associated with laser cleaners demand comprehensive research to mitigate dangers, ensuring safe disposal practices. Neglecting these risks could potentially lead to detrimental consequences, warranting urgent attention to safeguard industry and environmental health.
Nick Harvey: That is a lot of information to digest but let me offer some additional perspective. Apex International is recognized as the world's leading supplier of anilox and metering rolls, operating out of seven international manufacturing sites. Our facilities are equipped with over 30 lasers, enabling us to maintain continuous 24-hour production. This capability underscores our commitment to operational excellence.
It’s important to emphasize that our organization has thoroughly investigated the potential risks associated with Cr2/O3 particles. Our lasers are designed with significantly enhanced exhaust systems that ensure effective particle extraction, even during the highest levels of production. Moreover, our exclusive use of Cr2/O3 in engraving processes has undergone rigorous scrutiny concerning particle emissions. We are committed to strict safety standards and environmental responsibility, ensuring that our operations are not only efficient but also safe.
Regarding the risks associated with airborne particles during the burning of ink or coatings, which may include various layers, I acknowledge the complexities involved in ensuring 100% safety in such scenarios. However, the widespread adoption of this technology suggests a significant level of confidence in its safety and effectiveness. Could you elaborate on how these risks have been addressed given the widespread use of these technologies?
Christopher Jones: OK - before I go on, I realize that there really is a lot to go at here and please let me be clear, I am not laying this at the door of Apex or any anilox supplier for that matter. Experience and expertise mean that you and companies similar to you have the processes and safety precautions in place to responsibly deal with the harmful waste products I’m referring to. That is not in doubt so please don’t think for a moment I am lumping anilox suppliers into this. Not at all.
That being said, a lot of the suppliers of laser cleaning systems have marketing claims that really do appear too good to be true, making them hard to ignore. Let’s be honest, the expense, expertise and forethought anilox suppliers put into safety precautions cannot and will not be replicated to that extent in print shops. That’s a fact I think we can all agree on. To really do this correctly as anilox suppliers must do, it requires expense and complexity that an average print shop can neither afford nor is equipped to do. What this means is systems are in place which carry very real risks as if there is nothing to be concerned about. There is also the ‘Star Wars’ effect… people love lasers! This is a really appealing technology and application. So, this coupled that when people are told that they’ll solve every anilox cleaning they’ve ever had or will have, as if it’s the last anilox cleaner they’ll ever buy, the huge outlay is overlooked and indeed, customers are not given the true picture of the risks I’m referring to. Whether this is through lack of knowledge on behalf of the supplier or simply telling customers what they want to hear, it is clear that these systems have come into the market way too early.
Again, I need to be really clear that I’m not someone with an axe to grind and I am not trying to foul bad-mouth a competitor just to score points. I do, however, have a responsibility as a supplier to this industry to give this industry the real picture. Especially when it comes to potential health risks.
Nick Harvey: Well, I guess that’s the right thing to do from your perspective. It looks like as an industry we really need to learn more about what this equipment can and can’t do. We need some real data.
Christopher Jones: Exactly. I think they’ve been launched before being fully perfected and I worry that beyond the potential pitfalls in effectiveness and operational considerations, we will see health related issues coming to the fore sooner rather than later.
Nick Harvey: Let’s move on. Finally, let's delve into ultrasonic anilox cleaning. Tell us about Alphasonics as a company. With these systems having a long-standing presence and generating varied opinions, could you provide a thorough explanation of how ultrasonic cleaning operates in anilox cleaning? Additionally, do all ultrasonic systems rely on identical technology?
Christopher Jones: No problem. Alphasonics was started in Liverpool, U.K. in 1993 and we fully design, develop and manufacture all the equipment and the technology in it. We have around 3000 units in the field globally now and have highly successful partnerships worldwide with press and anilox manufacturers as well as other suppliers to the industry. We can clean any number of anilox rolls or sleeves at any face width, diameter and screen count without the need to remove any gears or bearings if present. We operate in labels, flexible packaging, corrugated and even vinyl flooring across both flexo and gravure. About 6 years ago, we opened an operation in the USA which is now called Alphasonics Americas. From this office we serve the entire Americas region
and pride ourselves on our technical excellence and expertise in both ultrasonics and flexography.
But we weren't the first to use ultrasonics for anilox cleaning of course. Ultrasonic cleaning for aniloxes has been around for a while since the early 1980’s. I’ll try and give the full picture without getting too technical. We’ve all heard the horror stories of aniloxes being damaged, which has led to the prevalence of other cleaning methods, especially in the U.S. However, the first and most important thing for people to remember, is that not all ultrasonic anilox cleaners are created equally. That’s something to really keep in mind when looking at this technology in the flexo arena.
