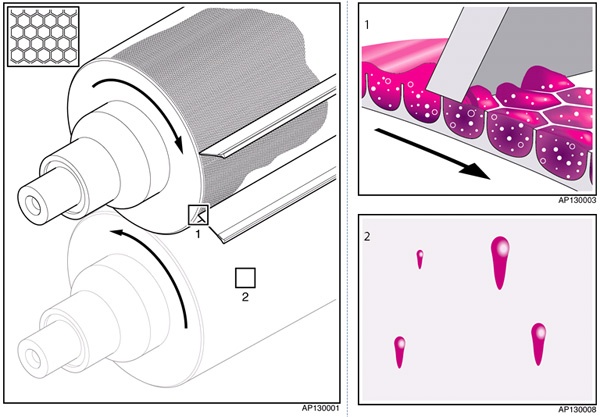
UV inks are considered by many to be the most popular in the narrow-web space. And for good reason. Print results with UV inks are consistently better than those using water or solvent-based inks. But the use of UV inks is not without its challenges. Chief among those challenges is the issue of spitting.
There are several theories as to why spitting occurs with UV inks and not with water or solvent inks. Generally, these revolve around the higher viscosity of UV inks comparied to water or solvent and the impact it has on the doctor blade. Specifically, the higher viscosity can move the blade just enough to allow more ink than is intended to slip through. Other theories suggest that anilox cell type, viscosity, press speed and doctor blade specifications all play a role. Regardless, the results can be a disaster, particularly at high speeds.
While exactly why spitting occurs is a subject for debate, what is not in dispute is that the relationship between doctor blade and anilox is at the core. If spitting is creating a challenge in your shop, try these tips for better print results:
1. A stiffer doctor blade may prevent excess ink from getting under and transfering to the plate and substrate.
Testing shows a thicker blade will minimize UV spitting because they resists hydroplaning and do not allow texcess ink to transfer to the anilox.
2. Try a 30° anilox cell with openings
The ink can move through the openings in the anilox cell walls preventing ink from being built up onto the back of the doctor blade. (Situation 1a).
A word of caution: This solution is only temporary. Because the roll will wear over time, the openings will become smaller and eventually disappear. So over time you will get the same situation as with the regular anilox roll. Ink will built up at the back of the doctor blade (situation 1b).
3. Try GTT Channel engravings.
There is no pressure built up at the doctor blade because the ink can move through the GTT channels. Therefore no ink builds up onto the back of the doctor blade and no ink drops from the doctor blade onto the flexographic plate or substrate.
Comments from users:
Niklas Olsson - Global Brand Manager Flint Group - Inks division:
“We know Apex International GTT rolls from our co-operation within the REVO Digital Flexo project, where our R&D teams worked closely together in order to create the ultimate ink-transfer for a consistent and repeatable print job. We also have GTT rolls in our demo center in Sweden already for more than 2 years. The open-slalom S-shape severely reduces and is our strongly recommended remedy to overcome UV ink spitting, whether we use Low-migration inks or conventional UV inks. We would advice GTT as thé solution to solve UV Spitting!”.
Christophe Vossaert - St. Luc Labels & Packaging - Belgium:
“Considerable production hours were lost in switching anilox rolls in an attempt to eliminate our UV Spitting problem. The solution that resolved the spitting, literally overnight, was Apex GTT technology. We began with a trial on one of our presses, and after good results of consistent HD-flexo print quality and gain in production time, the decision was made to convert all flexo presses to GTT. From day one, our press operators were very happy with the switch to the Apex GTT-technology,” said Christophe Vossaert, Business Development Manager of St-Luc Labels & Packaging.”