Ultrasonic cleaning occurs in a heated tank of water that has transducers fixed to the underside of it. When current is applied to these transducers, the tank base flexes at an extremely high rate, which is too fast for the water to follow suit which creates a vacuum. When this flexure occurs, tiny vacuum chambers (or bubbles to you and me), are produced which are related to the size of that flex depending on the desired ultrasonic frequency. These chambers implode of the surface of the anilox which literally pulls contamination out of the anilox cells and within the fluid itself, causing a chemical cleaning reaction. This is called cavitation.
The problem with ultrasonics is that in its raw element, there is no uniformity and therefore can be extremely patchy. In its basic form, ultrasonics applied to fluid can create areas of high activity and low activity in the cleaning tank. ‘Hot spots’ are where too many ultrasonics are focused which can potentially damage an anilox and ‘cold spots’ occur where little or no cleaning will occur. Imagine it like cleaning a delicate sweater - if you clean one area only, you will wear a hole in it. This is the best way to illustrate this. To counteract this effect, a ‘sweeping circuit’ is built in which seeks to equalize the distribution of sound by sweeping either side of an average desired harmonic frequency. Essentially, the wider the sweep rate, the more consistent the distribution of sound. This is where the difference comes into play in terms of the brands on offer.
Alphasonics have a ‘super sweeping’ rate of +/- 12 kHz, the nearest competitor has +/-5 kHz with most systems on the market having much less.
This means two things:
1. The risk of damage is completely removed with our technology.
2. Effective cleaning to 100% of the aniloxes deliverable volume can be achieved consistently.
This is not the case with other suppliers who in most cases also use an average frequency of around 40-45 kHz, which we would deem too aggressive for anilox cleaning.
Nick Harvey: How does Alphasonics set itself apart from its competitors?
Christopher Jones: We purposefully call our technology ‘Medical Grade’ ultrasonics because the development of our technology that has been used to clean aniloxes has led us to enter the medical field for the cleaning of surgical equipment to remove infection causing proteins and bacteria. This is the level we are working at in comparison to the others in the industry.
Where we also differ is the fact we allow the user to utilize 1 of 2 ultrasonic frequencies depending on the regularity of cleaning. By allowing our customers to choose between 55 kHz and 98 kHz (low and high), thus giving them what can be best described as a ‘scrubbing brush’ and a ‘feather duster’. This means even high screen aniloxes can be safely cleaned often - even after every job, safely and effectively. Customers can clean as often as they like, or as little as they like without any limitations in terms of time. We even have the ability to allow our customers to utilize 4 ultrasonic frequencies where required, with two frequencies being applied simultaneously in the high or low settings. This is particularly suited to ‘HD Flexo’ and again, something others can’t provide.
The technology built into our systems seems complicated but is extremely simply to use due to a PLC system and simple control panel. At the touch of a button, an anilox is cleaned automatically at the correct time, temperature, power and frequency. This means that in theory any person in a pressroom could use our equipment, even with zero training or prior experience. To add to that, our systems only use 10% chemical, with the rest of the fluid being made up of water straight from the tap. We’re a cost-effective solution to buy and to run.
Alphasonics even have patented technologies to enhance the cleaning effect. For example, ‘Active Cavitation’ which increases the chemical cleaning effect of sonolysis. We even allow customers to fine tune the machine’s specification with a range of optional extras like automatic dosing, chemical monitoring and hard chroming of the base tank to essentially double the machine’s lifetime by preventing the naturally erosion caused by the transducer vibration. Again, this is the extra mile that isn’t available elsewhere.
The long and short of it is this: we are the only cleaning supplier that can offer written guarantees of not only performance but also safety. Neither of those written guarantees have ever been activated since our inception in ’93. We do what we say, by creating a solution tailor made exactly to the customer’s requirements. We’re able to do so because we’re in the best position to do it.
Nick Harvey: Well, you’ve given some real insight here. I’m sure that a lot of people reading this would have thought ultrasonic units all did the same thing.
Christopher Jones: Well, the theory is the same, it’s just that without the controls built in and the expertise to shape the technology to what the industry needs, you get vast variations in terms of capabilities and sadly, quality. That is why we’re at the top of the game both in terms of ultrasonic cleaning and anilox cleaning in general. As I mentioned earlier, we’ve never been beaten in a cleaning trial, anywhere in the world.
Nick Harvey: I appreciate the comprehensive overview you've provided. It's been an enriching conversation. As we wrap up, could you summarize the pivotal importance of anilox cleaning and provide recommendations for readers on key factors to evaluate when selecting a cleaner?
Christopher Jones: Control is everything Nick. As you know. I truly believe that there’s a fine line between the anilox and a company’s profit margin. By cleaning the anilox to 100% you can control what the anilox is capable of doing for longer periods. You have an anilox that goes to press correctly every time. When you consider that 80% of print production issues come from the condition of the anilox, the odds are in your favor. This means, you’re less likely to create waste in terms of ink or substrate, as well as time and money in putting the anilox right once the job has begun. You need to be able to achieve this 100% cleanliness consistently to maintain that control.
So, readers should ask themselves:
-
-
Can the system they choose clean rolls to this level every single time to control anilox but also how is the system itself controlled?
-
Do the features and benefits mean the system can run effectively for longer before fresh consumables are required or maintenance is needed?
-
Can control be achieved safely? For both the anilox and the operators of the equipment?
-
And finally, at what cost? Not only the cost of the system itself but in terms of the cost to introduce a skill to the business, price of consumables and fluid disposal and the costs to literally keep the machine switched on.
-
Do your research. Get as much information as you can in terms of facts, figures and data. Data doesn’t lie. Also, go speak to other users of the kit and not just the suppliers themselves. This way, you can truly get a first-hand account of whether the marketing message translates into real life. There’s no one size fits all solution. Do the leg work and you’ll find something that suits your needs exactly and will give you the very best in the long term, time after time.
Nick Harvey: Chris, I want to extend my appreciation for your time and the wealth of knowledge you've provided. Our discussion has been incredibly engaging, and I'm excited to see the reactions it sparks among our readers.
Christopher Jones: It was an absolute pleasure, Nick. I hope I’ve helped people learn a few things today.
We have journeyed deeper into the technological forefronts and discussed emerging challenges within the anilox cleaning landscape. Our dialogue with industry experts such as Nick Harvey from Apex International and Christopher Jones from Alphasonics Americas has illuminated the ongoing evolution and diversification of cleaning technologies—from the traditional methods to the cutting-edge laser and ultrasonic technologies.
As we conclude this part of our series, it is clear that the quest for the optimal anilox cleaning solution remains dynamic and complex. Each method comes with its own set of benefits and limitations, tailored to different operational requirements and environmental considerations. This discussion not only underscores the importance of choosing the right cleaning technology but also highlights the need for ongoing innovation and adaptation in response to evolving industry demands and environmental regulations. Our exploration has shown that while there is no one-size-fits-all solution, the key to effective anilox roll maintenance lies in understanding the specific needs of your operation and the capabilities of various cleaning systems. As we move forward, we encourage our readers to engage actively with suppliers, seek out comprehensive data, and consider both the efficiency and environmental impact of their chosen solutions.
Stay tuned for the next installment and thank you for joining us on this enlightening journey. We look forward to continuing this conversation in our upcoming posts.
About Alphasonics Americas:
Alphasonics, part of the global network since 2018 and formerly known as Alphasonics USA, serves all regions across North, Latin, and South America with a focus on delivering the highest standards in cleanliness and safety for the flexographic printing industry. With over 30 years of experience, we specialize in manufacturing bespoke ultrasonic cleaning systems and Anilox Roll Cleaning Systems, featuring unique patented technologies for unmatched performance and durability.
Our systems efficiently remove a wide range of contaminants, such as ink, varnishes, and oils, ensuring safe and effective cleaning. As a family-owned and operated group, Alphasonics prides itself on innovation, technical excellence, and a robust global presence. We cater to specific industry standards with quality and consistency, offering tailor-made cleaning solutions to enhance print quality and profitability.
About Christopher Jones:
Christopher D. Jones holds the position of Vice President at Alphasonics Americas and possesses Master’s degrees in Advanced Marketing from Aberystwyth University and Business Administration from Liverpool University. Since entering the flexographic printing industry in 2010, Christopher has cultivated a profound passion for the sector, continuously expanding his knowledge through scholarly pursuits and interaction with both print shops and industry peers.
At Alphasonics, he is dedicated to driving excellence by advancing technological innovations and building strong global relationships by taking the time to understand the unique requirements of every customer and partner. Christopher’s approach goes beyond merely selling anilox cleaners; he aims to foster growth and innovation alongside clients and co-suppliers through industry leadership and proactive engagement. He values integrity and diligence in all areas of life, including his personal interests in boxing, soccer, music, culture, and technology. Committed to offering his expertise and enthusiasm, Christopher supports a diverse range of clients, from multinational corporations to local family-owned businesses across the Americas. He and the Alphasonics team stand ready to collaborate.